Welcome, Guest |
You have to register before you can post on our site.
|
Forum Statistics |
» Members: 466
» Latest member: Charvab
» Forum threads: 1,441
» Forum posts: 2,615
Full Statistics
|
Online Users |
There are currently 18 online users. » 0 Member(s) | 17 Guest(s) Bing
|
Latest Threads |
Bedava Free Fire Hesap
Forum: My Forum
Last Post: Tanitim2025
01-01-2023, 01:02 PM
» Replies: 0
» Views: 0
|
Bedava Pubg Mobile Hesap
Forum: My Forum
Last Post: Tanitim2025
01-01-2023, 12:49 PM
» Replies: 0
» Views: 0
|
Bedava Hesaplar
Forum: My Forum
Last Post: Tanitim2025
10-20-2022, 07:51 AM
» Replies: 0
» Views: 0
|
Film izle
Forum: My Forum
Last Post: Tanitim2025
08-27-2022, 05:16 AM
» Replies: 0
» Views: 0
|
Ehliyet Sınav Soruları
Forum: My Forum
Last Post: Tanitim2025
08-14-2022, 03:13 PM
» Replies: 0
» Views: 0
|
Seo Hizmetleri
Forum: My Forum
Last Post: Tanitim2025
05-22-2022, 02:08 PM
» Replies: 0
» Views: 0
|
شراء عقار في تركيا
Forum: My Forum
Last Post: Tanitim2025
04-30-2022, 11:57 AM
» Replies: 0
» Views: 0
|
Propriété à vendre à Turq...
Forum: My Forum
Last Post: Tanitim2025
04-27-2022, 10:50 AM
» Replies: 0
» Views: 0
|
Apple benefits elma yemen...
Forum: My Forum
Last Post: Tanitim2025
04-16-2022, 10:23 PM
» Replies: 0
» Views: 0
|
CLOUD TÜRKIYE Bulutların ...
Forum: My Forum
Last Post: Tanitim2025
04-13-2022, 04:05 PM
» Replies: 0
» Views: 0
|
|
|
Chandelier Buyer's Guide |
Posted by: ye28ye - 10-11-2021, 05:35 AM - Forum: My Forum
- No Replies
|
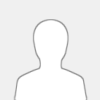 |
Chandeliers add elegance to any space, and the look is more versatile - and affordable - than you might think.
When you think of chandeliers, you might picture cartoonish dollar signs — they’re often associated with the wealthy– but, in fact, you can find a wide range of affordable chandeliers on the market. Chandeliers come in all types of styles, sizes, and price points, compared to industrial chandelier. Just about any consumer that’s considering a new light fixture for their home can find one that’s within their price range and matches the style of their space. All you have to do is look.
If you like the idea of adding some classy style to your home with a new chandelier, we can help. This buyer’s guide will take you through the main types of chandeliers available and factors you should consider in your search.
Types of Chandeliers
Chandeliers are far from basic in style. Some are fancy, like those you may picture accentuating a palace ballroom. Some are more modern and offer a simpler style. Others provide an old-fashioned look with candelabras updated for the modern era to be electric. In other words, when it comes to buying a chandelier, you’ve got plenty of options. Here are six of the most common types of chandeliers you will be choosing from.
Chandelier with Shades
If you’ve been looking at other types of lighting fixtures, then you’ll know that “lights that come with shades” is a common category, regardless of the type of fixture you're looking at. Chandeliers are no different.
Shaded chandeliers are available in a wide array of colors and styles, but in all cases, they do the double duty of adding a visual element to the chandelier while also somewhat dimming how much light it puts out. If you want softer lighting from your chandelier, or simply like the look of a chandelier with shades, then this is a category worth considering.
Tiered Chandeliers
If your ceiling as are high enough to safely install one, a tiered luxury chandelier can add a majestic look to your space. Like it sounds, a tiered chandelier will have multiple levels of lights. Perhaps the most common, are chandeliers that have two tiers of lights. However, it’s not hard to find a chandelier that offers three, four, or five tiers of lights.
Candelabra Chandeliers
Many of the modern chandeliers of the past held candles. Candelabra, or candle style chandeliers, borrow this idea to keep a classic, old-fashioned look, while updating the technology behind it to add safety and convenience. You can get the historical look of a candle-filled chandelier by simply flipping a switch (and without burning your house down).
Crystal Chandeliers
When you picture fancy, sparkling chandeliers from movies or the homes of the wealthy, the crystal chandelier is likely what comes to mind. Many crystal chandeliers will be costly, as you’d expect, but you can actually find plenty that fall in a reasonable price range for customers looking on the lower end of the chandelier price spectrum.
Drum Chandeliers
Drum chandeliers have a shade around the light or lights in the shape of a drum. This technically makes them a subset of the chandeliers with shades category, but they’re popular enough on their own to mention separately. The shades you’ll see on drum chandeliers can come in a number of different materials and often offer some extra design to the overall effect of the chandelier.
Mini Chandeliers
Chandeliers are often thought of as something grand, which in our imaginations usually also means large. If you want the elegance of a chandelier in one of the smaller spaces in your home though, you can find plenty of options in the mini-chandelier category. Mini chandeliers are available in a wide array of style types and at many different price points, so don’t let size stop you from going after the light fixture of your choice.
What is a downlight?
The downlight definition can vary depending on whom you ask, but generally speaking, downlighting refers to any light that is mounted in a high place and aimed downward at a surface, object, or general area, like a spotlight. The term is often used interchangeably with “recessed lights”, which are downlights that have been mounted within an opening in the ceiling.
Recessed downlights,also known as can lights or pot lights, are an excellent choice for many residential and commercial applications. These versatile lights give a clean, modern and attractive look to their surroundings and will work in practically any room. Homeowners and business owners can use them in a variety of ways for general lighting or to highlight specific parts of a room.
What are the common uses of recessed downlights?
They can provide ambient or general light to give broad, even light to an entire room. Alternatively, they can provide accent lighting, highlighting a painting, sculpture or other object that warrants attention. Recessed downlights can be used as task lighting over work desks, providing concentrated light on a project. Finally, these lights can be used for wall-washing to make a room look bigger and more attractive.
Recessed downlights typically require three primary components for installation. Even so, they’re not particularly difficult to install.
Components
The first thing you’ll need is a housing to contain the light. The housing is hidden above the ceiling and encloses all the parts of the downlight fixture. Sometimes the housing is purchased separately and sometimes it is integrated into the full fixture. When choosing recessed lighting, an important consideration of the housing is whether or not you need it to be insulated or air tight (AT). Insulated (IC-rated) housings mean that the downlight is allowed to be in direct contact with the insulation that is above the ceiling. This is important if you need to maintain a continuous thermal break or need continuous insulation coverage between two floors of a building. Downlight housings that are AT prevent the conditioned air leakage below the ceiling from seeping into the unconditioned plenum space above. This air sealing will save on heating and cooling costs.
In addition to the housing, recessed lights also require trim. The trim is the finished portion of the downlight that you see below the ceiling. It comes in many different styles that can manipulate the light in different ways as well as provide different desirable aesthetics. Reflector (also called multiplier) trims provide the most light by reflecting the light from the light source, which increase its brightness and effect. Baffle trims are useful in providing a matte, diffused light output that reduces glare. Adjustable (also called eyeball) trims allows you to swivel and direct the light at a particular object. Shower lens trim is waterproof, which makes it perfect not just for showers and bathrooms, but for any place where water might be an issue — including outdoor installations. Wall wash trim masks off a portion of the downlight’s aperture to direct it in one direction only.
Finally, you must select a light source to provide the actual illumination in your recessed lighting. The types of bulbs you can use in recessed lighting include halogen, fluorescent, incandescent, and LED. Each of these bulbs has its pros and cons. The housing usually includes instructions from the manufacturer on suggested bulb types, which makes your choice easier. In addition, most LED surface mounted downlight trims contain an integrated LED module and have no need for separate bulbs. The experienced staff at Take Three Lighting is always ready to help you with your choice of bulbs, trim and housing or with any questions you may have.
Also, LED Street lights are becoming more the norm than the exception due to lower prices, better technology and more demand for energy efficiency. With savings of our 70% compared to HIDs, Metal Halide and High Pressure sodium, the energy savings is pushing LED street lights into the very mainstream. The MH and HPS have been the dominant light sources for the last 30 years, but Light Emitting Diodes are taking over faster than ever.
|
|
|
Every Question You've Ever Had About Lash Extensions, Answered |
Posted by: ye28ye - 10-11-2021, 05:33 AM - Forum: My Forum
- No Replies
|
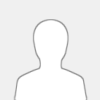 |
The beauty industry has seen it all when it comes to lashes—magnifying mascaras, “miracle” growth serums, heated curlers—you name it. But no trend is quite as polarizing as eyelash extensions. When extensions first hit the mainstream market, it seemed like a relatively painless way to achieve wispy, fluttering lashes without the inconvenience of falsies or mascara. But as with any new beauty service, lash extensions quickly revealed their drawbacks. For starters, some states haven’t placed regulations on the service, consequently leading to cases of irritation, infection, and damaged natural lashes due to poor hygiene and technique.1 The process is also fairly expensive, setting you back hundreds of dollars and hours of your personal time.
But is it worth it to wake up with a flawless set of semi-permanent lashes every day?
What Are Lash Extensions?
Eyelash extensions are semi-permanent fibers that are attached to your natural eyelashes in order to make your lash fringe look longer, fuller, and darker. Individual lash extensions are applied to each of your individual natural eyelashes (one extension per natural eyelash) using a semi-permanent glue. The material varies from studio to studio, but lash extensions can be made of synthetic, mink, faux mink eyelashes, or silk fibers. Most studios offer a variety of extension lengths, curl patterns, and tints so clients can customize their look.
Types of Eyelash Extensions
Lash artists use three different kinds of eyelash extension materials: mink, silk, and synthetic. Some studios also carry "faux mink eyelashes" extensions, which are technically just synthetic extensions that mimic mink extensions. Most lash studios have their preference for the type of lash extension they use and won't always ask you if you have a preference. So if you're vegan or allergic to cats, be sure to specifically request that mink eyelash extensions are not used on you. No lash extension type lasts longer than the other, but mink and silk flat eyelashes tend to have a more natural look, while synthetic lashes can be thicker and darker, which is better suited for those who want a bolder look.
Within these three categories (mink, silk, and 3D synthetic eyelashes), there are varying degrees of length and curl to choose from. Typically your lash artist will use multiple lengths and curl strengths to create a wide-eyed effect, with longer lashes being placed towards the outer corners of the eyes and shorter lashes placed on the inner corners.
What’s the Application Process Like?
“[Lash extensions] are carefully applied one at a time (typically 80-140 per eye) using a specially-formulated, semi-permanent glue that will not irritate or damage the natural lash,” says Richardson. “The lash is only applied to an existing lash, not to the skin.” While the exact process varies from salon to salon, here’s what you can expect:
Evaluation: “Prior to application, the technician should go through all the risks and benefits of having eyelash extensions before applying them, and also ask about any conditions you may have that would make eyelash extensions unsuitable for you,” says Richardson. They'll also ask you to remove your contacts if you wear them.
Decide on Extension Length and Curl Strength: Your lash artist should start the process by asking you what kind of look you’re going for, whether that be more glamorous or more natural. Based on your desired look, you’ll choose an ideal length and curl strength for the extensions. Keep in mind that your artist may decide to use up to 3-4 different extension lengths, concentrating longer extensions on the outer corners and shorter extensions on the inner eyes.
Cleansing the Eye Area: Your lash artist will have you lie down and ensure that you are in a comfortable position. Then, they will cleanse the area to remove any makeup, oil, and germs from the area. It’s helpful to your artist if you arrive makeup-free to your appointment.
Applying the Tape and Eye Gels: Your eyes are closed for the duration of the process, which typically takes 1-2 hours, depending on the number of extensions your lash artist is applying. To prep for the actual application, you lash artist will apply an under-eye gel to your lower lash line to keep your lower lashes out of the way and provide a contrasted background to work against (it’s easier to see your lashes against a crisp white background). Then, the eye gels will be secured with medical-grade tape on both sides of the eye (this tape doesn’t touch your lashes, and it doesn’t hurt once it’s removed later).
Application: Using tweezers, your lash artist will dip the end of each extension in the lash glue and then apply it to your individual circular eyelashes. In most cases, one eyelash extension is applied per natural lash, however, more voluminous looks can require multiple extensions per individual natural lash. The application isn’t painful, although you may feel anxious having tweezers operate so close to your eyes while they’re closed.
Drying: The lash glue dries very quickly, but your lash artist will likely have you sit for around 10 minutes once all of the extensions have been applied. Some lash artists like to point a small, handheld fan at your extensions to speed up the drying time, while others prefer to let the glue air dry. During this stage, your eyes are still closed.
Removing the Tape and Gels: Once your lashes are completely dry, your lash artist will remove the under-eye gels and tape (this doesn’t hurt at all, but let your lash professional know if you tend to experience sensitivity in this area so they can practice extra caution). Once removed, your lash artist will likely brush through the lashes with a spooly, then you’ll be asked to slowly blink your eyes open. Et voila!
Where Should You Go For Eyelash Extensions?
One of the scariest things about eyelash extensions is that the process isn’t regulated in some states, as is the case in Alabama, Maryland, Connecticut, Delaware, Idaho, and Wisconsin. A shocking number of states only require a cosmetology license in order to perform the service, and while these professionals are extremely skilled in their respective areas of focus (hair coloring, hair styling, hair cutting, makeup, and nails), they aren’t trained specifically to work on the eye area, which is extremely sensitive and delicate.
When booking your lash extension service, make sure your lash artist is a licensed esthetician (rather than a cosmetologist).1 Estheticians are specifically trained in skin-oriented treatments, like facials, microdermabrasion, chemical peels, and—you guessed it—eyelash services. Ideally, visiting a licensed esthetician at a studio that focuses on lash services (like Envious Lashes in New York City) is your safest bet.
The Benefits
It Works: With lash extensions, you’ll wake up every day with long, fluttering, gorgeous lashes.The process is extremely effective at enhancing your eyes, and looks incredible on everyone.
Completely Customizable: Your look can be as natural or as dramatic as you’d like, just work with your lash artist to decide on the ideal length and curl of your extensions.
Virtually Waterproof: While you can’t get them wet in the first 48 hours, you can still swim, shower, and sweat in your extensions (although the dryer you keep them, the longer they can last).
Pain-Free: The entire process is 100 percent painless for almost everyone, from start to finish.
It’s (Usually) Safe: Dermatologists, plastic surgeons, and estheticians agree that, for the most part, extensions are safe (although there are risks of irritation and infection...more on that below).
The Drawbacks
Irritation and Infection Risks: “The major risk of eyelash extensions is irritation of the eyes. Eyelash extensions typically require a [glue] to attach the extension to the natural follicle, and eyes are incredibly sensitive to these chemicals,” says Dr. Nazarian. “Even many hypoallergenic ingredients can still inflame or irritate tissue by weighing them down or pulling on the hairs... hence the inherent problem with extensions.” She continues, “Anything around the eyes can irritate, either due to the chemicals or due to the friction and tugging forces around the lashes.” To prevent irritation and allergic reaction, it’s a good idea to do a patch test on your hand with the adhesive. Dr. Nazarian also recommends that you request your esthetician use a latex- and formaldehyde-free adhesive, since these ingredients are two of the most common irritants.2
Investment of Time and Money: Your initial set will cost anywhere from $100-300, with refills setting you back around $50-150 every 2-4 weeks. Getting your initial set can take up to two hours, with refill appointments lasting up to an hour.
Potential Damage to Natural Lashes: Even if you see the best lash artist and execute your aftercare perfectly, it’s still very possible that you’ll see damage to your natural human hair eyelashes. As your natural lashes grow, your extensions get farther and farther from the root of the lash. This makes it harder for your natural lashes to support the weight of the extension, which can cause breakage. Rubbing or itching your lashes in your sleep (either with your hands or against your pillow) can also cause damage to natural lashes. 3
Uneven Fallout: Your lashes are at all different stages of growth at any given time, which means that some lashes are in a period of growth, while others are getting ready to shed. This means that a few weeks after your appointment, some extensions will fall out as lashes shed and are replaced with new, extension-free eyelashes, while others will remain in tact. This can create an uneven, scattered effect if you don’t get your extensions refilled every 2-4 weeks.
Washing Your Face Is a Pain: Remember that you can’t rub your eyes when you have eyelash extensions, which means you have to work around the eye area when you’re washing your face.
|
|
|
Freezing in Glass (No More Broken Jars!) |
Posted by: ye28ye - 10-11-2021, 05:31 AM - Forum: My Forum
- No Replies
|
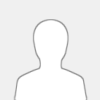 |
Creating glass containers can be accomplished by one of two different processes – the Blow and Blow, or the Press and Blow process. Each process is chosen based on the kind of glass bottle being made. All glass bottles start out as raw materials. Silica (sand), soda ash, limestone, and cullet (furnace-ready, recycled glass) are combined into a specific mixture based on the desired properties of the bottle. The mixture is then melted at high temperatures in the furnace until it becomes a molten material, ready for formation. The type of glass this mixture will produce is known as soda-lime glass, the most popular glass for food and beverages.
Glass Forming Methods
Molten glass gobs are cut by a perfectly-timed blade to ensure each gob is of equal weight before it goes into the forming machine. The weight of a gob is important to the formation process for each glass container being made. The molded glass is created by gravity feeding gobs of molten glass into a forming machine, where pressure forms the neck and basic shape of the bottle. Once the neck finish and the general glass bottle shape has been achieved, the form is known as a parison. To achieve the final container shape, one of two processes are used.
Press and Blow Process
The Press and Blow process is the most commonly used method in glass bottle manufacturing. It uses an individual section (IS) machine, which is separated into varying sections to produce several containers of the same size simultaneously. The molten glass is cut with a shearing blade into a specific gob size. The gob falls into the machine by force of gravity. A metal plunger is used to push the gob down into the mold, where it starts to take shape and become a parison. The parison is then transferred into the blow mold and reheated so that the parison is soft enough to finish off the dimensions of the glass. Once the parison is reheated to blowing temperature, air is injected to blow the container into shape. Press and blow methods are typically used for manufacturing wide-mouth bottles and glass jars as their size allows the plunger into the parison.
Blow and Blow Process
The Blow and Blow process is used to create narrow containers. It also requires an IS machine, where gobs of molten glass are gravity fed into the mold. The parison is created by using compressed air to form the neck finish and basic bottle shape. The parison is then flipped 180 degrees and reheated before air is again injected to blow the container into its final shape. Compressed air is once again used to blow the bottle into its desired shape. Blow and Blow methods are best used for glass bottle manufacturing requiring different neck thicknesses.
Finishing the Process
Regardless of the process used, once the bottle has been completely formed, it is removed from the mold and transferred to the annealing lehr. The lehr reheats the bottes to a temperature of about 1,050 degrees Fahrenheit then gradually cools them to about 390F. This process allows the glass to cool at an even rate - eliminating internal stresses in the glass that could lead to cracking or shattering. Bottles are then subjected to careful inspections to ensure they meet quality control guidelines. Any bottles showing imperfections, including bubbles, cracks, or misshapen areas, are removed from the line and used as cullet. All remaining bottles are sorted according to size and type. The bottles are then packaged on pallets and prepared for shipping.
Keeping your freezer filled with homemade broth is a fantastic way to keep your home stocked with healthy convenience food. But after stewing and brewing all that broth, you need a simple, nontoxic way to store it.
Plastic containers can work fine in a pinch, but plastic food storage does come with some concerns about leeching chemicals. Pressure canning the broth in glass jars in another option, like a CBD flower jar, but requires more work and attention.
Filling up a glass jar and popping it in the freezer, though? Now that’s a whole lot simpler.
Simple Tips for Freezing in Glass
1. Cool Your Broth
A great place to start is to cool your broth before ladling into the jars, then completely cool the jars of broth in the fridge before freezing.
This does two things:
It won’t shock the jars when you fill them with broth (that means giving them such a huge temperature change that the glass shatters), and
You won’t burn yourself by ladling hot broth into jars and spilling on yourself. Not that such a thing could ever happen in my kitchen.
2. Fill With Less Broth Than You Think
This is a really easy mistake to make and was my biggest mistake in the past.
I used to leave 1-2 inches of headspace in the jars when filling them up with broth, thinking that there was plenty of room for it to expand while freezing. But most of them would still break and crack. I was stumped.
Turns out that it isn’t the top of the jar you need to be mindful of when filling your jars. It’s the shoulders.
Anytime you freeze in a glass jar that has shoulders, you have to make sure that the broth stays below the shoulders while it freezes and expands. That means that the broth should be 2-3 inches below the shoulders before you stick it in the freezer.
3. Use Wide Mouth Mason Jars
Instead of using regular qube jars and worrying about the shoulders, you can use wide mouth mason jars.
These wide mouth jars really are the best for freezing broth. Since they lack the shoulders that most jars have, the jar isn’t put under pressure when the broth freezes and expands. I don’t have many of these, but I do reach for them first when I go to freeze broth.
Someone even told me that they stick warm broth right in the freezer in wide mouth jars with nary a glass casualty.
4. Cap Loosely
When jars are tightly capped before freezing, they tend to break more often. If you just loosely place the lids on until the broth is totally frozen, the jars hold up better. (These lids are especially handy when storing food in jars.)
Once the broth is frozen, you can tighten the lids if you remember. It’s not a big deal if you forget, though. I rarely think to do it!
5. Leave Space Between Jars in the Freezer
For some reason, jars that are touching when placed in the freezer seem to break more readily, as well. This problem has another simple solution: just leave a little space between the jars when placing in the freezer.
There are great tips in the comments section, so give them a scan if you want more ideas! Some of my favorites:
Place your jars in a cardboard box (like the one mason concentrate jar sets are sold in) before putting in the freezer. This allows you to easily keep some distance between them and can also be handy if you use a chest freezer. Or use a JarBox, a genius product!
Slip your jars into clean socks before putting them in the freezer. This prevents them from bumping against each other and breaking that way.
Try Glasslock storage containers. The glass is tempered, so it’s stronger and better able to handle temperature changes. They are pricier than canning or repurposed weed jars, but might be an investment you’d like to make since you can also cook with them.
Stick with jars that are designated as freezer-safe, like these pint-and-a-half wide mouth jars, or use smaller size jars like wide mouth pint, half-pint, and 4-ounce.
|
|
|
What is Quartz Glass? |
Posted by: ye28ye - 10-11-2021, 05:25 AM - Forum: My Forum
- No Replies
|
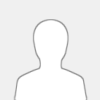 |
Quartz is one of the most abundant and widely distributed minerals in nature. Quartz is the only stable polymorph of crystalline silica on the Earth‘s surface. It is found in all forms of rocks: igneous, metamorphic and sedimentary. It becomes concentrated in soils, bodies of water and sand when a quartz-bearing rock is weathered or eroded.
The chemical formula of quartz is SiO2. The silicon-oxygen (Si-O) bond is polar and covalent. Elemental silicon contains four valence electrons making the silicon atom bonded to four oxygen atoms. One oxygen atom is bonded to two silicon atoms, making the body-centered tetrahedral crystal system of quartz. The tetrahedral crystal system is composed of four oxygen atoms at the corners and a central silicon atom. In one tetrahedron, the O-Si-O bond makes a 109° angle. In a network of SiO4 tetrahedra, the corner oxygen atoms link the central silicon atom. The Si-O-Si bond makes a 144°. The structure of the networked SiO4 is open with wide spaces, hence giving quartz a hexagonal crystalline form.
Quartz can be manufactured into quartz glass, which is valued for its exceptional purity and serves a wide range of applications. Quartz glass does not contain additives. It is sometimes referred to as fused quartz or fused silica; the difference between the two is that fused quartz is made from pure silicon dioxide (SiO2) while fused silica is made from synthetic precursor. Natural quartz is rarely used in the industry since it may contain several impurities; the most commonly used raw material is "cultured quartz", which is quartz crystals that are grown in controlled conditions.
Quartz glass is valued due to its distinct and high value characteristics. Among these are because of its low coefficient of thermal expansion, high gas permeability, and extensive optical transmission.
Production of Quartz Glass
This chapter presents the steps in transforming the raw quartz into a formed, fused quartz glass.
Washing and Drying
Dirt, moisture and contaminants present in the natural quartz are removed in the early stages of processing which may affect the quality and performance of the quartz glass to be produced. This is only applicable for mined quartz banger.
Comminution
The objective of this step is to reduce the raw quartz into a size suitable for the fusion method and machinery to be utilized. Natural quartz undergoes a series of size reduction steps such as crushing and milling (ball milling or roll milling). Quartz is very brittle in nature, which makes comminution quite easy. Afterwards, the particle size is analyzed and larger grains are separated.
Fusion
In this stage, thermal energy is used to break the strong silicon-oxygen bond. With increasing temperature, more bonds are broken and result in the less viscous flow of quartz. After shaping and cooling to its final form, the ordered crystalline structure of SiO2 molecules is converted into a vitreous, amorphous structure and metastable form of quartz.
Depending on the desired purity level and end use application, the natural quartz may be homogenized and formed through the following fusion methods:
Electric fusion
This method produces an industrially known Type I quartz glass. Electric fusion method is used if a high level of purity and low hydroxyl (OH) content (> 1 ppm – 30 ppm) is to be obtained. The quartz glass with low OH content produced from this method has high infrared transmission, but aesthetically pleasing bubbles and drawing lines are present in the glass surface. The starting material is natural quartz grains, and may be subject to the following production modes:
Continuous Mode: The quartz sand is continuously fed on top of a refractory metal crucible column which contains an electric heating device. The internal chamber of the crucible is maintained at a dry and vacuum-sealed atmosphere to keep the melted quartz from reacting with the refractory material. After passing through the hot crucible column, melted quartz is collected in an orifice located at the bottom of the column in which it is shaped and cut into plates, tubes and rods. This method is suitable for high volume manufacturing.
Batch or Boule Mode: Large quantity of quartz is placed inside a refractory-lined vacuum chamber which also contains an electric heating device. After the quartz is fused, the viscous melt is collected and shaped into its final form. This method is used to create quartz glass with more sophisticated shapes and details.
Flame Fusion
In this method, a natural quartz or a synthetic precursor can be a starting material. Natural quartz passes through a chamber with a high temperature hydrogen/oxygen (H2/O2) flame until the starting material is fused. If silicon tetrachloride (SiCl4), a gaseous synthetic precursor, is to be used, it is made to react with the H2/O2 flame. The viscous melt is deposited in a refractory-lined vacuum chamber, collected slowly by a die at the bottom of the container, and shaped to its final form. Due to its direct contact with H2/O2 flame, this method produces quartz glass with 150-200 ppm OH content from natural quartz and up to 1000 ppm for synthetic silica.
Glass produced from crystal quartz through flame fusion is classified as Type II, and from synthetic precursor as Type III. Type III synthetic silica glass is a product of a chemical reaction. The combustion of silicon tetrachloride gives synthetic quartz and leaves environmentally toxic byproducts, chlorine, and hydrochloric acid.
Plasma Fusion
This process is similar to flame fusion with water-vapor free plasma flame being used as a source of heat. Plasma fused quartz glass has high purity level, low OH content, minimal bubble content and no drawing lines.
Natural quartz or a synthetic precursor may be the starting material for this method. Quartz glass produced from the combustion of a synthetic precursor in plasma flame is known as Type IV.
Electric Arc Fusion
The quartz sand is melted in an electric arc furnace. The resulting glass ingots are crushed and molded; the formed parts are dried and sintered. In this method, the quartz flask glass produced is white and opaque and does not generally belong to any types of quartz glass. However, it is comparable to transparent quartz in terms of purity level.
Shaping and Finishing Processes
A manufacturer can process quartz glass just like any other kinds of glass.
Mechanical forming
Shaping and forming of quartz glass may require diamond cutting tools due to its hardness. Also, such operating parameters must be optimized since the quartz glass is also brittle and there is a limited force that can be applied before cracking or fracture occurs. Some of the mechanical processes include:
Cutting: Band and wire saws, chop saws, CO2 lasers, and water jet cutters are used to cut the quartz glass. Using a laser cutter can leave a glazed and smooth cut, while those quartz glass which used saw cutting can leave a rough cut. Thick quartz glass sheet slabs may require multiple consecutive cuts if a single cut would not suffice. Annealing may be required to relieve the thermally-induced stress and to keep it from shattering.
Drilling: As detailed in the fused quartz glass product, holes may be produced using a diamond driller. A laser driller may be used to cut thin, small plates. Proper cooling must be ensured in order to prevent the tools from premature worn-out.
Grinding: The quartz glass surface may be smoothened and its thickness may be reduced, depending on the end-use application.
Hot Forming
The quartz glass is quite complex to thermoform due to its high melting point and steep viscosity, allowing it to be formed on a very narrow temperature range. If the temperature is too low, the glass is solid; if the temperature is too high, the glass is less viscous and volatile resulting in evaporation of the parts. In addition to this, single or multiple annealing steps are required to relieve the thermal stress and prevent fracture induced by hot forming. The following are some hot forming methods which a manufacturer can use in order to enhance the glass product:
Welding: Two components of quartz glass are joined together through a weld. The ends of each component are heated, and a piece of quartz glass is melted to fill the gap in the seam or joint. It is critical to keep the temperature just high enough in order to avoid thermal stress.
Collapsing: In this process, quartz glass rods are reduced to a smaller diameter. A metal tube is heated to the softening temperature of the quartz glass and pressure is applied under the tube to push the glass rods.
Elongation and Compression: A positive or negative radial force is applied to elongate or compress the quartz glass rod to its final diameter. This is performed at the softening temperature of the quartz glass, and an optimal force must be applied in order to prevent fracture and cracking.
Glass Blowing: A piece of molten quartz glass is inflated with the aid of a blowpipe in order to acquire a hollow shape.
Properties of Quartz Glass
This chapter presents the notable properties and characteristics of quartz glass.
Chemical Purity
Purity is one of the most important aspects in quartz glass manufacturing. Contaminants, even in very low levels, influence the thermal, electrical and optical properties of the resulting quartz tube glass and material in contact in their final application. Strict handling precautions must be taken at the starting material source and all stages of production to ensure high purity. The most common impurities are metal oxides (Al2O3, Fe2O3, MgO, etc.), water, and chlorine.
Water is present in quartz glass as hydroxyl (OH) groups. The OH content can change depending on the thermal treatment and amount of moisture to which the quartz glass is exposed at an elevated temperature. OH influences infrared transmission, viscosity and attenuation. High levels of OH reduces infrared transmission. OH also lowers thermal stability; higher OH content means that the quartz glass is not suitable for high temperature end applications. An annealing step may reduce the OH content of the quartz glass in electric fused quartz glass.
Chemical Behavior
Quartz glass is chemically inert to most chemical compounds: water, salt and acids, making it an advantageous material in chemical laboratories and industries. It is essentially impermeable to gases. Hydrofluoric acid and phosphoric acid are the only agents that can etch and disintegrate quartz glass at ambient temperatures. However, alkali and alkali earth agents attack the surface, causing accelerated devitrification. 0.1 mg of alkali per square centimeter of alkali compounds can amplify to transform all of the semi-stable molecules. Even fingerprints, which contains traces of alkali, can trigger devitrification.
Thermal Properties
Quartz glass is known for its very low coefficient of thermal expansion (CTE). Thermal expansion refers to the fractional change in size of an object in response to the change of its temperature. For most materials, CTE is directly proportional to temperature change. Quartz glass also has excellent thermal shock resistance, which can withstand sudden and extreme changes in temperature. Quartz glass instrument also has low thermal conductivity.
Quartz glass is softened starting at 16300C and acts like a viscous liquid at high temperatures like most glass types. This state occurs at a wide range of temperature, and viscosity decreases with increasing temperature. Viscosity is also increased by the presence of impurities.
Mechanical Properties
Quartz glass has almost similar mechanical properties compared to other glass types. Quartz glass rod has high compressive strength, but also exhibits high brittleness. Surface defects can also affect the overall strength of this material. Machine-polished parts tend to be weaker than fire-polished ones. Also, the age of the glass also affects reliability due to exposure to the environment.
Optical Properties
Quartz crucible glass has been a subject of research due to its extensive optical transmission properties, covering the ultra-violet regions, visible and infrared wavelengths. It can be further enhanced through addition of doping materials. Transmission is influenced by the quartz glass‘ purity and OH content. The increase in metallic impurities and OH-molecular vibrational and rotational excitations can lead to light absorption and hence affect the consequent transmission.
Electrical Properties
Quartz glass is an excellent electrical insulator, retaining high resistivity at elevated temperatures. It has a high dielectric strength. This is due to the absence of charged mobile ions in the molecular lattice and the strong silicon-oxygen bond which imparts very low polarizability to the structure.
|
|
|
Choosing the Right Folder-Gluer |
Posted by: ye28ye - 10-11-2021, 05:19 AM - Forum: My Forum
- No Replies
|
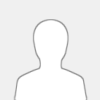 |
The search for a new folder-gluer can be very daunting. There are many folder-gluer OEMs out there and each have different models, features and sizes designed for a variety of applications. When a finisher or folding carton manufacturer is in the market for an upgraded or new folder-gluer, there are several questions to ask in order to find the best fit for the market they are involved in or attempting to enter.
1. Do you run paperboard or corrugated?
The paperboard market includes folding paper cartons – sometimes referred to as just folding cartons. The corrugated market produces folding boxes that often are referred to as cardboard boxes. The folding/gluing machines for these two distinctive markets may look similar, but the design and structure of the machines are quite different. There are folder-gluers that will produce products using both of these substrates, but on a limited basis. In other words, if you wish to produce corrugated C flute boxes, don’t expect the same folder-gluer machine to produce 12-point folding paper cartons – at least not efficiently.
In addition, the paperboard folding carton market typically will have more variety to the carton styles (more folded panels) than the corrugated box market. Taking this into consideration, the folder-gluer for paperboard typically has to be more versatile in its design in order to produce a wider range of carton styles. However, a “specialty folder-gluer” for corrugated can be equipped to run some of the same styles as well and may need to run special folds for applications such as POP displays.
2. What size and style of products are you running now or considering running in the future?
Let’s take bottle carriers, for example. There are some OEMs that have designed a special section of the machine that will turn the product 90 degrees inline to the running direction. These sections are amazing to watch and can run at very high speeds. However, they are available at a considerable cost and add permanent length to the folder-gluer.
If your product line has only a couple of designs that require turning, this additional section will need to be set-up to allow other products to pass through it when not turning. If you have large -volume products that need turning, this section may work very well for you. If not, you may want to consider looking at a machine that offers tooling instead of a turning section. Tooling can be placed on the folder-gluer to turn the product, will not increase the length of the machine and can be removed from the machine when not in use. Cost savings are great. Running speed can be an issue here as the tooling will not allow the machine to run some products as fast as the turning section will. Some OEMs offer a “Right-Angle” machine for those companies that have a lot of products or long runs that require 90-degree turning. A right-angle machine offers a simpler set-up and an increased running speed when compared to the tooling option.
Other items to think about are the features and age of your current folder-gluer. Obviously, you wouldn’t be considering another folder-gluer if you haven’t examined the abilities and features of what you already have on your floor. Age can equate to repairs, and upgrade installations (if available) can lead to downtime and added cost. If you need a machine that can run 4-/6-corner products and your current side gluing folder gluer is not equipped to run them, your options are limited.
On a side note, one also must consider the folder-gluer operator. Good operators are getting hard to find these days. Having one who can understand (or has experience) on the new mechanical and electronic systems is a real plus. Having an operator who has confidence in his ability to make the transition from the old methods to the newer ones also is a plus. Either way, the operator should be included in this process in order to give an opinion and feedback. The operator can get some questions answered from the OEM during the demonstration as well. Even operators who have many years of experience can feel challenged if the company they work for decides to enter into a different market. Now the operator must learn how to run the different carton styles that the new market presents and a new folder-gluer as well.
3. What does your budget allow? What can you afford?
The price range for a new folder-gluer can run from around $200,000 for a small, simple machine designed to do simple-style products to well over a million dollars for a machine that can do large, complex styles. The price should be reflective of the technology that went into the design. However, this is not always the case. It is important to analyze all the different box folder-gluers on the market, with 4/6 corner box folder, the features available and how those features meet the type of cartons you will be running. Look for extended-length parts warranties that are included in the base price. Extra operator training also can be included, in many cases, as incentive for purchase.
When comparing different pre-folding folder gluer and looking at the technology included, you have options.
Option 1.
Option 1 is a model that is automated with a system that can record and store the job names, carrier locations and all systems settings, with the ability to recall them, accurately place the carriers and energize the different systems for future repeated runs. These types of folder-gluers find a good home in companies that have a lot of repeat jobs or small runs that can come up during another run. That means the operator must pull the current job off of the machine and set-up the new order. That can lead to excessive waste. An automated folder-gluer that can set itself up on repeat jobs can reduce these potential inefficiencies and can save money in the process.
Of course, folder-gluers with the automation option will be at the higher end of the price tag, but can offer cost savings in the form of reduced waste, quicker set-up times, increased accuracy for set-ups and, in turn, a higher quality product that may eventually pay for itself.
Another benefit of the automated folder-gluer is that your jobs are stored in the memory program of the machine. In the situation where an operator is out for vacation or sick, a job that is stored in the memory program can be recalled by another operator. Look for automated set-up processes that not only set-up the entire folder-gluer but also will include automation for adjusting individual carriers and individual sections of the machine.
Option 2.
This is a model without automation, but with motorized carriers. This option can save on the initial cost outlay for a new folder-gluer. Even though there isn’t a memory bank of jobs to recall from when repeating jobs, motorized carriers still can save a lot of time during the set-up. Motorized carriers often will allow the operator to look over a specific area of the machine while moving the carrier(s). Folder-gluer machines that offer a numerical carrier position indicator also will help the operator place the carrier. Although these indicators are not usually very accurate compared to the automated method, the operator still can write down the numerical position of each carrier and refer to this for future set-ups.
Option 3.
Option 3 is a model without automation or motorized carriers. The operator uses a hand crank to move and adjust each carrier position. This is even less costly and is old school for sure. But, it can fit into the overall budget better and the set-up methods of the seasoned operator. Numerical carrier position indicators should be a must have for repeat jobs; however, most seasoned operators won’t use them. This is okay as long as the job is set-up in good time and the waste is low. Experienced operators generally know what they are doing on a crash lock bottom folder gluer but would be well-served using the new technology to increase their knowledge and productivity.
A final consideration is the method of packing the cases with cartons or banding the bundles of boxes. You may have made improvements to your finishing department to make it more efficient with an upgrade to your folder-gluer, but how you handle the product as it exits the folder-gluer also should be considered. This will be discussed in a future article on automating the feeding, exiting and packing of the cartons.
|
|
|
What Is Microfiber Leather |
Posted by: xiop2v - 10-09-2021, 05:28 AM - Forum: My Forum
- No Replies
|
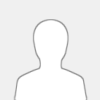 |
Microfiber leather is an abbreviation of ultrafine fiber PU synthetic leather. It is a non-woven fabric made of three-dimensional structure network by carding acupuncture with microfiber staple fiber. After wet processing, PU resin impregnation, alkali reduction, and dermabrasion and polishing And other processes eventually make microfiber leather. It is made by adding ultra-fine fiber to PU polyurethane, which makes the toughness, air permeability and abrasion resistance further strengthened; it has extremely excellent abrasion resistance, excellent cold resistance, breathability, and aging resistance. Eco-friendly, Comprehensive performance beyond real leather. Widely used for automotive, garment, bags, sofa, shoes, boots, basketball, belt, jewellery box and so on. We are specialize in microfiber leather production manufacture.We provide the optimal leather options, the best leather substitute and best leather alternatives for automotive seat covers and interiors, furniture & sofa upholstery, footwear and shoes, bags, garments, gloves, balls, etc.
While synthetic leather were once considered not suitable for high quality shoes, PU microfiber leather has changed how shoes are made.
Microfiber leather is designed to hold up against weather conditions and the wear and tear of walking and running over an extended period of time.
They can retain their form very well, and thus are usually very durable if cared for properly. They're also more water-resistant and lighter than real leather, making them great for long wear and outdoor activities.
We found this video, below, that tests how durable shoes made with suede microfiber leather are. Check it out!
The difficulty in dyeing microfiber base filled with ordinary polyurethane presents a significant challenge in maintaining the uniformity and highly realistic appearance of the resulting products. In the present study, a type of acid-dyeable polyurethane (PU-MDEA; MDEA=N-methyldiethanolamine) was synthesized, and its chemical structure and dyeing properties were investigated. Nuclear magnetic resonance analysis indicated that cationic groups were successfully incorporated into the PU-MDEA backbone via chain extension using MDEA. The amorphous nature of PU-MDEA was determined by differential scanning calorimetry, X-ray diffraction, and polarizing optical microscopy. Owing to the strong binding between these cationic groups and acid dye, as well as the reduced resistance to dye penetration, PU-MDEA showed better dyeability toward the acid dyes studied herein when compared with the control sample (microfiber synthetic leather filled with ordinary polyurethane). The adsorption isotherm experiment revealed that the dyeing process conformed to the Langmuir model, thereby indicating that the acid dyes attached to PU-MDEA via strong ionic bonding rather than van der Waals forces or hydrogen bonding. Additionally, it was found that the wastewater resulting from the dyeing of the microfiber synthetic leather filled with PU-MDEA exhibited environmentally friendly characteristics when compared with that displayed by the control sample (microfiber synthetic leather filled with ordinary polyurethane). Thus, the current results show the potential of PU-MDEA, as a filler, in the manufacture of microfiber synthetic leather to achieve fast dyeing rate, high dye uptake, and good color fastness, thereby improving the uniformity and highly realistic appearance of the resulting products.
BONDED LEATHER VERSUS MICROFIBER
A much more sophisticated form of faux leather: polyurethane resin and ultra- fine microfiber leather for automotive are combined to replicate the microscopic structure of leather. The complexity of its construction mean that it is more expensive than other faux products but it does have a number of advantages over bonded leather. It doesn’t scratch or tear and is non-fading. It breathes like real leather but it also has ant -bacteria and anti-mildew properties. Unlike bonded leather it is completely odourless.
|
|
|
Cast Iron Pipe |
Posted by: xiop2v - 10-09-2021, 05:17 AM - Forum: My Forum
- No Replies
|
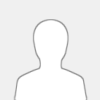 |
Cast iron pipes can fail in many modes which in general can be summarized into two categories: loss of strength due to the reduction of wall thickness of the pipes, and loss of toughness due to the stress concentration at the tips of cracks or defects. Even in one category there can be many mechanisms that cause failure. The strength failure can be caused by hoop stress or axial stress in the pipes. A review of recent research literature (Sadiq et al., 2004; Moglia et al., 2008; Yamini, 2009; Clair and Sinha, 2012) suggests that current research on pipe failures focuses more on loss of strength than loss of toughness. As was mentioned in Section 3.3.7(b), the literature review also revealed that in most reliability analyses for buried pipes, multifailure modes are rarely considered although in practice this is the reality. Therefore the aim of this section is to consider multifailure modes in reliability analysis and service life prediction for ductile iron pipe. Both loss of strength and toughness of the pipe are considered. A system reliability method is employed in calculating the probability of pipe failure over time, based on which the service life of the pipe can be estimated. Sensitivity analysis is also carried out to identify those factors that affect the pipe behavior most.
Buried pipes are not only subjected to mechanical actions (loads) but also environmental actions that cause the corrosion of pipes. Corrosion related defects would subsequently cause fracture of cast iron pipes. In the presence of corrosion pit, failure of a pipe can be attributed to two mechanisms: (i) the stresses in the pipe exceed the corresponding strength; or (ii) the stress intensity exceeds fracture toughness of the pipe. Based on these two failure modes, two limit state functions can be established as follows.
Steel pipe is manufactured by the pit, horizontal or centrifugal method. In the vertical pit method, a mold is made by ramming sand around a pattern and drying the mold in an oven. A core is inserted in the mold and molten iron is poured between the core and the mold. In the horizontal method, a machine is used to ram sand around horizontal molds that have core bars running through them. The molten iron is poured into the molds from multiple-lipped ladle designed to draw the iron from the bottom to eliminate the introduction of impurities. In the centrifugal method (Figure 3.4), sand-lined molds are used that are placed horizontally in centrifugal casting machines. While the mold revolves, an exact quantity of molten iron is introduced, which, by action of the speed of rotation, distributes itself on the walls of the mold to produce pipe within a few seconds.
Since cast iron pipes are deteriorating rapidly and causing so many maintenance problems (Section 4.3.2), the distribution network is currently undergoing an extensive replacement scheme with old, leaking and corroded cast iron pipes being replaced by MDPE and uPVC. These new plastic pipe materials are thought to support fewer bacteria than the old hubless cast iron pipe. Their surface is smoother and therefore the surface area smaller and they are not subject to corrosion or biodeterioration.The Putney gas explosion was a real wake-up call, and accelerated the replacement of old gray ductile iron pipe fittings by polymers such as medium-density polyethylene (MDPE), high-density polyethylene (HDPE), and unplasticized polyvinylchloride (UPVC). HDPE has a tensile strength of ≈20–37 MN m−2 (which is more than adequate for typical internal pressures). Most importantly, though, it has a Young’s modulus which is ≈150–300 times less than cast iron. This means that HDPE pipes can deflect under misalignments of the kind experienced in the Putney explosion without reaching the fracture stress. Even better, over a long time the polymer also creeps, which further dissipates the stresses caused by misalignment. Polymers are also very resistant to corrosion, so should last indefinitely in the ground.By the 1870s, a 2000-mi network of small-diameter gathering lines connected the oil-producing areas with regional refineries and storage points on the railroads and rivers where the oil could be shipped to refineries via railcars or ships and barges. Typical crude oil trunk lines were constructed of 18-ft sections of lap-welded wrought steel pipe fittings 5 or 6 in in diameter joined with tapered, threaded joints manufactured specifically for pipeline service. The pipe was generally buried 2 or 3 ft below the ground surface. Worthington-type pumps were used as the motive power for the lines, and the pumps were powered by steam generated by coal-fired boilers. Pump stations were spaced as needed to maintain the flow of oil over the terrain crossed by the lines. At the pump stations, oil was withdrawn from the lines and passed through riveted steel receiving tanks some of which were 90 ft in diameter and 30 ft high holding about 35,000 barrels (The Engineering and Building Record, 1890; Scientific American, 1892; Herrick, 1949). Diesel-powered pumps began to replace steam power around 1913–1914 (Williamson et al., 1963).
|
|
|
Rethinking the bottle |
Posted by: xiop2v - 10-09-2021, 05:08 AM - Forum: My Forum
- No Replies
|
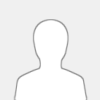 |
When I was younger, wine came in a glass bottle, and—outside of a few value-priced boxed options—that was that. But now, quality wine comes in all sorts of packaging: boxes, cans, pouches, even slim wine bottles that can fit through a mail slot. Of course, the bottle is still king—but even that classic container isn’t beyond innovation. The British company Frugalpac has just launched a standard-sized wine bottle made mostly out of recycled paper.
Digging into the specifics, a Frugal Bottle weighs about 3 ounces, whereas burgundy bottles can weigh about a pound. Additionally, Frugalpac says that beyond offering a carbon footprint that is 84 percent lower than a glass bottle, it’s also “more than a third less than a bottle made from 100 paper recycled plastic,” with a “water footprint is also at least four times lower than glass.” And, yes, the paper bottle is easy to recycle—because the liner inside is removable: “Simply separate the plastic food-grade liner from the paper bottle and put them in your respective recycling bins.”
“Frugalpac’s business model is to supply Frugal Bottle machines for wine producers or packaging companies to manufacture the bordeaux bottles on their site, cutting carbon emissions even further,” Waugh added. “Materials can be purchased locally through existing paperboard printers to give maximum freedom of design and the best commercial offering.”
Naturally, the company offers an environmental pitch, as well. “Our mission is to design, develop and supply sustainable packaging. The Frugal Bottle is up to five times lighter than a glass bottle, has a carbon footprint up to six times lower and is easy to recycle again,” explained Frugalpac chief executive Malcolm Waugh. “We’ve had fantastic feedback from people who’ve trialed the Frugal Bottle. As well as the superior environmental benefits, it looks and feels like no other bottle you have ever seen.”
Digging into the specifics, a Frugal Bottle weighs about 3 ounces, whereas ice wine bottles can weigh about a pound. Additionally, Frugalpac says that beyond offering a carbon footprint that is 84 percent lower than a glass bottle, it’s also “more than a third less than a bottle made from 100 paper recycled plastic,” with a “water footprint is also at least four times lower than glass.” And, yes, the paper bottle is easy to recycle—because the liner inside is removable: “Simply separate the plastic food-grade liner from the paper bottle and put them in your respective recycling bins.” For many of us wine drinkers, our first conscious act towards saving the planet was to separate champagne bottles from the rest of our rubbish. It made us feel pretty good, even though most of us were — and continue to be — shockingly ignorant about what then happens to them.
|
|
|
Why stainless steel corrodes |
Posted by: xiop2v - 10-09-2021, 05:00 AM - Forum: My Forum
- No Replies
|
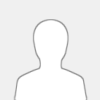 |
Stainless steel has unique properties which can be taken advantage of in a wide variety of applications in the construction industry. This paper reviews how research activities over the last 20 years have impacted the use of stainless steel in construction. Significant technological advances in materials processing have led to the development of duplex stainless steel tubing with excellent mechanical properties; important progress has also been made in the improvement of surface finishes for architectural applications Structural research programmes across the world have laid the ground for the development of national and international specifications, codes and standards spanning both the design, fabrication and erection processes. Recommendations are made on research activities aimed at overcoming obstacles to the wider use of stainless steel in construction. New opportunities for stainless steel arising from the shift towards sustainable development are reviewed, including its use in nuclear containment structures, thin-walled cladding and composite floor systems.
In summary, stainless steel does not rust because it is sufficiently reactive to protect itself from further attack by forming a passive corrosion product layer. (Other important metals such as titanium and aluminum also rely on passive film formation for their corrosion resistance.) Because of its durability and aesthetic appeal, 304 stainless steel 3 inch pipe is used in a wide variety of products, ranging from eating utensils to bank vaults to kitchen sinks.
Completely and infinitely recyclable, stainless steel is the “green material” par excellence. In fact, within the construction sector, its actual recovery rate is close to 100%. Stainless steel is also environmentally neutral and inert, and its longevity ensures it meets the needs of sustainable construction. Furthermore, it does not leach compounds that could modify its composition when in contact with elements like water.
In addition to these environmental benefits, 304 stainless steel round tube is also aesthetically appealing, extremely hygienic, easy to maintain, highly durable and offers a wide variety of aspects. As a result, stainless steel can be found in many everyday objects. It also plays a prominent role in an array of industries, including energy, transportation, building, research, medicine, food and logistics. Austenitic Stainless Steels: These are the largest group of stainless steels which comprise around two-thirds of all 304l stainless steel tube production. Their austenitic microstructure allows them to be tough and ductile, even at cryogenic temperatures. Moreover, they do not lose their strength when subjected to high temperatures. These attributes result in excellent formability and weldability. Since the austenitic structure is maintained at all temperatures, they do not respond to heat treatment. Their hardness and high tensile strength are acquired through cold working. Austenitic stainless steels are further divided according to the austenite forming elements.Martensitic Unit Cell: These stainless steels have higher amounts of carbon that promotes a martensitic microstructure. Martensitic stainless steels are hardenable by heat treatment. When heated above its curie temperature, they have an austenitic microstructure. From an austenitic state, cooling rapidly results in martensite while cooling slowly promotes the formation of ferrites and cementite. Varying the carbon content results in a wide range of mechanical properties which makes them suitable for engineering steels and tool steels. Increasing the carbon content makes the stainless steel harder and stronger while decreasing it makes the alloy more ductile and formable. However, adding more carbon results in lower chromium to maintain a martensitic microstructure. Thus, higher strength is attained at the expense of corrosion resistance. They generally have lower corrosion resistance than ferritic and austenitic 316 stainless pipe.
|
|
|
What are the advantages of time recording machine in an office ? |
Posted by: xiop2v - 10-09-2021, 04:49 AM - Forum: My Forum
- No Replies
|
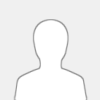 |
In the 1890s, timekeepers-- clerks who kept track of employees' hours in handwritten logs --found that machines were beginning to replace them, especially in workplaces with large numbers of employees. Thanks to the influence of the advocates of scientific management, nearly every industrial workplace had a time clock, after about 1910. So did many offices. By the early twentieth century the International Time Recording Company supplied an entire line of timekeeping devices, including master clocks, several types of time clocks, and time stamps. Founded in 1900, the firm continuously expanded its product line, underwent several reorganizations and name changes, and emerged in 1924 as the International Business Machine Corporation, familiar today as IBM.One of the firm's most popular products was the card punch time recorder, a clock that could furnish a daily or weekly record of up to 150 employees. Based on the 1888 patent of physician Alexander Dey, the dial time recorder was essentially a spring-driven clock with a cast-iron wheel affixed to its dial side. The rim of the wheel was perforated with numbered holes. As employees pressed a rotating pointer into the hole at their assigned number, the machine recorded the time on a preprinted sheet and rang a bell with each punch. A two-color ribbon printed all regular time in green and all tardiness, early departures, and overtime in red.This International digital card punch time recorder hung in a factory in the garment district of New York City.
Different mechanical devices have been designed for recording the exact time of the workers. These include:
(a) Time Recording Clocks
(b) analogue card punch time recorder
(a) Time Recording Clocks
This method has been developed to remove some of the difficulties faced in case of manual methods. Under this method, the attendance is marked by a time recording clock on a card. Every worker is allotted a time card usually for one week duration.
This machine can also! calculate the wages of the workers with greater accuracy and avoids much loss of time, I But a heavy capital investment is needed and hence only large organisations can use It is also necessary to have a close supervision on every worker to prevent fraud and I irregularities.
Make employee scheduling and pay calculation easier with this fingerprint time attendance. A perfect choice for tracking hours in busy workplaces, this time stamp keeps accurate time within fractions of a second by automatically syncing with codes from the National Institute of Standards and Technology. This device automatically adjusts for Daylight Saving Time and ensures consistent accuracy during power failures using an internal battery backup. Featuring over 150 print configurations and 13 messages in four languages, this device makes it easy to print custom messages in two hour formats and a variety of font sizes. Compatible with a variety of forms and time cards, this flexible machine aligns any document perfectly with an internal LED and a window over the print area. This Acroprint time recorder informs users of the time and date with a large, bold display.No resetting needed.The LCD backlight digital time punching machine synchronizes automatically with time codes transmitted by the National Institute of Standards and Technology, keeping it incredibly accurate. The internal battery backup keeps the clock on time, even during power outages.Flexible options.With over 150 possible print configurations and 13 preset messages in your choice of four languages, the ES700 easily supports a wide variety of time & attendance and document control applications. This time stamp accomodates virtually any time card, document or form, offering adjustable print font size, your choice of automatic, semi-automatic or manual print operation, and left or right hand print. The power supply is switchable from 120V to 240V.Easy to use.Cards and documents are a snap to align correctly, thanks to a handy window in the cover and a bright internal LED illuminating the document print area.
|
|
|
|