Welcome, Guest |
You have to register before you can post on our site.
|
Forum Statistics |
» Members: 466
» Latest member: Charvab
» Forum threads: 1,441
» Forum posts: 2,615
Full Statistics
|
Online Users |
There are currently 17 online users. » 0 Member(s) | 16 Guest(s) Bing
|
Latest Threads |
Bedava Free Fire Hesap
Forum: My Forum
Last Post: Tanitim2025
01-01-2023, 01:02 PM
» Replies: 0
» Views: 0
|
Bedava Pubg Mobile Hesap
Forum: My Forum
Last Post: Tanitim2025
01-01-2023, 12:49 PM
» Replies: 0
» Views: 0
|
Bedava Hesaplar
Forum: My Forum
Last Post: Tanitim2025
10-20-2022, 07:51 AM
» Replies: 0
» Views: 0
|
Film izle
Forum: My Forum
Last Post: Tanitim2025
08-27-2022, 05:16 AM
» Replies: 0
» Views: 0
|
Ehliyet Sınav Soruları
Forum: My Forum
Last Post: Tanitim2025
08-14-2022, 03:13 PM
» Replies: 0
» Views: 0
|
Seo Hizmetleri
Forum: My Forum
Last Post: Tanitim2025
05-22-2022, 02:08 PM
» Replies: 0
» Views: 0
|
شراء عقار في تركيا
Forum: My Forum
Last Post: Tanitim2025
04-30-2022, 11:57 AM
» Replies: 0
» Views: 0
|
Propriété à vendre à Turq...
Forum: My Forum
Last Post: Tanitim2025
04-27-2022, 10:50 AM
» Replies: 0
» Views: 0
|
Apple benefits elma yemen...
Forum: My Forum
Last Post: Tanitim2025
04-16-2022, 10:23 PM
» Replies: 0
» Views: 0
|
CLOUD TÜRKIYE Bulutların ...
Forum: My Forum
Last Post: Tanitim2025
04-13-2022, 04:05 PM
» Replies: 0
» Views: 0
|
|
|
Plating |
Posted by: yida996 - 09-10-2021, 02:11 AM - Forum: My Forum
- No Replies
|
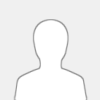 |
There s no such thing as alchemy—magically changing common chemical elements into rare and valuable ones—but water plating is possibly the next best thing. The idea is to use electricity to coat a relatively mundane metal, such as copper, with a thin layer of another, more precious metal, such as gold or silver. Water plating has lots of other uses, besides making cheap metals look expensive. We can use it to make things rust-resistant, for example, to produce a variety of useful alloys like brass and bronze, and even to make plastic look like metal. How does this amazing process work? Let s take a closer look!
Plastic water plating involves passing an electric current through a solution called an electrolyte. This is done by dipping two terminals called electrodes into the electrolyte and connecting them into a circuit with a battery or other power supply. The electrodes and electrolyte are made from carefully chosen elements or compounds. When the electricity flows through the circuit they make, the electrolyte splits up and some of the metal atoms it contains are deposited in a thin layer on top of one of the electrodes—it becomes electroplated. All kinds of metals can be plated in this way, including gold, silver, tin, zinc, copper, cadmium, chromium, nickel, platinum, and lead.
Water plating is very similar to electrolysis (using electricity to split up a chemical solution), which is the reverse of the process by which batteries produce electric currents. All these things are examples of electrochemistry: chemical reactions caused by or producing electricity that give scientifically or industrially useful plastic water plating products.
How does water plating work?
First, you have to choose the right electrodes and electrolyte by figuring out the chemical reaction or reactions you want to happen when the electric current is switched on. The metal atoms that plate your object come from out of the electrolyte, so if you want to copper plate something you need an electrolyte made from a solution of a copper salt, while for gold plating you need a gold-based electrolyte—and so on.
Next, you have to ensure the electronic products shell plastic water plating you want to plate is completely clean. Otherwise, when metal atoms from the electrolyte are deposited onto it, they won t form a good bond and they may simply rub off again. Generally, cleaning is done by dipping the electrode into a strong acid or alkaline solution or by (briefly) connecting the Water plating circuit in reverse. If the electrode is really clean, atoms from the two-color material plating bond to it effectively by joining very strongly onto the outside edges of its crystalline structure.
Now we re ready for the main part of two-color material twice molding water plating. We need two electrodes made from different conducting materials, an electrolyte, and an electricity supply. Generally, one of the electrodes is made from the metal we re trying to plate and the electrolyte is a solution of a salt of the same metal. So, for example, if we re copper plating some brass, we need a copper electrode, a brass electrode, and a solution of a copper-based compound such as copper sulfate solution. Metals such as gold and silver don t easily dissolve so have to be made into solutions using strong and dangerously unpleasant cyanide-based chemicals. The electrode that will be plated is generally made from a cheaper metal or a nonmetal coated with a conducting material such as graphite. Either way, it has to conduct electricity or no electric current will flow and no plating will occur.
How are plastics electroplated?
If you know anything about plastic, you ll spot the obvious problem straightaway: plastic product molding generally don t conduct electricity. In theory, that should completely rule out electroplating; in practice, it simply means we have to give our plastic an extra treatment to make it electrically conducting before we start. There are several different steps involved. First, the plastic surface treatment has to be scrupulously cleaned to remove things like dust, dirt, grease, and surface marks. Next, it s etched with acid and treated with a catalyst (a chemical reaction accelerator) to make sure that a coating will stick to its surface. Then it s dipped in a bath of copper or nickel (copper is more common) to give it a very thin coating of electrically conducting metal (less than a micron, 1μm, or one thousandth of a millimeter thick). Once that s done, it can be electroplated just like a metal. Depending on how much wear and tear the plated part has to withstand, the coating can be anything from about 10–30 microns thick.
|
|
|
New RO modules from Hydranautics |
Posted by: yida996 - 09-10-2021, 02:09 AM - Forum: My Forum
- No Replies
|
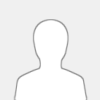 |
We are one of the global leaders in the field of integrated membrane solutions, providing complete membrane solutions for water, wastewater and process treatment and applications, such as reverse osmosis, nanofiltration, ultrafiltration and microfiltration. Our membrane-based solutions are currently used in various applications on seven continents around the world, such as seawater desalination, industrial high-purity water, surface water treatment, wastewater treatment, special process applications, etc.
Residential membranes are manufactured using advanced RO membrane technology. These membranes are available in five variants, 50, 75, 100, 150 and 500 gallons per day (GPD). These membranes can repel salt and other minerals while reducing the flow problems normally associated with membranes.
Hydranautics is a worldwide supplier of separation membrane technology with a comprehensive list of top-performing filtration products for various industries. Applications of Hydranautics RO membrane include boiler feedwater treatment, wastewater treatment, seawater desalination, surface water treatment, drinking water purification, agricultural water treatment, and pharmaceutical water purification.
Hydranautic membrane products are designed with the goal of delivering unmatched quality in terms of product and technical mastery. They are depended upon by several large manufacturing sites throughout the world in countries such as USA, China, Canada, Japan, Mexico, etc.
Proponents of water filters say the water is cleaner and healthier, with impurities removed and minerals added. Replace water filter and alkaline water companies also advertise a laundry list of claims, from improved gastrointestinal health to detoxification and even cancer prevention.
Water filter housings are casings around your filter cartridge that directs the flow of water. In this article, we will take a look at some of the most frequently asked questions about our water filter housings.
They come in a wide range of types. Mainly water filter housings are of two types. However, there can be subcategories based on size, material, and purpose.
RO membrane housings will filter your water right where you use it. For example, an individual tap or faucet. So the systems cover filters under the sink, filters attached to your faucets, or filtration pitchers. The housings for POU water systems serve this purpose
Water filter clear housings, especially whole housing systems, offer a versatile large capacity filtration. Since they are geared towards high flow, they can remove heavy sediments easily. By installing large water filter housings, you can reduce the number of vessels needed for high-flow applications. It can also withstand variations in water pressure. The large cartridge capacity will be very helpful for you.
Reverse Osmosis works by using a high pressure RO pump to increase the pressure on the salt side of the RO and force the water across the semi-permeable RO membrane, leaving almost all (around 95% to 99%) of dissolved salts behind in the reject stream. The amount of pressure required depends on the salt concentration of the feed water. The more concentrated the feed water, the more pressure is required to overcome the osmotic pressure.
|
|
|
Compact Wheel Loader Design Competes with Skid-steer Dominance |
Posted by: yida996 - 09-10-2021, 02:07 AM - Forum: My Forum
- No Replies
|
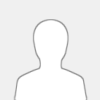 |
Compact wheel loaders generally lag behind skid steer loaders, even though compact wheel loaders are more productive in certain applications. Compact wheel loaders can be a good complement or substitute for skid steer loaders. Benefits include excellent visibility, improved tire wear and fuel economy, driving speed and overall operator comfort. There are also some disadvantages that need to be considered, such as the height of the cab, operating weight and transport capacity. The versatility of the wheel loader is very important.
The definition of a compact wheel loader varies from manufacturer to manufacturer, but machines with less than 125 horsepower usually fall into this category. The real difference between these loaders and their main competitors skid steer and compact track loaders is the higher rated working load capacity, significantly higher travel speeds, superior lift and reach distances, longer wheelbases and more High fuel efficiency.
Due to the characteristics of steering machinery, compact articulated medium wheel loaders work well on hard surfaces because of low tire wear. Compared with similar slip diverters, they also burn less fuel. Between tires and fuel, your end result is reduced daily operating costs.
Visibility on the job site is a safety advantage. From the operator station of the large wheel loader, your field of view is much less than any skid steering system claims. Speed is also an important advantage when working on a site with a large number of ground shots. When comparing compact wheel loaders, there are many configurations and options that can really distinguish performance. Investigate all options before making a choice.
The modern backhoe-loader traces its lineage to a hydraulic digging attachment developed in the late 1940s. Lee Horton and Dave Willens, co-authors of Wain-Roy and the Invention of the Backhoe conducted extensive research into the history of this machine and the associated patents. Look for future designs to provide more car-style functions. With the popularity of backhoe loaders among owners/operators and the platform most similar to the trucks these people travel to and from the site every day, you will continue to see the impact of cars on the cabs and controls of these machines. This includes everything from seat and fabric options to the inclusion of Bluetooth radios and related functions, as well as a constant focus on visibility and site awareness.
Excavators can be divided into many types, such as crawler excavator, wheeled excavator and towed and rail excavator, etc. But they all consist of a boom, dipper, bucket and cab. The crawler excavator is a tracked vehicle that moves upon crawler tracks. In contrast, the wheel excavator is moved upon wheels. They both can be used in many working conditions, such as the digging of the trenches, holes; material handling, forestry work, demolition.
Powered industrial trucks, more commonly known as forklifts trucks, are the worker bees in many manufacturing and warehousing operations. Although primarily used to move materials, they also can be used to raise, lower or remove large objects or a number of smaller objects on pallets or in boxes, crates or other containers. In other words, they do the heavy lifting for us.
Powered industrial trucks can either be ridden by the operator or controlled by a walking operator, and there are many types of powered industrial trucks. Each type presents different operating hazards. For example, a sit-down, counterbalanced high-lift rider truck is more likely than a motorized hand truck to be involved in a falling load accident because the sit-down rider truck can lift a load much higher than a hand truck.
|
|
|
TYPES OF ELASTIC AND WHEN TO USE THEM |
Posted by: yida996 - 09-10-2021, 02:03 AM - Forum: My Forum
- No Replies
|
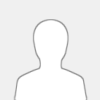 |
Hey y’all, in keeping with this month’s theme of what’s underneath? today we’re going to talk about types of elastic. Being confronted with a wall of elastic or hundreds of online choices can be intimidating for a beginner, so today’s post is meant to demystify those choices.
Types of Elastic
There are three basic types of elastic: braided, woven and knitted. These refer to how the yarns are put together, and the different methods of construction give the resulting elastics different properties.
Braided Elastic
Elastic braided tape has lengthwise, parallel ridges. Those ridges make this elastic have more grip but they also mean that braided elastic tends to narrow as it is stretched. Braided elastic also rolls more easily than woven or knitted elastics, and tends to lose stretch if it is sewn through. For this reason braided elastic rope is typically recommended for use in casings, not for sewing directly to fabric. But in some casings (like waists) braided elastic isn’t the best choice because of its tendency toward rolling. It’s better in sleeves, necklines, or other areas where rolling isn’t a big issue.
Knitted Elastic
Knitted elastic tape is made by knitting the fibers together. Knitted elastic tends to be softer than braided or woven elastic, and it retains its width when stretched. It also works well even when pierced by needles, so it’s a good choice for sew on applications. It rolls more than woven elastic, but less than braided elastic. Since this elastic is softer, it’s suitable for light to midweight fabrics, but doesn’t have the grip needed for heavier fabrics. With knit elastic, I may cut the elastic slightly shorter than the finished measurement in order to have it grip properly, particularly when I use it for waistbands or bra bands.
Woven Elastic
Also referred to as non-roll elastic, woven elastic tape is usually the firmest of the three basic elastic types. It retains width as it is stretched, and is suitable for sew on applications as well as use in casings. Because it tends to be very firm, it is also suitable for heavier weight fabrics. I generally don’t cut woven elastic with much negative ease, because it will pull too much. In other words, if I’m using it in a waistband, I’ll cut the elastic to the body measurement where the waist hits, not any less.
The zipper is such a great invention no dressmaker can ever imagine what life in the sewing room would be like without the zipper. Then of course the famous zipper needs a useful foot to ensure it sews up perfectly. That’s where the zipper foot makes its entrance. If you are going to sew a zipper into your garment don’t attempt this process without a zipper foot. The zipper foot enables the sewing needle to stitch close to the raised edge of the zipper. The gadget itself can be attached to the machine’s presser foot shaft. The zipper foot has the added advantage of being able to attach to the right or the left side of the presser foot holder. Use your zipper foot to insert piping as well as cording.
There are two types of sewing pins. The most commonly used is the straight pin, also know as the hemming pin or basting pin. The key facets of straight pins that differ and can help you choose the type you need are length, thickness, and type of head and tip. The metal or finish of the straight pin is typically brass, steel, nickel, or a combination thereof. The metal used with sewing pins determines whether the pins will stick to a magnet - a plus for making sure there are none on the floor. Nickel plating is useful for steel pins as it helps the pin stick to a magnet and prevents it from rusting.
A crochet hook is the basic tool you'll need to get started on your journey as you learn to crochet. Made from metal, plastic or wood with a small hook at one end, crochet hooks are used to turn a lovely skein of yarn into cosy jumpers, snuggly blankets and beautiful home accessories. All crochet hooks have similar basic features, in the same way knitting needles do, but different brands may modify them slightly for extra comfort or a more eye-catching design.
|
|
|
What is Grinding? |
Posted by: dwpyyy1 - 09-09-2021, 05:30 AM - Forum: My Forum
- No Replies
|
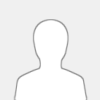 |
Grinding takes an abrasive — often attached to a grinding wheel — and uses its many grains to cut a workpiece. Variations on this process are useful for a wide variety of applications.
These interactions feed into three major commercial grinding processes: rough grinding, precision grinding and ultra-precision grinding. Rough grinding maximizes the metal removed at the cost of surface finish. It primarily sees use in cutting off billets, grinding weld beads smooth and snagging gates and risers from castings. Additional surface finishing passes typically take place afterward — in particular, a “spark-out” pass relieves some of the stress on the machine tool and uses plowing to impart a better surface finish and size tolerance. Precision grinding is a middle-ground between metal removal and part size control, and serves as the basis for creep feed grinding, slot grinding and high-efficiency deep grinding. In ultra-precision grinding, little to no actual cutting occurs, but sliding action from very fine grains rubs the workpiece surface to a high finish. Most surface finishing processes, such as lapping and polishing, are examples of this type of grinding.
Although speeds for grinding wheels and cutting wheels are measured in sfm or smm, wheels are often rated in rpm. It is important never to operate a grinding wheel over its rpm limit — most experts recommend never mounting a wheel on a machine that can exceed the wheel’s limit.
As speeds increase, each grain cuts and wears less. This emulates a harder grade. Vitrified bonds work up to 6,500 sfm, with organic bonds handling up to around 9,500 sfm. Higher speeds will require specially made grains.
Work speed defines the speed at which a grinding wheel passes over a workpiece or rotates around a center. High work speeds lower the heat retention and reduce the risk of thermal damage. Both high work speeds and reducing the diameter of the wheel result in increased grain depth of cut, performing like a softer grade wheel.
Surface grinding, such as stainless steel grinding, involves grinding a plane surface by feeding the workpiece beneath a rotating grinding wheel. Like cylindrical grinding, it operates in two general formats. The workpiece may travel traversely under the wheel and move back and forth beneath a grinding wheel mounted on a horizontal spindle, or it may move in circles on a rotary table beneath a vertical spindle that cuts on the face of the grinding wheel or grinding segment. Applications for this grinding type may grind a surface flat or introduce grooves by grinding straight channels into the workpiece. While milling can complete these tasks, grinding improves surface finish, has less expensive tooling and allows contours to be dressed into the profile of the wheel — making it much more cost-effective for very hard or abrasive surfaces.
Centerless grinding creates cylindrical forms at extremely close tolerances. This type of grinding eliminates the need for center holding by supporting the workpiece at three separate points: the grinding wheel, feed wheel and work support blade. Nothing actually clamps the workpiece in place, so each piece flows freely for continuous production (also known as “throughfeed centerless grinding”). The grinding wheel, during ordinary metal grinding, and the feed wheel rotate in the same direction, while the workpiece rotates in the opposite direction between them. The rotation keeps the workpiece down, while the work support blade (slightly angled to raise the workpiece above the centerline for better cylindricity) holds it up. The work support blade should always be at least as long as the grinding wheel is wide. Centerless grinding also comes in three forms. Throughfeed centerless grinding is used on straight cylindrical workpieces without interfering shoulder or projections, and involves the offset axis feed wheel feed the workpiece past the grinding wheel to a discharge position. Infeed grinding (also called plunge centerless grinding) is best when a workpiece has projections, irregular shapes, varying diameters or shoulders, and works best for profiles and multi-diameter workpieces. In this submethod, feed wheels above the grinding wheel feed the workpiece downward, with no lateral movement during grinding. Endfeed centerless grinding grinds conically tapered cylindrical sections like shanks on A and B taper drill bits. Here, the feed wheel, grinding wheel and work blade are set up in a fixed relationship to each other, then two wheels are dressed to a shape matching the end taper of the workpiece and the workpiece is fed from the front of the grinding machine until it reaches an end stop.
Creep feed grinding is a slow, one-pass operation that makes a deep cut of up to one inch in steel materials at low table speeds between 0.5 and 1 ipm. It is not suitable for conventional grinding machines, but for those which are compatible with it, it offers high productivity and cost effectiveness. Creep feed grinding is a plunge operation with high horsepower requirements, and which also requires a heavy flow of cutting fluid close to the nip to remove chips and cool the work. Continuous dressing at about 20 to 60 millionths per revolution — preferably with a diamond roll — reduces cutting times of fixed machine cutting and keeps the wheel sharp. When a second pass is required, it is typically of no more than 0.002 inch deep to “clean up” the workpiece.
|
|
|
Key Door Hardware Components for Safety and Security |
Posted by: dwpyyy1 - 09-09-2021, 05:20 AM - Forum: My Forum
- No Replies
|
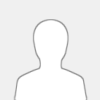 |
Understanding door hardware options and opportunities is the first step in turning threats and weaknesses into strengths. Entry doors with window mesh might be in bad condition, with broken closers, loose hinges, doors that sag or are sticking, latches that do not align properly with the strike, and wide gaps between the door and frame that pry open easily. Other access points might use old technology.
Poorly maintained hardware offers the easiest path for unauthorized entry. Old technology is next and soon might become a weakness. Vendors know the best options for meeting ASTM/BHMA standards for the manufacture and testing commercial grade hardware. ANSI Grade 1 hardware is specifically designed for high-traffic areas because it can withstand the highest number of life cycles and is much harder for an active shooter to break through.
Upgrades that deliver greater safety and security include replacing Grade 2 and 3 components with Grade 1 hardware. A further upgrade involves integrating the latest generation of commercial electronic UPVC door locksets, closers, hinge hardware and alarms with a central control system.
Managers need to pay special attention to levels of access to facilities. Authorized personnel need access and, in emergency situations, rapid and safe egress, while unauthorized personnel have to be kept out. Firefighters and other emergency personnel need ease of entry to locate and evacuate people rapidly.
Increasingly, managers are installing card and PIN UPVC door lock systems, and they are rearranging traffic flows to channel visitor traffic at elevator lobbies toward properly staffed, secure reception areas. Only authorized personnel should be able to enter the main building through locked lobby doors.
Among the most common door hardware components upgraded for improved security are the following:
Closers.
Standard and custom door closers include surface-mounted and hidden, heavy-duty closers for high-cycle or windy and drafty conditions, as well as ADA-compliant maximum-force-to-operate closers. A closer’s open cycle compresses the spring and positions the fluid through the open valve for closing. The delay valve allows slower-moving traffic to pass. The closing valve slows closing speed to within 6 inches of the stop. The latching valve accelerates closing for the last 6 inches. Closers need regular adjustment to keep the cycles operating as designed.
Hinges. (UPVC door window hinges)
By removing the hinge pins, an attacker can gain access to a facility through a hinged door with window hinge, even when it is locked. Removing a screw and inserting a special pin prevents an attacker from removing the door from its frame, even if door hinge pins are removed.
Locksets.
Deadbolts, knobs, lock cylinders, levers, and entry handsets are wired and wireless devices that operate via remote-open and turn-on devices and cell phone applications. Replacing mechanical keyed locksets with electro-mechanical locks in the same housing is a low-cost upgrade option. Managers are using electronic remote-controlled devices, such as door roller, cameras, motion sensors, and tamper alarms, to give early warning.
They also can upgrade unguarded remote entry points from mechanical locks and keys to systems that incorporate CCTV and sound. A security guard at a remote point directs the person seeking entry to place his or her badge in front of the camera, verifies the person has the proper clearance and is the same person as shown on the picture badge, and remotely actuates the lock allowing entry.
In an emergency requiring rapid evacuation of the building, all evacuation route doors with window roller are remotely unlocked immediately and simultaneously from a central control. Other common upgrades include the installation of biometric fingerprint readers, facial-recognition systems, and floor-to-ceiling locked turnstiles.
Alarms. Radio-wave tamper alarms can be activated by a vehicle or a person moving through and disturbing a radio wave field. The power source sends radio waves through the antenna surrounding anything the antenna touches , including a door, window door hand tools, fence, vehicle, or unattended building. Audio alarms can be attached or silent-connected to a police station or can activate CCTV or access -control systems.
|
|
|
Importance of Using Paper Bags |
Posted by: dwpyyy1 - 09-09-2021, 05:14 AM - Forum: My Forum
- No Replies
|
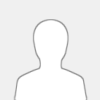 |
Carrybags has become a more convenient way to carry daily necessities and for packaging in small quantities. The well-known form of such bags is in the form of plastic bags. Despite of all known hazards of plastic pollution, it’s prevalent and pervasive in India. Plastic bags are one of the worst and most unnecessary plastic polluters of the earth. Plastic bags are used on a large scale by retailers for a simple reason that plastic bags are much cheaper than paper, cloth or other eco-friendly bags. This paper presents the designing and development of asystem to automate the procedure of paper bags production so as to make its production cost comparable to plastic bags and inherently increase its production rate so as to fulfill the ever increasing demand. We have used micro-controller based design approach which has kept the cost of the system significantly low as compared to PLC based designs and have automated the manufacturing process.
We need small size bags every day for various purposes like grocery, fruits, and vegetables. We use plastic bags for such purposes. Plastic shopping bags have a surprisingly significant environmental impact for something so seemingly innocuous. Plastic shopping bags kill large numbers of wildlife each year. One of the most dramatic impacts is on marine life.So to avoid above harmful effects of Plastic Bags, viable alternative is required which is Paper Bag. Actually, Paper Bag is being used but in very small scale. Conventional Paper Bags requirespecial paper which increases the overall cost of the Paper Bag. This is the main cause due to which use of Paper Bag is less. Also initial investment cost is very much in conventional paper bag making machine. So it cannot be used for small scale production.All these problems are eliminated in the presented machine. Amachine whose initial cost is less, which does not require any special paper, which can be used for small scale production, is developed. Thismachine willhelp a poor family to earn money through small scale production of paper bags.
Paper bags have been gaining popularity since then plastic bags have been banned in various countries and cities. The product is made in two ways; traditionally, i.e. manual which is a manual or technical means i.e. with the help of automated equipment. The second method is much larger. In other words, it requires less workers and more money to buy land and equipment. Based on the core business of nonwoven bag making machine Manufacturers, the machine has 2 different output capabilities with good finish and seamless quality.
Amazing Benefits of Using a Paper Bag Production Machine: -
Excellent Quality: The great advantage of producing a paper bag from an automated machine is the excellent quality one can achieve throughout the production process. When we make paper bags in traditional ways, the quality of the product does not always match the whole production process. It is difficult to maintain the same level of quality per unit. Machine paper bags offer the same quality and precision each time.
Save on Work Expenditure: The introduction of an automated production process machine including slitting machine has reduced the need for workers in the paper industry. One only needs to change the paper roll and collect the finished product after the production process is completed. This saves unnecessary costs on jobs and you can invest in machinery and land instead of workers. Too much machinery and land can lead to a double standard of business production at the same time.
Paper bags are gaining importance as these bags are 100% reusable, recyclable and biodegradable and at the same time environment friendly and pose less threat to wildlife. it requires less energy for paper bags to be recycled than plastic bags. Paper bags have come a long way since their beginnings in the mid-eighteenth century when some paper bag manufacturers started developing paper bags that are more hardy and long lasting. The paper bags are generally box-shaped in design that allows them to stand upright and hold more goods. Corporates are using paper bags for promotions, seminars, product packaging and branding purposes.
10. When your product is properly packaged with premium quality paper bags, you can attract more customers which will help in promoting your brand to the targetaudience.
So, if you are ecofriendly and at the same time want to be ahead of your competitors, start using paper bags.
|
|
|
The chemistry of cosmetics |
Posted by: dwpyyy1 - 09-09-2021, 05:08 AM - Forum: My Forum
- No Replies
|
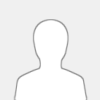 |
Cosmetics materials are not a modern invention. Humans have used various substances to alter their appearance or accentuate their features for at least 10,000 years, and possibly a lot longer.
Women in Ancient Egypt used kohl, a substance containing powdered galena (lead sulphide—PbS) to darken their eyelids, and Cleopatra is said to have bathed in milk to whiten and soften her skin. By 3000 B.C men and women in China had begun to stain their fingernails with colours according to their social class, while Greek women used poisonous lead carbonate (PbCO3) to achieve a pale complexion. Clays were ground into pastes for cosmetic use in traditional African societies and indigenous Australians still use a wide range of crushed rocks and minerals to create body paint for ceremonies and initiations.
Cosmetic products that make an additional therapeutic claim (such as moisturisers that also lighten the skin) are regulated by a different organisation—the Therapeutic Goods Administration (TGA).
But what exactly are we putting on our skin? What do those long names on the ingredient list mean and what do they do? While the formula of each product differs slightly, most cosmetics contain a combination of at least some of the following core ingredients: water, emulsifier, preservative, thickener, emollient, colour, flavors and fragrances and pH stabilisers.
Water
If your product comes in a bottle, chances are the first ingredient on the list is going to be water. That’s right, good old H2O. Water forms the basis of almost every type of cosmetic product, including creams, lotions, makeup, deodorants, shampoos and conditioners. Water plays an important part in the process, often acting as a solvent to dissolve other ingredients and forming emulsions for consistency.
Water used in the formulation of cosmetic materials is not your everyday, regular tap water. It must be ‘ultra-pure’—that is, free from microbes, toxins and other pollutants. For this reason your label may refer to it as distilled water, purified water or just aqua.
Emulsifiers
The term emulsifiers refers to any ingredient that helps to keep unlike substances (such as oil and water) from separating. Many cosmetic products are based on emulsions—small droplets of oil dispersed in water or small droplets of water dispersed in oil. Since oil and water don't mix no matter how much you shake, blend or stir, emulsifiers are added to change the surface tension with surfactant materials between the water and the oil, producing a homogeneous and well-mixed product with an even texture. Examples of emulsifiers used in cosmetics include polysorbates, laureth-4, and potassium cetyl sulfate.
Preservatives
Preservatives are important ingredients. They are added to cosmetics to extend their shelf life and prevent the growth of microorganisms such as bacteria and fungi, which can spoil the product and possibly harm the user. Since most microbes live in water, the preservatives used need to be water-soluble, and this helps to determine which ones are used. Preservatives used in cosmetics can be natural or synthetic (man-made), and perform differently depending on the formulation of the product. Some will require low levels of around 0.01%, while other will require levels as high as 5%.
Some of the more popular preservatives include parabens, benzyl alcohol, salicylic kojic acid, formaldehyde and tetrasodium EDTA (ethylenediaminetetra-acetic acid).Lipid thickeners are usually solid at room temperature but can be liquefied and added to cosmetic emulsions. They work by imparting their natural thickness to the formula. Examples include cetyl alcohol, stearic acid and carnauba wax.
Emollients soften the skin by preventing water loss. They are used in a wide range of lipsticks, lotions and cosmetics. A number of different natural and synthetic chemicals work as emollients, including beeswax, olive oil, coconut oil and lanolin, as well as petrolatum (petroleum jelly), mineral oil, almond oil, glycerine, zinc oxide, butyl stearate and diglycol laurate.
Colouring agents/pigments
The inorganic metal oxide pigments are usually duller than the organic intermediate pigments, but are more resistant to heat and light, providing a longer-lasting colour.
Glimmer and shine
|
|
|
Here's the Truth About Wood Veneers |
Posted by: dwpyyy1 - 09-09-2021, 04:54 AM - Forum: My Forum
- No Replies
|
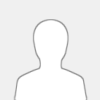 |
When you learn that a piece of furniture has a veneer, does it make you cringe a little? Admittedly us, too. But wood veneers, in fact, are a traditional and structurally significant aspect of furniture-making that still come into play in contemporary design. Wood veneers have been used in furniture-making and millwork techniques for over 200 years, says interior designer Cate Caruso, of Studio C, who uses them for all kinds of high-quality custom furnishings. In woodworking, a veneer is actually a paper thin cut of wood that's applied to both sides of a strong core surface, like furniture-grade MDF or substrate material, to seal and stabilize it—which is critically important when you're fashioning built-in furniture or anything with a mechanism. The reason is simple: Solid wood expands and contracts as the temperature changes, and your apartment isn't temperature controlled no matter how powerful your A.C. unit is. A dining table, for instance, can be made from solid wood (and many are), but a wood piece with moving parts cannot. With kitchen cabinetry, drawers, and anything built-in or paneled, you really have to have veneers, Caruso explains. A solid piece of wood just isn’t always structurally sound enough to fabricate a millwork.
What she is not using is fake wood. Oftentimes, when people see a veneered furnishing that’s cheap, it’s actually not wood at all—it’s a laminate material, Caruso explains, putting a name to the faux surface that gave all veneers a bad rap somewhere along the line. (Those are made from plastic, paper, or even foil that's been printed with a wood grain pattern that often wears away at the edges—a sure way to spot them.) But of course, there's also a range in quality of proper veneers depending on who makes them. All woodworking can be done well or it can be done poorly—but an expert millworker will make veneers look seamless, with perfect corners, Caruso says, which explains the misconception that a wood engineered veneer is cheap when it’s anything but.
Besides keeping a wood panel stable, veneers have other perks and purposes. They're considered an environmentally conscious option because you're maximizing that log in thin little sheets, Caruso says, and then the core is furniture grade MDF or substrate material. In extreme cases, they can even be cost-saving. Think about Brazilian rosewood, which is rare, endangered, very hard to get, and very expensive, says Patrick Muecke, Caruso's general contractor, who was a millworker for 15+ years before opening his own GC and management company. If you want to do a rosewood paneled room in solid wood, you’d have to be the Sultan of Brunei in order to afford it. The same would go for any project in an expensive wood; veneers would bring down the cost. Beyond millwork, natural bamboo veneers are also required for certain special techniques: Book-matched wood doors (or book-matched wood anything) would have to be fashioned using bamboo veneers because you'd never find wood planks with grains that perfectly match—it's necessary instead to have a series of veneers cut from the same log. Then there are labor-intensive inlay arts like marquetry and parquetry, which require veneers cut to certain sizes and shapes that are then fit into the top of a structure. A far cry from laminate surfaces, right?
What kind of wood edge banding do you want?
For many people who are new to buying residence hall furniture, that’s going to elicit some questioning faces.
What’s edge banding? Good question.
Wood Veneer
3. Wood Veneer, including reconstituted veneer is another common edge banding material. It’s made from thin slices of wood—typically oak, maple, ash, walnut, birch, and mahogany—that are joined together in a roll using finger jointing. It usually features a heat-sensitive glue backing.
Pros: It’s attractive, durable, and strong. It provides a clean solid-wood look, and it’s pre-sanded to easily absorb stains and finishes to seamlessly match your wood. Cons: It’s not heat resistant. Avoid putting it near a heater. It doesn’t do well in high-use environments.
|
|
|
UNDERSTANDING AUDIO AND VIDEO WIRE AND CABLE |
Posted by: dwpyyy1 - 09-09-2021, 04:45 AM - Forum: My Forum
- No Replies
|
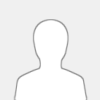 |
An Electrical conductor is an element (remember the periodic table in chemistry?) which conducts electricity, as opposed to an insulator, which does not, or a semiconductor which allows some electricity to pass. There are also alloys that have different electrical characteristics, and platings or other element to element contacts such as in connectors which also have electrical characteristics as well as chemical characteristics in their applications. Simply stated - it is not just a matter of connect metal to metal and you have a good connection. The best connectivity designs take into account the source connector materials, the receiving device connector materials, the audio video wire connector materials, the conductor materials and the electrical and chemical ways in which they interact with one another.
MEET THE CONDUCTORS - SILVER, COPPER, GOLD, TIN, NICKEL, STEEL
1. Silver is the best conductor, with a very slight edge over copper. Silver also has the benefit of having oxidation that conducts as well as unoxidized silver.
2. Copper is the next best conductor, with about 1.05 times the resistance of silver, and due to its lower cost is the most commonly used conductor for audio and video cables. Unfortunately copper oxidation is a semi conductor and should be avoided because of the "skin effect" which causes high frequencies to use the outside of the conductor at high frequencies. If the outside of the conductor is oxidized, the performance at very high frequencies will suffer. Note: This is does not have any significant effect in the audio frequency range. (For more on Skin effect see the Article Library at Audioholics)
Discreet wiring - Discreet wiring is where separate conductors, indluding speaker wires, are run in some fashion (wires or circuit board traces) to the circuit components or input/output connections to which they need to go to. In some circuits, especially non signal related connections the path or interaction of these types of wires to one another is not particularly important as long as they are separated from one another to a reasonable extent. The closer they get, the more likely they are to possibly interact. This all goes out the window when a signal or "change" (whether they are due to ac power wire, analog signals or digital signals - basically any type of current or voltage change) becomes a part of the mix.
Example: Two wires are close together while another two wires are farther apart. The closer wires act more like a capacitor (have more capacitance) than the second two wires. If the circuit is in a quiescent state - "at rest" (no changes are going on) , there is potential energy storage due to capacitance, but without change, it has no effect on any signal, since there is no change. If you then create a change, or signal wire that causes electrical current flow, the two sets of wires may then have an effect on those changes, due to capacitance, inductance, etc, and the changes created may be different depending on the frequency of the signal involved and the characteristics of the wires and the overall circuit.
*Note - Steel Coat Hangers as Cable
While the typical crazies on forums suggest that coat hangers will operate just fine as an audio cable (and poorly designed tests concur) there are definitive reasons why it is not a remotely good choice. First of all, Steel is a very poor conductor with over 7 times the resistance of copper wire. That means lots of wasted power supply wire. Second, steel oxidizes easily and the oxidization is a poor conductor. Third, steel is rather hard to make into a twisted pair, allowing for EMI and RFI resistance. Without making the steel into a twisted pair, Noise and Hum may become a larger than desired portion of the sound!
|
|
|
|