Welcome, Guest |
You have to register before you can post on our site.
|
Forum Statistics |
» Members: 466
» Latest member: Charvab
» Forum threads: 1,441
» Forum posts: 2,615
Full Statistics
|
Online Users |
There are currently 20 online users. » 0 Member(s) | 19 Guest(s) Bing
|
Latest Threads |
Bedava Free Fire Hesap
Forum: My Forum
Last Post: Tanitim2025
01-01-2023, 01:02 PM
» Replies: 0
» Views: 0
|
Bedava Pubg Mobile Hesap
Forum: My Forum
Last Post: Tanitim2025
01-01-2023, 12:49 PM
» Replies: 0
» Views: 0
|
Bedava Hesaplar
Forum: My Forum
Last Post: Tanitim2025
10-20-2022, 07:51 AM
» Replies: 0
» Views: 0
|
Film izle
Forum: My Forum
Last Post: Tanitim2025
08-27-2022, 05:16 AM
» Replies: 0
» Views: 0
|
Ehliyet Sınav Soruları
Forum: My Forum
Last Post: Tanitim2025
08-14-2022, 03:13 PM
» Replies: 0
» Views: 0
|
Seo Hizmetleri
Forum: My Forum
Last Post: Tanitim2025
05-22-2022, 02:08 PM
» Replies: 0
» Views: 0
|
شراء عقار في تركيا
Forum: My Forum
Last Post: Tanitim2025
04-30-2022, 11:57 AM
» Replies: 0
» Views: 0
|
Propriété à vendre à Turq...
Forum: My Forum
Last Post: Tanitim2025
04-27-2022, 10:50 AM
» Replies: 0
» Views: 0
|
Apple benefits elma yemen...
Forum: My Forum
Last Post: Tanitim2025
04-16-2022, 10:23 PM
» Replies: 0
» Views: 0
|
CLOUD TÜRKIYE Bulutların ...
Forum: My Forum
Last Post: Tanitim2025
04-13-2022, 04:05 PM
» Replies: 0
» Views: 0
|
|
|
Cotton or Polycotton Fabric |
Posted by: tfg004 - 08-13-2021, 08:13 AM - Forum: My Forum
- No Replies
|
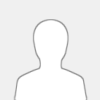 |
When shopping for clothes, consumers are presented with a wide range to choose from. The combination of fabrics, styles, and different manufacturers can make the choice a daunting one. Two of the more popular fabrics for clothes are 100% cotton fabric and polycotton fabric. But which is the best choice? In short, that depends on what the buyer is looking for.
So, what are the differences between 100% cotton and poly-cotton blend fabrics? To start with, a poly-cotton blend is just what its name suggests: a fabric that is made up of cotton and polyester fibers. The ratio varies, with 65% cotton and 35% polyester being the most common. 50/50 blends are also easily found. The blend is designed to afford the advantages of both the cotton and polyester fibers into one fabric.
What are the advantages and disadvantages of cotton?
100% cotton is a fully breathable fabric, which means that it can be cooler to wear in hot conditions. However, as the thickness increases, the breathability decreases. 100% cotton tends to rip and wear out easily, depending on the weave. Cotton canvas is a very durable and abrasion-resistant fabric, but it is very thick and heavy. In regards to safety, cotton fibers that have not been treated for fire resistance will tend to burn away where polyester will melt. As a natural fiber, 100% cotton garments also tend to be a bit more expensive than their synthetic counterparts.
Polyester has an equal number of advantages and disadvantages as cotton
Polyester does not breathe and has a tendency to stick to the skin once perspiration begins. In regard to durability, polyester is a more elastic fiber and therefore tends to be tear resistant. However, it does not tend to be as abrasion-resistant as cotton canvas. As polyester is not dependent upon the forces of nature for a successful harvest, it is usually considerably cheaper than 100% cotton.
A fabric made from a polycotton blend combines the strengths of the two fibers. Polycotton garments are breathable, tear-resistant, and can be fashioned into abrasion-resistant fabrics, like canvas. While not as inexpensive as pure polyester, polycotton blends do tend to cost less than comparable garments made of 100% cotton and they provide much more comfort. The previously mentioned 65/35 blend of cotton and polyester is the most popular for work garments, particularly because of price, durability and a larger color selection is available for purchase. When shopping for work garments, the choice between 100% cotton and polycotton blends depends largely on the work environment and personal preference. If employees work indoors around machinery, the tear-resistance of polycotton may be favorable. If the work is in an outdoor setting, particularly in hot climates, 100% cotton fabric could be the better choice. Before deciding, make sure to take all environmental factors into consideration.
It is the intention of this article to help shed some light on the different types of fabric characteristics of 100% cotton and poly cotton fabric. We are hoping to share our thoughts with you in order for you to make a more informed decision when choosing the fabric type for your garments.
If you’ve ever wondered what’s the difference between water-resistant and water-repellent or between water-repellent and waterproof or between water-resistant and waterproof textiles and clothing, you’ve come to the right place.
The main function of outdoor clothing is to provide protection against environmental factors. In a wet environment, the basic requirement for clothing is to keep the wearer dry. Therefore, the outer layer of your clothing, as well as your gloves or mitts, need to resist moisture. But what are the main terms regarding this? What do they really mean? Is there any difference between them? If so, what’s the difference? Here, we’ll try to answer these and many other questions regarding water-repellent, water-resistant, and waterproof fabrics and clothing.
In contact with water, water-repellent materials form beads on the outside that can be easily removed from the fabric surface. This means that water can’t easily penetrate the material; however, for longer contact with water or with a higher pressure difference, the material will absorb water. Water-repellent fabrics are often compact textile structures or common materials treated with hydrophobic chemicals. Although water-resistant and water-repellent are often used interchangeably, there’s a difference as water-resistant fabrics will resist wetting by water for longer. Waterproofing of a material is defined as the property of a material not to be penetrated by fluids, i.e. a waterproof material must be impervious to water.
Tencel fabric is a popular fabric of choice for eco-conscious clothing brands. It’s light and versatile, and used in everything from casual wear to underwear to activewear. But what impact does it have on people, the planet, and animals? Is Tencel ethical and sustainable? We’ve put together a cheatsheet to help demystify this fabric and put the power back in your hands. Tencel is a type of rayon, like viscose and modal. These cellulose fibres are all made in a similar way: by dissolving wood pulp and using a special drying process called spinning. Before drying, the wood chips are mixed with a solvent to produce a wet mixture. This mixture is then pushed through small holes to form threads, chemically treated, then the lengths of fibre are spun into yarn and woven into cloth.
Table linen fabric is a fabric that can be reused, including tablecloths, napkins, placemats, table skirts and napkins.
Table napkins are a small piece of table linen that is used to wipe the mouth and to cover the lap in order to protect clothing or place mats, which serve as a table linen for an individual place setting. Linen napkins, especially those with a vibrant color, are often used to transform a table from the ordinary to special.
A tablecloth is used to cover a table. They can be ornamental coverings, as well as a provider of protection from scratches and stains. Other tablecloths are designed to be spread on a dining table before laying out tableware and food. Tablecloths are standard covering for a restaurant dining table and in many homeowners formal dinner tables and are often high quality, bright white linen or cotton cloth. Some of the most popular types of tablecloth fabric include cotton, polyester and linen tablecloths. Polyester tablecloths are easy to wipe down and clean and are often found in casual dining restaurants.
Lightweight cotton fabrics come in a variety of weights from sheer to semi-sheer. You can see lines from the cutting table (or your hand) underneath the sheer fabric. This means fashionable sheer cotton dresses must be lined with lining fabric. They can also be worn with a camisole or an underbody. Not all lightweight kinds of cotton are sheer. Some darker and/or printed fabrics go with regular lingerie.
Fabrics like cotton gauze and cotton voile fold nicely and make airy dresses with a drapery. A gauze also has some crinkle to it so it is often used for making tunics, tops, swimsuit cover-ups etc. Cotton lawn fabrics are a little more of semi-sheer, closer to opaque. Liberty is probably the most popular and favourite brand. They are super soft and really wearable especially after being washed.
High thread count Egyptian cotton bedding sheets fabric is a very popular item in the luxury bedding category recently. Fabric thread counts have spiraled to dizzying heights, and now range from 180 to 1500. Traditional wisdom counsels that fabric increases in softness as thread count increases, so shoppers gravitate toward high numbers when making their final purchasing decision. However, the rules for determining quality fabrics in the marketplace has changed. You can no longer make an apple-to-apple comparison between two bed sheet sets based strictly on thread count numbers.
|
|
|
The Different Types of Tablet Packing Machines |
Posted by: tfg004 - 08-13-2021, 08:12 AM - Forum: My Forum
- No Replies
|
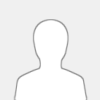 |
Packaging machinery is one of the vital equipment in the pharmaceutical industry, food processing, and chemical industries among which blister packaging machines are widely used for packaging capsules, pills, tablets, suppositories, etc. We can get an effective and safe packaging of tablets from a tablet press or capsules from capsule filling with the help of a blister packing machine. It contians different types for different use, such as pharmaceutical blister packing machine, food blister packaging machine, etc. The blister packing machine is designed for packing the different products (tablets, strong or delicate gelatin capsules, and so forth) into a blister.
A wide variety of tablet packaging machines are available from different manufacturers. A high-speed machine that is ideal for different products such as tablets, dragees or capsules. Machines are robust and well constructed and generally provide high quality by using accurate temperature control, and the ability to exert variable pressure on the sealing rollers. A strip packaging machine is ideal for coating heat sealable films such as polymer-coated aluminum foil, cellophane and polymer-coated paper.
The process of strip packing entails the packaging of pharmaceutical products consisting of lozenges, tablets, capsules, etc. between two sheets of heat-sealable foil like paper-poly and aluminum-poly.
You seal the pharmaceutical product inside pockets created within two, continually moving foil sheets.
The area about the pockets creates a hermetic seal hence providing a specific shelf life to the items contained within it.
An automatic cartoning machine is a device that you can use to make special carton packages for different products. The machine involves an integration of light, electrical, air, and mechanical configurations to make a carton for different products. Since the machine is fully automatic, most of the controls are under a computer control system that regulates its operations.
Capsule filling machines are used to fill empty capsules with substances, such as medicines or nutrients and are available in both personal and professional formats. Personal capsule filling machines are often manual or semi-automatic and used for families or for one's own use at an office and allow individuals to easily fill their capsules with the necessary medication. They are also often used by compounders to customize medication based on a patient’s specific need. Professional machines are designed for production or scientific use and can efficiently and safely produce thousands of capsules in a single hour. Fully automatic capsule filling machines must accurately fill capsules repeatedly, often with extremely low dosage weights.
|
|
|
Food additives |
Posted by: kkkdd5s - 08-12-2021, 09:00 AM - Forum: My Forum
- No Replies
|
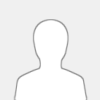 |
Food additives are chemicals added to foods to keep them fresh or to enhance their colour, flavour or texture. They may include food colourings (such as tartrazine or cochineal), flavour enhancers (such as MSG) or a range of preservatives.
Safety tests for food additives
Food Standards Australia New Zealand (FSANZ) is responsible for the approval of which food additives are allowed in Australian foods. All food additives used in Australia undergo a safety assessment, which includes rigorous testing before they are approved.
Toxicological tests on animals are used to determine the amount of the additive that is expected to be safe when consumed by humans. This is usually an amount 100 times less than the maximum daily dose at which ‘no observable effects’ are produced by an additive consumed over the test animal’s lifetime.
If there is any doubt over the safety of an additive, approval is not given. If new scientific information becomes available suggesting that a food additive is no longer safe, the approval to use the food additive would be withdrawn.
Most food additives are tested in isolation, rather than in combination with other additives. The long-term effects of consuming a combination of different additives are currently unknown.
Plant Extracts: The Original Food Additives
Plant and herb extracts have long been used to enhance the healthfulness, color, and even taste and flavor of foods, beverages and supplements. With an often “natural” positioning, their popularity is assured.
Ginny Bank, Contributing Editor
October 2011/NutraSolutions -- In 399 BC, the Greek philosopher Socrates was executed by drinking an infusion of the poisonous hemlock plant. In ancient Egypt, Cleopatra used henbane extract to dilate her eyes and make her appear more alluring. Also in Egypt, red fabric found in the tomb of King Tut contained alizarin, a pigment extracted from the roots of the madder plant. While such historical accounts documenting human use of plant-based extracts can be traced back over 3,000 years, their use is possibly as old as civilization itself. From the very first Chinese dynasties, Mesopotamia and ancient Greece, and westward to the empires of Mesoamerica, early civilizations had a surprisingly sophisticated understanding of botanicals and their extracts, especially for use as medicine. Flowers, fruits, roots, bark and leaves of plant material were extracted by various techniques to concentrate not only their therapeutic properties, but also their pigments, aromas and flavors. The simplest method of extraction, used for plants that have high oil content, was the expression of the essential oils. Other techniques included steeping the plant part in water to make an infusion (also known as a tisane) or mashing them and boiling in water to make a decoction. This method was also used to make natural dyes, sometimes boiling the decoction for days to concentrate the pigments further. Elixirs were produced by extracting the plant parts in alcoholic beverages to dissolve the active components.
Today, the use of plant extracts to flavor, color and improve health are not that different from ancient times. Even the extraction methods are fundamentally the same. And, with hundreds, if not thousands, of years of traditional use behind many plant extracts, their safety (and often their efficacy) has been well-documented. Even so, when one takes into account the massive number of plant-based extracts used in traditional medicinal systems, such as Ayurveda and traditional Chinese medicine, very few are approved for use in foods or have Generally Recognized as Safe (GRAS) status. This may be changing, as self-affirmation of GRAS status for such ingredients is steadily increasing. Within the last 18 months alone, a number of extracts received GRAS status through self-affirmation, with or without FDA notification
Pharmaceutical manufacturing is a strictly regulated, process-driven industry. A mistake in manufacturing can be costly in the best-case scenario and at worst, it can be life-threatening, particularly if a product has reached consumers.
The industry must adhere to numerous guidelines that are laid out by the Food & Drug Administration (FDA), for example, the Current Good Manufacturing Practices (cGMP). Product quality is at the center of cGMP, which assures the correct monitoring, design, and control of manufacturing facilities and processes.
cGMP also supplies guidance for how to attain quality raw materials, in addition to the preferred management processes and systems for maintaining optimum laboratory testing procedures. All factors play a key part in the effectiveness and safety of pharmaceutical raw materials.
For manufacturers, adherence to cGMP is a necessity, and while quality and safety are top priorities in the pharmaceutical industry, these guidelines do introduce more challenges in the manufacturing process.
Medical apparatus and instruments refer to instruments, instruments, implants, extracorporeal reagents or similar or related items used to diagnose, prevent or treat diseases or other medical conditions, and are not achieved by chemical effects (such as drugs) in the body or in the body Its purpose. The main goal of any medical device is to improve the patient’s daily quality of life or well-being during diagnosis, treatment, and/or medication. Over the last decade, the medical device industry is a fast-growing and demanding industry. Advances in design, materials, and technologies have increased the potential to develop improved solutions for all medical applications. These advances have managed to supply the clinicians with new products, tools, and procedures, supporting them in their work by making surgery, diagnosis, or treatment processes easier than ever before. These advances have also aimed to reduce both lead times and costs in the production of existing medical devices, reducing global healthcare costs. Due to this fact, medical devices are a hot topic among the industrial and academic domains regarding issues such as design, materials, prototypes, or manufacturing processes.
[font="Open Sans", sans-serif]Fine and specialty chemicals are a not sharply defined chemical substances that are usually produced in small quantities and on special customer request. Fine chemicals are chemical substances that are obtained by means of complex syntheses and have a guaranteed degree of purity. Specialty chemicals is the broader term and generally includes chemical substances for special applications where the effect is what counts most. [/font]
You can use disposable protective gloves to protect your hands from any kind of hazard. There are three main types of disposable safety gloves. There are latex gloves, which are manufactured from natural rubber. Nitrile gloves are produced from synthetic nitrile rubber. And vinyl gloves are made from synthetic plastic polymer. Whichever type of glove you decide to use, you should always ensure that it is suitable for your kind of industrial application. Disposable gloves are usually manufactured with a service grading. The service grade of a disposable glove indicates the type of industry that it should be used. This article looks at the various uses of disposable gloves according to industry.
Medical Usage
Disposable safety gloves are some of the most commonly used safety products in the healthcare industry. These gloves are worn to prevent cross-contamination between patients and medical staff. They are also used for general hand protection when handling various sensitive things in a medical setting. Disposable gloves that are used in the healthcare industry are referred to as medical gloves. Medical disposable gloves are tested and approved by the U.S. Food and Drug Administration (FDA). These gloves are worn by surgeons, doctors, laboratory technicians, nurses, caregivers, dentists and all other medical personnel. Blue disposable gloves are most popular for healthcare use, but you can also get medical safety gloves in various shades of pink, purple, and even grey. These gloves undergo several rounds of testing including leak and puncture testing, and visual defect examination. The FDA allows only premium grade medical safety gloves to be marketed.
Food Service Usage
There are special disposable gloves for use in the food service industry and restaurants. These gloves are also tested and approved by the FDA. Food service gloves are worn by chefs, waiters, and various hospitality personnel. Food service gloves are used to prevent cross-contaminating during food preparation and service. Like the medical disposable gloves discussed above, food service gloves undergo serious testing before they can hit the market. Food service gloves are usually white in color to Accenture the cleanliness or sterility of the hospitality industry.
|
|
|
Some packaging types to consider |
Posted by: kkkdd5s - 08-12-2021, 08:59 AM - Forum: My Forum
- No Replies
|
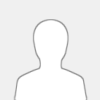 |
Remember the feeling when you picked up your first iPhone? Taking off the plastic seal and feeling the sleek white box? By touching the box for the very first time you already felt the importance, quality & significance of this device. This is no coincidence! We meticulously strategized how they were going to package their product to align with their branding of providing top of the line product innovation & consumer experience!
It is clear that packaging plays a large role in the perceived value of a product and as a whole, the packaging industry really hasn’t changed too much in the past years, compared to the constant innovations made in portable technology. With all the packaging and box choices available in today’s market, it often becomes difficult to select the most appropriate packaging solution for your product. Let’s take a look at some of the different types of packaging options you can use to enhance your product & customer experience!
1. Cardboard boxes
Paperboard is a paper-based material that is lightweight, yet strong. It can be easily cut and manipulated to create custom shapes and structures. These characteristics make it ideal to be used in personalized packaging. It is made by turning fibrous materials that come from wood or from recycled waste paper into pulp, and then bleaching it. Paperboard packaging comes in various grades, each suitable for different packaging requirements.
SBS (or solid bleached sulfate) paperboard can be used for packing cosmetics, medicines, milk and juice, cosmetics, frozen food and more. Choosing kraft, or CUK (coated unbleached kraft) paperboard packaging are for those who prefer the natural and environmentally-friendly look of recycled paper, which can be used for similar packaging applications. Kraft is often seen to be less resistant to moisture, making it less suitable for food-related products, or frozen-goods packaging. With the right combination of design options, paperboard packaging can look high-end, without high-end pricing.
2. Corrugated boxes
Corrugated boxes simply refer to what is commonly known as: Cardboard. Corrugated boxes are the ones many probably consider as ‘cardboard’ as it produces the large shipping, shoe & storage boxes. What a lot of people do not realize is that corrugated boxes also come in different types depending on the durability and strength of the box. Identifying a certain corrugated material, however, is easy. How do you determine the material? Through its corrugated medium (also known as fluting). Identifying a corrugated material is easy. It consists of 3 layers of paper, an outside liner, an inside liner and a corrugated medium (also known as fluting). The corrugated medium that gives it strength and rigidity.
3. PVC boxes
Plastic is used in a wide range of products, from spaceships to paper clips. A number of traditional materials, such as wood, leather, glass, ceramic, and so on, have already been replaced by plastic. PVC box packaging has many advantages in which they can be recycled, and generally they are much more durable than paperboard boxes. Airtight plastic packaging containers can help to preserve the quality of food and eliminate any contamination issues. Plastic packaging also does not break easily and can be stored with food under extreme conditions.
Another reason why plastic is a popular choice for packing material is because of its ability to showcase the product at any angle without necessarily opening the packaging. It is also flexible, lightweight and can be applied with films or coating to enhance packaging appearance.
Contrary to popular belief, plastic is in fact recyclable, in the sense that it takes less energy to produce new plastic, compared to glass, and other materials. Best of all, it is very cost effective!
4. Paper tube packaging
Paper tube packaging is becoming popular globally. It provides a unique packaging alternative. Paper tube packaging is lightweight that makes it easier to transport. They also provide good protection to the packaged product from damage and contamination. It is also eco-friendly and thus contributes to conserving the environment. Paper tube packaging is being widely used in different industries like cosmetics, food products, etc.
The packaging industry has seen a move towards sustainable packaging. Product packaging that is not eco-friendly creates unnecessary junk that ends up either in landfills or into ocean beds. Such packaging is harmful to the environment. Customers are becoming more aware of the dangers of non-degradable packaging and are preferring products using eco-friendly packaging.
Paper tube packaging is 100% eco-friendly. It is biodegradable and does not leave behind harmful packaging waste. Paper tube packaging can be easily recycled which saves a lot of energy and resources that would have gone into preparing fresh packaging. Using paper tube packaging helps you to position your brand and product as eco-friendly. This will provide you a competitive edge in the market and attract more customers into buying your product.
5. Paper bags
Paper bags have been part of trade and commerce for more than centuries. Traditionally cloth and jute bags were used to pack goods in larger quantities during its transfer from manufacturer or farms to retailers and shopkeepers then used the paper bags to distribute smaller quantity goods to end customers. In fact, paper bags are still used by small food retailers like – sweetshop owners, street food vendors, bakers and by small vegetable sellers.
On the other hand, a waterproof paper gift bag’s structural firmness and surface feature made it ideal to print high-quality images, logo, designs better as compared to a plastic bag, and that made paper bags a hit for fashion, luxury and premium gift packaging industry.
This trend has gained popularity owing to the people and businesses becoming more aware of the ecological surroundings. Also, several individuals want to use paper bags because they are easy to carry, clean and can hold items for a good duration of time.
|
|
|
Material Handling Equipment: Why Steel Containers |
Posted by: kkkdd5s - 08-12-2021, 08:58 AM - Forum: My Forum
- No Replies
|
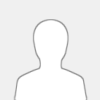 |
As you can imagine, there are several ways to move, stack, carry, store and prep material when deciding upon the correct material handling equipment. This may seem a bit more simplistic than it is but, in general, it takes a lot of consideration when creating the specific product material flow. Additionally, there are a lot of choices when it comes to the equipment used to move material, store it and potentially assemble it.
Material handling equipment can be any apparatus that helps move, store, protect and even control material. The options seem limitless.
Categories of Material Handling Equipment
There are four generalized categories of material handling equipment. The first is wire container. Generally, it consists of the JP wire containers and EU mesh containers.
The next category of material handling equipment is any roll container.
The third category of material handling equipment consists of pallet containers.
The last material handling equipment category refers to storage racking systems.
Determining the Right Container for Material Handling
When companies purchase containers for material handling, they tend to shop based on container type, size and availability. The size of the container depends on required holding capacity and the footprint of shop storage space. This is generally the starting point for many purchasing departments who receive specifications from their shop personnel for container use.
Pallet racks have played an essential role in maximizing storage capacity at warehouses and distribution centers for decades. An important part of industrial pallet racking design is the selection of rack decking, which acts as a base for storing cases or non-palletized items in conjunction with palletized products. By increasing the number of contact points between the product being stored and the storage media, decking reduces the chance of products falling – increasing overall warehouse safety. Naturally, not all decking solutions are created equal. One of the most versatile and popular choices, and the topic of this article, is wire decking.
If you’ve decided wire decking is the best option for your warehouse or distribution center, you still need to decide which options will work best. Below are 4 things to consider when selecting the best wire decking for your application.
1. What are you storing?
The most important factors when selecting wire decking are the weights and overall dimensions of the products that will be stored on it. Unless specifically designed to do so, wire decking is not intended to support the full weight of a pallet (point load) and can warp or collapse under the pressure. This creates a significant safety risk and is one of the most common mistakes we see in the field.
2. How will you be using your wire decking?
Will you be storing full pallets, individual pieces of equipment, or loose cases? Pallet racking can accommodate all the above, but it is important you consider the overall use of decking in your design. One very common use of wire decking is the storage of individual cases. Some companies refer to this as “hand stack”. If this is your intended use, you should consider increasing the density of the wire mesh grid. Standard grid densities are typically 2”x4”, 2.4”x4” or 2.5”x4.5”. When “hand stacking,” consider selecting a grid size of 1”x2” or 1”x4”. There are also design enhancements that can be incorporated into wire decking to help with your specific application. For example, the 90-degree turn at the front and rear edges of the wire deck, called waterfalls, can be configured upwards to help prevent products from sliding off the deck. There are also different accessories like dividers that clip onto the wire deck itself to help with organization. If your intended use is order picking, you could also consider sloping the wire decking to make it easier to access products.
3. In what type of storage media will the wire decking be going?
Are these wire decks for bulk shelving or pallet box? If the answer is pallet racking, is it roll-formed or structural? Manufacturers can differ slightly on the overall dimensions of their beams (horizontal members) and uprights (vertical members), so it’s important to check the sizing to ensure a good fit. Bastian Solutions has many years of experience working with all pallet racking manufacturers and can help in this selection process.
4. In what environment will the wire decking be going?
Is the wire decking going into a freezer or cooler? Will it be stored outside or in a facility where food is present? In most applications, a standard paint finish of backed on or powder coated enamel is fine. However, in environments where moisture or oxidation are concerns, galvanized or stainless steel should be considered.
Another consideration is whether wire deck channels should be inverted or flipped upside down. By inverting the wire decking channel, you can help mitigate the buildup of moisture, dust, dirt and other debris. This practice is commonly found in the food storage industry to promote a cleaner environment.
|
|
|
Enabling a circular economy for chemicals in plastics |
Posted by: pd123d - 08-11-2021, 09:02 AM - Forum: My Forum
- No Replies
|
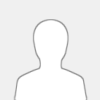 |
[font=NexusSerif, Georgia, "Times New Roman", Times, STIXGeneral, "Cambria Math", "Lucida Sans Unicode", "Microsoft Sans Serif", "Segoe UI Symbol", "Arial Unicode MS", serif]Enabling a circular economy for plastics in Europe and beyond is an ambitious goal. To reach a fully closed loop, numerous challenges and knowledge gaps need to be overcome. This review provides a list of more than 6000 chemicals reported to be found in plastics and an overview of the challenges and gaps in assessing their impacts on the environment and human health along the life cycle of plastic products. We further identified 1518 plastic-related chemicals of concern, which should be prioritized for substitution by safer alternatives. At last, we propose five policy recommendations, including the need of a global and overarching regulatory framework for plastics and related chemicals, in support of a circular economy for plastics and of target 12.4 of the UN Sustainable Development Goals.[/font]
[font=NexusSerif, Georgia, "Times New Roman", Times, STIXGeneral, "Cambria Math", "Lucida Sans Unicode", "Microsoft Sans Serif", "Segoe UI Symbol", "Arial Unicode MS", serif]State of knowledge of chemicals in plastics[/font]
[font=NexusSerif, Georgia, "Times New Roman", Times, STIXGeneral, "Cambria Math", "Lucida Sans Unicode", "Microsoft Sans Serif", "Segoe UI Symbol", "Arial Unicode MS", serif]Overview of chemical additives[/font]
[font=NexusSerif, Georgia, "Times New Roman", Times, STIXGeneral, "Cambria Math", "Lucida Sans Unicode", "Microsoft Sans Serif", "Segoe UI Symbol", "Arial Unicode MS", serif]The production of chemicals for plastics is continuously increasing in terms of both quantity and diversity, with several thousand chemicals used across many material applications. Estimating global additives production is not an easy task, because these data are usually not publicly available. However, with a global plastic production of 368 Mt in 2019, and assuming 1–10% additives mass fraction for nonfibre plastics, the total amount of additives used in 2019 might be around 20 (3.6–36.8) Mt. If plastic production follows current increasing trends, it is estimated that we will have produced 2000 Mt of additives by the end of 2050. Plasticizers are the most used additives and together with flame retardants cover almost 50% of globally applied additives. Owing to their wide-ranging application and high-production volumes, these two types of additives have been receiving special attention (e.g. Commission Regulation (EU) 2018/2005).[/font]
[font=NexusSerif, Georgia, "Times New Roman", Times, STIXGeneral, "Cambria Math", "Lucida Sans Unicode", "Microsoft Sans Serif", "Segoe UI Symbol", "Arial Unicode MS", serif]Additives are applied during the production process at different concentrations based on the specific function that they need to fulfil. It provides an overview of functions, typical material application, chemical classes, and application ranges. For example, plasticizer application ranges vary across materials, and can reach up to 60–70% of the plastic mass in soft PVC resin products. Other additives are usually applied at much lower concentrations, such as 0.7–25% for flame retardants or 0.05–5% for stabilizers and antioxidants. The concentration of unintentional residues is typically <1%. Generally, it is accepted to consider as NIAS only compounds with a mass <1000 Da, assuming that substances with a higher molecular weight cannot be absorbed in the body (EU No 10/2011, although there might be some uptake in the gut).[/font]
[font=NexusSerif, Georgia, "Times New Roman", Times, STIXGeneral, "Cambria Math", "Lucida Sans Unicode", "Microsoft Sans Serif", "Segoe UI Symbol", "Arial Unicode MS", serif]Chemicals reported in plastics[/font]
[font=NexusSerif, Georgia, "Times New Roman", Times, STIXGeneral, "Cambria Math", "Lucida Sans Unicode", "Microsoft Sans Serif", "Segoe UI Symbol", "Arial Unicode MS", serif]As of today, there is no publicly available database containing a complete and detailed list of chemicals used in the various plastic products, specifying typical function, plastic types, and mass fraction ranges. In an attempt to provide such an overview, we used the mapping of plastic additives conducted by the European Chemical Agency (ECHA), and expanded it with data from 35 additional sources. The considered sources include—amongst others—Annex I of Commission Regulation (EU) No 10/2011, also called the Union list, which is a positive list of monomers and additives authorized for use in plastic-based food contact materials, the work conducted by Groh et al., and the Chemicals and Product Categories database (CPCat; actor.epa.gov/cpcat), which contains information across different categories and materials[/font]
[font=NexusSerif, Georgia, "Times New Roman", Times, STIXGeneral, "Cambria Math", "Lucida Sans Unicode", "Microsoft Sans Serif", "Segoe UI Symbol", "Arial Unicode MS", serif]As a result, It provides a list of more than 6000 functional additives, pigments and other substances found (both currently and in the past) in plastics. For each substance, we provide CAS number, main chemical function, typical application range, and polymer type (when available). For building the data set, we checked and harmonized where needed the reported chemical names, CAS numbers, and functions. Chemicals were classified according to their specific function in plastic materials based on the information reported in the considered sources. Wherever such information was missing, we retrieved the function from other references.[/font]
[font=NexusSerif, Georgia, "Times New Roman", Times, STIXGeneral, "Cambria Math", "Lucida Sans Unicode", "Microsoft Sans Serif", "Segoe UI Symbol", "Arial Unicode MS", serif]It aims at providing a comprehensive overview of chemicals found in plastics across different polymers and product applications. It contains various types of substances reported to be found in plastics; consequently, it is not limited to additives but also includes NIAS, solvents, unreacted monomers, starting substances, and processing aids.[/font]
[font=NexusSerif, Georgia, "Times New Roman", Times, STIXGeneral, "Cambria Math", "Lucida Sans Unicode", "Microsoft Sans Serif", "Segoe UI Symbol", "Arial Unicode MS", serif]Challenges and gaps in assessing plastic-related chemicals’ impacts in a circularity context[/font]
[font=NexusSerif, Georgia, "Times New Roman", Times, STIXGeneral, "Cambria Math", "Lucida Sans Unicode", "Microsoft Sans Serif", "Segoe UI Symbol", "Arial Unicode MS", serif]The goal of a circular economy is to move.[/font]
[font=NexusSerif, Georgia, "Times New Roman", Times, STIXGeneral, "Cambria Math", "Lucida Sans Unicode", "Microsoft Sans Serif", "Segoe UI Symbol", "Arial Unicode MS", serif]Sodium carbonate, activated carbon and copper-impregnated aluminium are used to absorb the sulphur without the use of water. They give efficiencies of absorption of 85–90% and have the advantage of not cooling the stack gases. The gases will then rise upwards from the top of the stack and disperse more widely in the atmosphere.[/font]
[font=NexusSerif, Georgia, "Times New Roman", Times, STIXGeneral, "Cambria Math", "Lucida Sans Unicode", "Microsoft Sans Serif", "Segoe UI Symbol", "Arial Unicode MS", serif]Food packaging is of high societal value because it conserves and protects food, makes food transportable and conveys information to consumers. It is also relevant for marketing, which is of economic significance. Other types of food contact articles, such as storage containers, processing equipment and filling lines, are also important for food production and food supply. Food contact articles are made up of one or multiple different food contact materials and consist of food contact chemicals. However, food contact chemicals transfer from all types of food contact materials and articles into food and, consequently, are taken up by humans. Here we highlight topics of concern based on scientific findings showing that food contact materials and articles are a relevant exposure pathway for known hazardous substances as well as for a plethora of toxicologically uncharacterized chemicals, both intentionally and non-intentionally added. We describe areas of certainty, like the fact that chemicals migrate from food contact articles into food, and uncertainty, for example unidentified chemicals migrating into food. Current safety assessment of food contact chemicals is ineffective at protecting human health. In addition, society is striving for waste reduction with a focus on food packaging. As a result, solutions are being developed toward reuse, recycling or alternative (non-plastic) materials. However, the critical aspect of chemicals for food safety is often ignored. Developing solutions for improving the safety of food contact chemicals and for tackling the circular economy must include current scientific knowledge. This cannot be done in isolation but must include all relevant experts and stakeholders. Therefore, we provide an overview of areas of concern and related activities that will improve the safety of food contact articles and support a circular economy. Our aim is to initiate a broader discussion involving scientists with relevant expertise but not currently working on food contact materials, and decision makers and influencers addressing single-use food packaging due to environmental concerns. Ultimately, we aim to support science-based decision making in the interest of improving public health. Notably, reducing exposure to hazardous food contact chemicals contributes to the prevention of associated chronic diseases in the human population.[/font]
[font=NexusSerif, Georgia, "Times New Roman", Times, STIXGeneral, "Cambria Math", "Lucida Sans Unicode", "Microsoft Sans Serif", "Segoe UI Symbol", "Arial Unicode MS", serif]Titanium dioxide is odourless and absorbent. Its most important function in powder form is as a widely used pigment for lending whiteness and opacity. Titanium dioxide has been used as a bleaching and opacifying agent in porcelain enamels, giving them brightness, hardness, and acid resistance.[/font]
We supply innovative specialty chemicals for textile leathe and related industries that include dyes, pretreatment, bleaching, finishing, coating and special effects products. Our commercial and technical teams will provide you with unparalleled sales support to fit your needs and keep you in the loop with the latest market developments.
We provide high quality raw materials, sourced from leading global manufacturers, as well as a wide range of value-added services including formulation advice, lab support, sampling, and professional handling and delivery of your products.
[font=NexusSerif, Georgia, "Times New Roman", Times, STIXGeneral, "Cambria Math", "Lucida Sans Unicode", "Microsoft Sans Serif", "Segoe UI Symbol", "Arial Unicode MS", serif]The addition of water treatment chemicals has always been considered as a standard operation in water and wastewater treatment. The concentration of chemicals was usually kept to the minimum necessary to achieve a good quality of potable or otherwise treated water. A significant interruption to the status-quo occurred more than 20 years ago after a severe and highly publicized outbreak of Cryptosporidium parvum oocysts. The strategic planning after the outbreak was to shift from physical-chemical to physical treatment methods, such as membrane filtration and UV disinfection. As such, the new procedures were supposed to eliminate the threat of water contamination through a minor addition of chemicals. Such was the mistrust and disappointment with water treatment chemicals themselves.[/font]
[font=NexusSerif, Georgia, "Times New Roman", Times, STIXGeneral, "Cambria Math", "Lucida Sans Unicode", "Microsoft Sans Serif", "Segoe UI Symbol", "Arial Unicode MS", serif]Indeed, water treatment technologies, such as chemicals for water treatment, are now using novel physical treatment methods. Membranes largely replaced granular filtration, and UV is paving the way towards minimization or elimination of the use of classic disinfection chemicals, such as chlorine and its derivatives. Yet, far from the “high-tech” revolution in water treatment technologies actually reducing the use of chemicals, the latter has in fact been significantly increased. The “conventional” chemicals used for pre-treatment, disinfection, corrosion prevention, softening and algae bloom depression are all still in place. Furthermore, new groups of chemicals such as biocides, chelating agents and fouling cleaners are currently used to supplement them. These latter are the chemicals needed to protect the high-tech equipment, to optimize the treatment, and to clean the equipment between uses.[/font]
[font=NexusSerif, Georgia, "Times New Roman", Times, STIXGeneral, "Cambria Math", "Lucida Sans Unicode", "Microsoft Sans Serif", "Segoe UI Symbol", "Arial Unicode MS", serif]The health effects of the new chemicals introduced into water are yet to be fully established. Typically, a higher treatment efficiency requires effective chemicals, yet these are not always environmentally friendly. It seems obvious that the “high-tech” revolution currently affects the sustainability of water resources, and certainly not in a completely positive way. In short, the adverse effects of the introduction of such a significant amount of treatment chemicals into our sources of water are yet to be evaluated.[/font]
[font=NexusSerif, Georgia, "Times New Roman", Times, STIXGeneral, "Cambria Math", "Lucida Sans Unicode", "Microsoft Sans Serif", "Segoe UI Symbol", "Arial Unicode MS", serif]Employees in printing industries can be exposed to multiple solvents in their work environment, like all sorts of chemicals for paint and print. The objectives of this study were to investigate the critical components of chemical solvents by analyzing the components of the solvents and collecting the Safety data sheets (SDSs), and to evaluate the hazard communication implementation status in printing industries.[/font]
|
|
|
Brief on Features and Applications of Solvent Dyes, and The Chemistry of Pigments |
Posted by: pd123d - 08-11-2021, 08:59 AM - Forum: My Forum
- No Replies
|
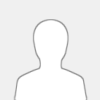 |
The selection of solvent for preparing a working electrode (and to act as the electrolyte) is known to influence the efficiency of dye-sensitized solar cells. In this topical review, results taken from a systematic study are presented from the authors’ own lab examining how protic and aprotic solvents, as well as solvent polarity, affect adsorption of carboxylic dyes on the titanium dioxide nanoparticle surface and electron injection from the dye to the semiconductor. Adsorption of dye molecules on nanoparticle surfaces is measured through second harmonic light scattering and electron injection through ultrafast transient mid-infrared absorption. It is revealed that protic solvents do not allow direct adsorption of the dye onto the semiconductor surface, due to hydrogen bonding with the dye and competitive binding to the semiconductor surface. Aprotic solvents, on the other hand, support solvation of the dye molecules but also facilitate dye adsorption on the semiconductor nanoparticle. Among aprotic solvents, it is found that solvents with higher polarity result in larger adsorption free energy for the dye and faster electron injection. Overall, these studies reveal that aprotic solvents with high solvent polarity (such as acetonitrile) yield more efficient solar cell devices.
The world of dyes and pigments is vast and there are innumerable varieties of these colorants to fulfill the requirements of varied industrial and commercial sectors. Acid dyes, basic dyes, solvent dyes, lake colors, pigment colors are just to name a few from the vast ocean of colors. This article will talk in brief about the solvent dye.
Solvent dye is a dye that is soluble in plastics or organic solvents. When it goes with an organic solvent the dyeing process occurs in a solution. As the molecules of solvent dyes have a very small polarity or none at all there is no ionization involved in the dyeing process as it does, say, with acid dyes. Solvent dyes are normally water insoluble. One commonly used organic solvent with solvent dyes that is non-polar is petrol.
As for the naming of solvent dyes a standardized pattern is followed. In the pattern, the first word is always ‘solvent’ which is followed by the dye color and then a distinguishing number. For example, the varied shades of red are segregated by the distinct number that comes after the shade name like ‘Solvent Red 49’, ‘Solvent Red 1’, and ‘Solvent Red 24’ and so on. Another example of the shade red occurring in another type of dye is Pigment Red 48 which is an azo derivative from naphthalene.
Solvent dyes are pretty versatile and have found their way into a number of applications. One of their common uses is in the automotive sector to impart color to petrol fuel and other lubricants. Varied hydrocarbon based non-polar materials such as waxes and candles, coatings and wood stains are colored with the aid of solvent dyes. In the printing industry they go towards marking inkjet inks, inks and glass coloration. Textile printing is followed by the media industry where the solvent dyes are used for magazines and newspapers.
Dyeing of plastics is another application which uses solvent dyes because of its chemical compatibility. In the plastics industry these dyes lend color to a number of solid materials like nylon, acetates, polyester, PVC, acrylics, PETP, PMMA, styrene monomers, polystyrene and other fiber. They are also increasingly being used for smoke signaling in the pyrotechnics industry. A mention has to be made of its application in scientific research and medical diagnostics. Here, the solvent dye is used as an important component to produce stains that help in identification of varied components in a cell structure.
There are several advantages offered by solvent dyes that have led to its wide use in varied applications. Color shade consistency, superior light fastness, resistance to migration, good thermal stability, extremely dissolvable in plastics and lack of precipitation even after extensive storage are just to name some of its superior attributes.
However, sourcing solvent dyes from reputed solvent dyes manufacturers is highly important. This guarantees you the quality of the product and its effectiveness in the application it shall be used for. There are several reputed manufactures of these dyes and the names can be easily obtained from the online yellow pages.
At the heart of every drop of paint, every thread of cloth, every bit of your brightly colored phone case is a pigment. Pigments are the compounds added to materials to give them color. This deceptively simple application has shaped our perception of the world via art, fashion, and even computer displays and medicine. Pigments are used in paints, inks, plastic applications, fabrics, cosmetics, and food.
Some of the earliest chemistry was to make and isolate pigments for paints, and pigment conservation is a focus for many modern researchers who identify and preserve artwork.
Get to know pigments
But what is a organic pigment, exactly? Pigments are brightly colored, insoluble powders (brightly colored liquids are called dyes). In most cases, the bright color is a result of the material absorbing light in the visible spectrum. In inorganic pigments, this absorption is the result of charge transfer between a metal (transition metals are really good at this); organic pigments tend to have conjugated double bonds that absorb visible wavelengths.
|
|
|
Comparing Castings and Forgings |
Posted by: pd123d - 08-11-2021, 08:58 AM - Forum: My Forum
- No Replies
|
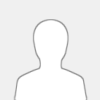 |
Many cell types will grow when attached to a rigid surface but not in suspension, a phenomenon termed „anchorage dependence”︁. Anchorage dependence can be studied by incorporating solid particles of varying size into gels. It has been found that colonies will form on glass fibrils 500 μ in length, but not in the presence of silica fragments smaller than the cells. This shows that the suspending medium is not itself inhibitory, and confirms the requirement for a rigid surface of adequate size.
The state of inhibited cells in suspension culture was examined by dispersing them in a methyl cellulose gel, in vessels lined with agar. In this system aggregation is prevented and the cells may be recovered quantitatively. Normal, as well as transformed, cells increase in size, and a proportion synthetize DNA during the first 24 hours in suspension culture. Growth and DNA synthesis in normal cells then virtually cease, while transformed cells continue to grow into colonies. The stationary normal cells remain competent for further growth for at least a week in suspension. When such cells are allowed to attach to a rigid surface in the presence of colchicine, DNA synthesis occurs and is followed by mitosis. These results indicate that suspended cells are blocked between mitosis and the end of the S phase of the cycle.
Anchorage Classification
To anchor is to hold or resist the movement of an object; anchorage is the gaining of that hold. In orthodontics, terms such as “critical anchorage”, “noncritical anchorage”, or “burning anchorage” are often used to describe the degree of difficulty of space closure. Anchorage may be defined as the amount of movement of the posterior teeth (molars, premolars) to close the extraction space (Fig. 10-1A) in order to achieve selected treatment goals. Therefore, the barrier anchorage needs of an individual treatment plan could vary from absolutely no permitted mesial movement of the molars/premolars (or even distal movement of the molars required) to complete space closure by protraction of the posterior teeth.
When designing large structural components it’s critical to make an informed decision between castings and forgings. The following paper by Rexnord provides an in-depth examination.
Material selection is one of the most crucial decisions made in the design, manufacture, and application of large structural components. Material selection naturally influences the entire performance of the design, and thus it is critical that informed decisions are made during the design stage. Steel castings and steel forgings are two alternatives for large structural components. For many design engineers it is often assumed that a forging is a better product because it is formed or worked during the manufacturing process. It also assumed that castings are inferior because they may contain porosity. Nothing could be further from the truth. Each process has its advantages and disadvantages. It is just as possible to produce an inferior product whether it is a forging or a casting. This paper will present an honest evaluation of castings and mining forgings, so that those in the design community can make an informed choice.
|
|
|
A Buyer's Guide to LED Tube Lights |
Posted by: pd123d - 08-11-2021, 08:57 AM - Forum: My Forum
- No Replies
|
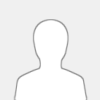 |
[font="Open Sans", verdana, arial, sans-serif]Replacing your fluorescent tube lights with LED retrofits can be a confusing and daunting process. We've put together this guide to demystify all of the ins and outs of replacing your fluorescent tubes with LED tube lights.[/font]
[font="Open Sans", verdana, arial, sans-serif]1) Advantages of LED tubes over fluorescent tubes
[font="Open Sans", verdana, arial, sans-serif]The many advantages of LED tubes over fluorescents are covered quite extensively, so we won't go into depth, but the three primary advantages are:[/font][/font] - Higher efficiency, energy savings (up to 30-50%)
- Longer lifetimes (typically 50k hours)
- No mercury
[font="Open Sans", verdana, arial, sans-serif]2) Fluorescent tubes sizes and LED tube light retrofitting
[font="Open Sans", verdana, arial, sans-serif]Because fluorescent fixtures are often mounted into ceilings and connected directly to mains electricity, they are relatively expensive and difficult to replace completely.[/font]
[font="Open Sans", verdana, arial, sans-serif]As a result, it oftentimes makes the most economical sense to simply use the same fluorescent fixture, but replace the fluorescent tube with an LED tube light.[/font]
[font="Open Sans", verdana, arial, sans-serif]Therefore, it is important to understand the types of fluorescent tubes that were developed, so that the correct LED panel light can be retrofitted in place.[/font]
[font="Open Sans", verdana, arial, sans-serif]Over the years, fluorescent tube manufacturers developed many varieties of sizes and types.[/font][/font]- T8 4-ft: Four-foot T8 fluorescent lamps are the most commonly used type today. They are 48 inches in length, and have a 1 inch lamp diameter.
- T12 4-ft: Four-foot T12 fluorescent lamps are less efficient compared to T8 lamps. They are the same length as T8 lamps, but have a larger 1.5 inch lamp diameter.
- T5 4-ft: Four-foot T5 fluorescent lamps are typically the most efficient, and some of the newest types of lamps introduced in the 2000's in the USA. They are commonly designated T5HO (high output) and provide more brightness than their T8 counterparts. They are slightly shorter than four feet (45.8 inches). T5 lamps come in a variety of lengths such as 1-ft, 2-ft and 3-ft versions and are commonly used in non-ceiling fixtures such as table lamps.
[font="Open Sans", verdana, arial, sans-serif]T8 and T12 tubes are also available in other lengths such as 8-ft tubes, but 4-ft lengths remain the most common types.
[font="Open Sans", verdana, arial, sans-serif]LED tube lights replicate the mechanical dimensions to ensure that they can be true retrofit replacements, and adopt the same form factor names (e.g. 4-foot T8 LED tube light).[/font]
[font="Open Sans", verdana, arial, sans-serif]T8 and T12 fixtures are generally the same length and use the same pins, so mechanically they are usually cross-compatible.[/font]
[font="Open Sans", verdana, arial, sans-serif]T5 fixtures are NOT cross-compatible with T8 and T12 lamps due to their different pin sizes and actual length.[/font]
[font="Open Sans", verdana, arial, sans-serif]3) Fluorescent ballasts and LED tri-proof light retrofitting[/font]
[font="Open Sans", verdana, arial, sans-serif]All fluorescent tube lights use a device called a ballast to regulate the lamp's brightness as it warms up. These devices are necessary for fluorescent lamps, and differ from incandescent lamps which can be connected directly to mains electrical circuits.[/font]
[font="Open Sans", verdana, arial, sans-serif]Fluorescent lamp fixtures typically house the ballast inside the fixture, and is not accessible without removing the fixture from the ceiling. Alterations to the fluorescent lamp ballast should be done only by those comfortable and knowledgeable with electrical work.[/font][/font]
Today LED high bay lights deliver equal or better lighting performance with only a fraction of the energy consumption of the traditional fluorescent tube LED flood lights. LED tube is the newest product line in the tube family made up of white LED chip modules. Provided with the advantages of long life-span, radiation-free, energy saving, environmental friendly.
Once you learn about the benefits of LED tube lights, you will see and understand why they are a positive choice for anyone looking to improve the environment with their lighting choices. In this Article, we will be comparing LED linear Lighting and traditional Fluorescent Tube Light by following characteristics
|
|
|
How Does a Drill Bit Work? |
Posted by: pd123d - 08-11-2021, 08:55 AM - Forum: My Forum
- No Replies
|
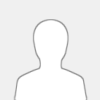 |
A drill bit is what actually cuts into the rock when drilling an oil or gas well. Located at the tip of the drillstring, below the drill collar and the drill pipe, the drill bit is a rotating apparatus that usually consists of two or three cones made up of the hardest of materials (usually steel, tungsten carbide, and/or synthetic or natural diamonds) and sharp teeth that cut into the rock and sediment below.
In contrast to percussion drilling, which consists of continuously dropping a heavy weight in the wellbore to chip away at the rock, rotary drilling uses a electric hammer drill bit to grind, cut, scrape and crush the rock at the bottom of the well. The most popular choice for drilling for oil and gas, rotary drilling includes a drill bit, drill collar, drilling fluid, rotating equipment, hoisting apparatus and prime mover.
The prime mover is the power source for the drilling, while the hoisting equipment handles lifting the drill pipe to either insert it into the well or lift it out of the well. Rotating equipment is what sets the whole system in motion. Before the early 1900s, drilling equipment was spun using livestock and a wooden wheel, but now, the rotating equipment is put in motion by a rotary table, which is connected to a square-shaped hollow stem, called a Kelly. Connected to the Kelly is the drill collar, which puts pressure and weight on the drill bit to make it drill through the rock and sediment. Capping off the drillstring is the drill bit, and encompassing the drilling process is drilling fluid, which helps to provide buoyancy to the drill string, lubricate the drilling process and remove cuttings from the wellbore.
Types Of Drill Bits
There are a number of different types of drill bits. Steel Tooth Rotary Bits are the most common types of drill bits, while Insert Bits are steel tooth bit with tungsten carbide inserts. Polycrystalline Diamond Compact Bits use synthetic diamonds attached to the carbide inserts. Forty to 50 times stronger than steel bits, Diamond Bits have industrial diamonds implanted in them to drill extremely hard surfaces. Additionally, hybrids of these types of drill bits exist to tackle specific drilling challenges.
Various drilling designs are also employed for different results, including core bits, which gather formation cores for well logging; mill bits, which help to remove cuttings from the well; and fishtail bits, which enlarge the drill hole above the drill bit.
Different configurations work better on different formations; so a number of different drill bits may be inserted and used on one well. Additionally, drill bits have to be changed due to wear and tear. Drilling engineers choose the drill bits according to the type of formations encountered, whether or not directional drilling is required, for specific temperatures, and if well logging is being done.
When a drill bit, like a masonry drill bit, has to be changed, the drill pipe (typically in 30-feet increments) is hoisted out of the well, until the complete drill string has been removed from the well. Once the drill bit has been changed, the complete drill string is again lowered into the well.
Cutting metal with cutting wheels
Plenty of manual cutting applications call for a hand-held grinder and cutting wheel. Cutting sheet metal, sizing a piece for fabrication, cutting out a weld to refabricate it, and cutting and notching in pipeline work are just a few examples of what can be accomplished using a grinder and cutting wheel.
[font="IBM Plex Sans", sans-serif]Resinoid-bonded cutting wheels are a popular choice to achieve these types of cuts because they offer portability and allow you to cut in many different angles and orientations. The bonding agent, in this case resinoid, holds the wheel together so it can cut effectively. The bond wears away as the abrasive grains wear and are expelled so new sharp grains are exposed.[/font]
[font="IBM Plex Sans", sans-serif]By following a few best practices, you can extend wheel life, promote safety, and improve productivity and efficiency within the process.[/font]
[font="IBM Plex Sans", sans-serif]The Basics of Cutting Wheels[/font]
[font="IBM Plex Sans", sans-serif]The main considerations in using resin cutting wheels include the cutting application, the tool being used—such as a right-angle grinder, die grinder, or chop saw—desired cutting action with diamond saw blade, the material being cut, and space. Wheels typically provide a fast cutting action, long life, and tend to be cost-effective.[/font]
[font="IBM Plex Sans", sans-serif]The two main types of resinoid-bonded abrasive cutting wheels are Type 1, which are flat, and Type 27, which have a raised hub. Type 1 wheels generally are used for straight-on cutting on electric or pneumatic right-angle grinders or die grinders and chop saws, among other tools. Type 27 wheels are required when there is some type of interference and the wheel needs to be raised up from the base of the grinder, but personal preference also plays a role in the decision. They are most commonly used with electric or pneumatic right-angle grinders.[/font]
[font="IBM Plex Sans", sans-serif]Resinoid-bonded abrasive cutting wheels are available in various sizes and thicknesses. The most popular range is 2 to 16 inches in diameter, and common thicknesses are from 0.045 in. to 1⁄8 in. Thinner wheels remove less material during the cut.[/font]
[font="IBM Plex Sans", sans-serif]Some types of wheels cut faster than others. The abrasive material used in the wheel is one influencer on cut rate and consumable life. Wheels come in several grain options, such as aluminum oxide, silicon carbide, zirconia alumina, ceramic alumina, and combinations of these materials.[/font]
[font="IBM Plex Sans", sans-serif]While not as sharp as other grains, aluminum oxide provides toughness and good performance for cutting on steel. Silicon carbide, on the other hand, is a very sharp grain but not quite as tough, making it suitable for cutting nonferrous metals. Zirconia alumina is a self-sharpening, tough, durable grain that holds up well in a range of demanding applications. Ceramic alumina also is designed to self-sharpen as it “breaks” at predetermined points to maintain a consistent cut rate and long life.[/font]
[font="IBM Plex Sans", sans-serif]When selecting a resinoid-bonded abrasive wheel, consider that products made with a mixture of zirconia or ceramic alumina with a harder bond typically cost more but offer durability and longer consumable life.[/font]
[font="IBM Plex Sans", sans-serif]Make sure to refer to the manufacturer’s recommendations, product descriptions, and RPM ratings to select the proper wheel size and bonded abrasive material for your application. Matching the size and RPM rating of the tool to the size and RPM rating of the wheel is critical for safe and effective usage. Choosing the tool with the greatest amperage or amount of torque while staying within size and RPM requirements of the wheel will increase performance.[/font]
[font="IBM Plex Sans", sans-serif]The kind of tool and the tool guard that you use also are factors that play a role in the type of wheel that can be used for an application. A larger-diameter wheel works best if you’re cutting deep into metal or need to cut a piece with a large diameter, for example, because it eliminates the need to rock the wheel back and forth during the cutting process. Look for a wheel with the diameter designed for the size and thickness of material being cut.[/font]
[font="IBM Plex Sans", sans-serif]Thin wheels, on the other hand, tend to remove less metal during the cut and have shorter life spans, but provide a quicker cut. There are some exceptions to this as different versions of thin wheels are lasting longer, so be sure to do your research before you make a final decision to ensure the wheel you select maximizes efficiency.[/font]
[font="IBM Plex Sans", sans-serif]Specialty cutting wheels are also available that are designed for use with certain materials, such as stainless steel and aluminum.[/font]
[font="IBM Plex Sans", sans-serif]Proper Positioning and Other Tips[/font]
[font="IBM Plex Sans", sans-serif]In addition to paying attention to designations for RPM rating, size, and material, you should also follow these tips when using resinoid-bonded abrasive cutting wheels.[/font] - Use the cutting wheel at a 90-degree angle, perpendicular to the work surface.
- Apply the proper amount of pressure—not too much, not too little—to allow the cutting wheel to do the work. Always avoid pushing too hard on the wheel, which can cause the grinder to stall or kick back or give you a much less efficient cutting action. It also increases the chances that you will slip or lose control of the tool, which can cause damage or injury.
- Choose a grinder with the highest torque or amperage available for the application, as this will help the wheel to do more of the work. For example, instead of using a 4.5-in. wheel on a 6-amp grinder, use a 4.5-in. wheel on a 10-amp grinder. The RPM rating remains the same, but the tool will provide more torque to cut into the metal.
- Choose a tool and consumables that offer quick, consistent cutting, which typically provides the most efficient performance.
- Remember, the thinner the cutting wheel, the more susceptible it can be to side loading, which is a term that describes when the wheel bends while moving side to side in the cut. This can turn dangerous if you lean too hard on a wheel, which can cause the wheel to break or jam in the cut. It can also reduce the efficiency of the wheel and increase the cut time.
- Store the wheel in a clean, dry environment, and avoid placing it in water or mud. This helps minimize environmental effects that could degrade its performance or cause it to crack or wear prematurely. The performance of resinoid bond tends to deteriorate when the wheel is stored for extended periods of time, so be sure to use FIFO (first in, first out) when using wheels.
- Inspect the wheel and consumable before each use to check for signs of damage or wear. Cutting wheels can become harder to control as they wear down. If you can no longer make a safe cut because the wheel’s diameter is worn so thin, then the best course of action is to replace it.
Hole saw basics
Spade bits are the tool of choice for drilling holes up to about 1-1/4 in. in diameter for running electrical wiring and other uses. But when it comes to drilling really big holes for locksets or plumbing pipes, reach for a HSS hole saw. A hole saw is a steel cylinder with saw teeth cut into the top edge. Hole saws don’t cut as quickly as large boring bits driven by a pro’s powerful 1/2-in. drill. But boring bits are expensive ($30 plus drill rental). Hole saws, on the other hand, are readily available at hardware stores and home centers for as little as $5 and work with a standard 3/8-in. drill. Cutting clean holes with hole saws requires a little skill and practice. Here are the key techniques that will make the task safer and give you the best results.
Proper setup is important
Mount the correct-size hole saw in the arbor. If your concrete hole saw has an adjustable center bit, make sure it protrudes past the toothed edge of the saw about 3/8 in. (Photo 2). If the center bit has a flat spot on its shank, align this with the setscrew. Then tighten the setscrew to secure the bit. Finally, tighten the holesaw in the chuck of a corded 3/8
|
|
|
|