Welcome, Guest |
You have to register before you can post on our site.
|
Forum Statistics |
» Members: 466
» Latest member: Charvab
» Forum threads: 1,441
» Forum posts: 2,615
Full Statistics
|
Online Users |
There are currently 13 online users. » 0 Member(s) | 11 Guest(s) Bing, Google
|
Latest Threads |
Bedava Free Fire Hesap
Forum: My Forum
Last Post: Tanitim2025
01-01-2023, 01:02 PM
» Replies: 0
» Views: 0
|
Bedava Pubg Mobile Hesap
Forum: My Forum
Last Post: Tanitim2025
01-01-2023, 12:49 PM
» Replies: 0
» Views: 0
|
Bedava Hesaplar
Forum: My Forum
Last Post: Tanitim2025
10-20-2022, 07:51 AM
» Replies: 0
» Views: 0
|
Film izle
Forum: My Forum
Last Post: Tanitim2025
08-27-2022, 05:16 AM
» Replies: 0
» Views: 0
|
Ehliyet Sınav Soruları
Forum: My Forum
Last Post: Tanitim2025
08-14-2022, 03:13 PM
» Replies: 0
» Views: 0
|
Seo Hizmetleri
Forum: My Forum
Last Post: Tanitim2025
05-22-2022, 02:08 PM
» Replies: 0
» Views: 0
|
شراء عقار في تركيا
Forum: My Forum
Last Post: Tanitim2025
04-30-2022, 11:57 AM
» Replies: 0
» Views: 0
|
Propriété à vendre à Turq...
Forum: My Forum
Last Post: Tanitim2025
04-27-2022, 10:50 AM
» Replies: 0
» Views: 0
|
Apple benefits elma yemen...
Forum: My Forum
Last Post: Tanitim2025
04-16-2022, 10:23 PM
» Replies: 0
» Views: 0
|
CLOUD TÜRKIYE Bulutların ...
Forum: My Forum
Last Post: Tanitim2025
04-13-2022, 04:05 PM
» Replies: 0
» Views: 0
|
|
|
What Is the Difference Between API and Pharmaceutical Intermediates? |
Posted by: hereuice - 10-13-2021, 05:27 AM - Forum: My Forum
- No Replies
|
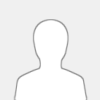 |
What Is the Difference Between API and Pharmaceutical Intermediates?
What is the difference between API and pharmaceutical intermediates? The main difference between the two is that the API is an active product that has completed the synthesis route, and the intermediate is a product in a certain place in the synthesis route.
Difference between API and pharmaceutical intermediates — detailed explanation
Both active pharmaceutical ingredients and intermediates belong to the category of fine chemicals. Intermediates are something that is produced in the manufacturing of API and requires further molecular changes to become APIs. Intermediates can be separated or not separated.
The active pharmaceutical ingredient is used for making medicine and it can be any substance or mixture of substances. When this ingredient is used in medicine, it becomes an active ingredient which plays pharmacological activity or other direct effects in the diagnosis, treatment, symptom relief, or prevention of diseases. The APIs can be directly formulated, while intermediates can only be used to synthesize the next product. Only through intermediates can APIs be produced.
It can be seen from the definition that the intermediate pharmaceutical products are the key products of the previous process of making APIs, which are also different in structure from APIs. In addition, the pharmacopeia has testing methods for APIs, but no for intermediates. Active pharmaceutical ingredients and intermediates are both important in the modern pharmaceutical industry.
Custom synthesis of intermediates
We have known the difference between the API and pharmaceutical intermediates series, and now it’s time to know how APIs are produced. This production process usually includes custom synthesis services. We will elaborate on the synthesis of intermediates to uncovers this production process.
Custom synthesis of intermediate pharmaceutical products is divided into 3 levels according to the closeness of cooperation with customers:
(1)Participating in the development stage of the customer’s new project, which requires the company hired to be highly innovative;
(2)Setting up the process route of large-scale production. This requires the company’s engineering amplification capabilities of the product and the ability to continuously improve the process of customized products in the later stage to meet the needs of large-scale production. Continuously reduce production costs and improve product competitiveness;
(3) Process improvement of the products in the mass production stage of customers, so as to meet the quality standards of foreign companies.
Molcreator is a chemical synthesis lab which can design synthetic routes for customers’ target molecules, and complete the synthesis and delivery of compounds in time with high quality ensured. These compounds include reference compounds, metabolites, reagents, intermediates, molecular fragments and impurities, etc.
Fine Chemicals, Intermediates and Excipient
The basic principle for definition of the term. Fine Chemicals is a three-tier segmentation of the universe of chemicals into commodities, fine chemicals, and specialty chemicals
Fine chemicals are complex, single, pure chemical substances. They are produced in limited quantities (<1000 metric tons per year) in multipurpose plants by multistep batch chemical or biotech(nological) processes.
Pharmaceutical intermediates are chemical compounds which form the building blocks of the active pharmaceutical ingredient (API).
Pharmaceutical intermediates are produced as a by-product during the production of API. Every reaction in the production process of API gives rise to various different pharmaceutical intermediates. Pharmaceutical intermediates are used in the production of bulk drugs and also for research and development purpose by various pharma and biopharma companies.
The pharmaceutical industry is ever thirsty to satisfy patient’s therapeutically needs and apart from active ingredients, inactive excipients play a major role in formulation development. Pharmaceutical excipients are substances other than the pharmacologically active drug or prodrug which are included in the manufacturing process or are contained in a finished
pharmaceutical product dosage form.
|
|
|
Accelerating growth in auto parts e-commerce |
Posted by: hereuice - 10-13-2021, 05:25 AM - Forum: My Forum
- No Replies
|
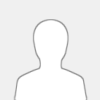 |
Accelerating growth in auto parts e-commerce
The UK automotive parts supply chain has been transformed by the emergence of e-commerce and the changing behaviour of car owners. Online parts sales are growing at a rate of around 10.5% a year (CAGR) compared with 3% for the whole UK aftermarket and, according to the Society of Motor Manufacturers and Traders (SMMT), online parts and accessories sales will be worth around £1.65 billion by 2022. These figures suggest manufacturers need to get into the e-commerce mindset and meet consumer expectations to avoid losing out on a sizeable revenue stream.
In 2016, Amazon launched an automotive research site that allows users to access aftermarket parts for specific makes and models. Though Amazon had been selling auto parts for ten years up to that point, the new site – geared towards purchasers’ individual requests – has proven automotive e-commerce to be just as viable as any other kind of e-commerce. Similarly, eBay.co.uk, visited by one in three British people every month, is emerging as a growing marketplace for automotive parts, such as JAC auto parts and JAC spare parts.
This online marketplace is focused on two primary customers: those seeking accessories for upgrades and those interested in purchasing older model parts. The average UK car is now approximately eight years old, up from just over six years old in 2003, according to the SMMT. Most of these owners are now choosing to buy chery spare parts or chery auto parts online because of the lower prices and convenience that e-commerce provides. Meanwhile, owners of newer vehicles are mainly interested in online shopping experiences that allow them to accessorise their vehicles.
Yet, despite the significant rise in the sector’s popularity, automotive manufacturers have yet to register a considerable rise in their bottom lines. According to PwC, figures from the US – a larger market but a yardstick for the UK – show that its top ten automotive manufacturers have only seen a 4% return on capital, compared with the average of 8-9% earned by manufacturers in other industries.
One way to improve these figures and take advantage of the rising popularity of the e-commerce automotive aftermarket sector would be to focus on the role that packaging plays in supply chain efficiency.
Far too often, packaging is viewed as a commodity, but in fact it is a critical component of manufacturers’ supply chains, as it determines how much space is needed in warehouses, how much damage products will experience during shipment and, as a result of e-commerce, how valued customers feel when they open the box in which the auto part was delivered. The value of packaging – and its impact on manufacturers’ marketability and supply chain efficiency – must not be overlooked.
Typically, package delivery costs consist of: freight (60%); labour (20%); packaging materials such as corrugated cardboard and dunnage (15%); and damage (5%). Companies tend to focus only on reducing packaging material costs, even though they could achieve more significant savings by concentrating on the other 85% of costs. To do this, manufacturer stakeholders should conduct a value analysis to determine the true financial and supply chain efficiency savings that can be generated if each type of cost is reduced.
To ensure automotive manufacturers find the right balance between packaging speed and protection, a four-pillar approach to packages should be considered: minimising damage; maximising packaging productivity; right-sizing boxes; and ensuring that unboxing is easy and pleasing. By implementing lean principles into packaging operations, these pillars can increase manufacturer productivity by up to 30%. This uptick in productivity can lead to a trickle-down effect, as manufacturers will typically require 15-20% less labour per package, figures that will directly influence their bottom lines.
As freight costs continue to rise because of limited trucking capacity, mainly resulting from driver shortages, manufacturers must ensure that all packages feature more products than air (box cube minus product cube) before they enter pallets or trucks. After all, only 65% of trucks and pallets – if filled with manufacturers’ packages – are utilised, as 35% of each box is composed of unfilled space.
To improve that figure and increase profits in the e-commerce era, a partnership with a packaging solutions provider that is focused on manufacturers’ unique needs and will test packages until correct sizes are determined is more important now than ever before.
|
|
|
Overview of CNC Machining Process |
Posted by: hereuice - 10-13-2021, 05:24 AM - Forum: My Forum
- No Replies
|
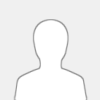 |
Overview of CNC Machining Process
Evolving from the numerical control (NC) machining process which utilized punched tape cards, CNC machiningis a manufacturing process which utilizes computerized controls to operate and manipulate machine and cutting tools to shape stock material—e.g., metal, plastic, wood, foam, composite, etc.—into custom parts and designs. While the CNC machining process offers various capabilities and operations, the fundamental principles of the process remain largely the same throughout all of them. The basic CNC machining process includes the following stages:
Designing the CAD model
Converting the CAD file to a CNC program
Preparing the CNC machine
Executing the machining operation
CAD Model Design
The CNC machining process begins with the creation of a 2D vector or 3D solid part CAD design either in-house or by a CAD/CAM design service company. Computer-aided design (CAD) software allows designers and manufacturers to produce a model or rendering of their parts and products along with the necessary technical specifications, such as dimensions and geometries, for producing the part or product.
Designs for CNC machined parts are restricted by the capabilities (or inabilities) of the CNC machine and tooling. For example, most custom CNC machine parts tooling is cylindrical therefore the part geometries possible via the CNC machining process are limited as the tooling creates curved corner sections. Additionally, the properties of the material being machined, tooling design, and workholding capabilities of the machine further restrict the design possibilities, such as the minimum part thicknesses, maximum part size, and inclusion and complexity of internal cavities and features.
Once the CAD design is completed, the designer exports it to a CNC-compatible file format, such as STEP or IGES.
CNC Machining Tolerances Tables
When specifying parts to a machine shop, it's important to include any necessary tolerances. Though CNC machines are very accurate, they still leave some slight variation between duplicates of the same part, generally around + or - .005 in (.127 mm), which is roughly twice the width of a human hair. To save on costs, buyers should only specify tolerances in areas of the part that will need to be especially accurate because they will come into contact with other parts. While there are standard tolerances for different levels of machining (as shown in the tables below), not all tolerances are equal.
CAD File Conversion
The formatted CAD design file runs through a program, typically computer-aided manufacturing (CAM) software, to extract the part geometry and generates the digital programming code which will control the CNC machine and manipulate the tooling to produce the custom-designed part.
CNC machines used several programming languages, including G-code and M-code. The most well-known of the CNC programming languages, general or geometric code, referred to as G-code, controls when, where, and how the machine tools move—e.g., when to turn on or off, how fast to travel to a particular location, what paths to take, etc.—across the workpiece. Miscellaneous function code, referred to as M-code, controls the auxiliary functions of the machine, such as automating the removal and replacement of the machine cover at the start and end of production, respectively.
Once the CNC program is generated, the operator loads it to the CNC machine.
Machine Setup
Before the operator runs the CNC program, they must prepare the CNC machine for operation. These preparations include affixing the workpiece directly into the machine, onto machinery spindles, or into machine vises or similar workholding devices, and attaching the required tooling, such as drill bits and end mills, to the proper machine components.
Once the machine is fully set up, the operator can run the CNC program.
Machining Operation Execution
The CNC program acts as instructions for the CNC machine; it submits machine commands dictating the tooling’s actions and movements to the machine’s integrated computer, which operates and manipulates the machine tooling. Initiating the program prompts the CNC machine to begin the CNC machining process, and the program guides the machine throughout the process as it executes the necessary machine operations to produce a custom-designed part or product.
CNC machining processes can be performed in-house—if the company invests in obtaining and maintaining their own CNC equipment—or out-sourced to dedicated CNC machining service providers.
Types of CNC Machining Operations
CNC machining is a manufacturing process suitable for a wide variety of industries, including automotive, aerospace, construction, and agriculture, and able to produce a range of products, such as automobile frames, surgical equipment, airplane engines, gears, and hand and garden tools. The process encompasses several different computer-controlled machining operations—including mechanical, chemical, electrical, and thermal processes—which remove the necessary material from the workpiece to produce a custom-designed part or product. While chemical, electrical, and thermal machining processes are covered in a later section, this section explores some of the most common mechanical CNC machining operations including:
Drilling
Milling
Turning
CNC Drilling
Drilling is a machining process which employs multi-point drill bits to produce cylindrical holes in the workpiece. In CNC drilling, typically the CNC machine feeds the rotating drill bit perpendicularly to the plane of the workpiece’s surface, which produces vertically-aligned holes with diameters equal to the diameter of the drill bit employed for the drilling operation. However, angular drilling operations can also be performed through the use of specialized machine configurations and workholding devices. Operational capabilities of the drilling process include counterboring, countersinking, reaming, and tapping.
CNC Milling
Milling is a machining process which employs rotating multi-point cutting tools to remove material from the workpiece. In CNC milling, the CNC machine typically feeds the workpiece to the cutting tool in the same direction as the cutting tool’s rotation, whereas in manual milling the machine feeds the workpiece in the opposite direction to the cutting tool’s rotation. Operational capabilities of the milling process include face milling—cutting shallow, flat surfaces and flat-bottomed cavities into the workpiece—and peripheral milling—cutting deep cavities, such as slots and threads, into the workpiece.
CNC Turning
Turning is a machining process which employs single-point cutting tools to remove material from the rotating workpiece. In CNC turning, the machine—typically a CNC lathe machine—feeds the cutting tool in a linear motion along the surface of the rotating workpiece, removing material around the circumference until the desired diameter is achieved, to produce cylindrical parts with external and internal features, such as slots, tapers, and threads. Operational capabilities of the turning process include boring, facing, grooving, and thread cutting. When it comes down to a CNC mill vs. lathe, milling, with its rotating cutting tools, works better for more complex parts. However, lathes, with rotating workpieces and stationary cutting tools, work best for faster, more accurate creation of round parts.
CNC Metal Spinning
Close cousins to lathes, CNC spinning lathe machines involve a lathe set with a blank (a metal sheet or tube) that rotates at high speeds while a metal spinning roller shapes the workpiece into a desired shape. As a “cold” process, CNC metal spinning forms pre-formed metal—the friction of the spinning lathe contacting the roller creates the force necessary to shape the part.
How Does a Swiss Machine Work?
Swiss machining, also known as swiss screw machining, uses a specialized type of lathe that allows the workpiece to move back and forth as well as rotate, to enable closer tolerances and better stability while cutting. Workpieces are cut right next to the bushing holding them instead of farther away. This allows for less stress on the part being made. Swiss machining is best for small parts in large quantities, like watch screws, as well as for applications with critical straightness or concentricity tolerances. You can find out more about this topic in our guide on how swiss screw machines work.
How Does a 5 Axis CNC Machine Work?
5 axis CNC machining describes a numerically-controlled computerized manufacturing system that adds to the traditional machine tool’s 3-axis linear motions (X, Y, Z) two rotational axes to provide the machine tool access to five out of six part sides in a single operation. By adding a tilting, rotating work holding fixture (or trunnion) to the work table, the mill becomes what is called a 3+2, or an indexed or positional, machine, enabling the milling cutter to approach five out of six sides of a prismatic workpiece at 90° without an operator having to reset the workpiece.
It is not quite a 5-axis mill, however, because the fourth and fifth axes do not move during machining operations. Adding servomotors to the additional axes, plus the computerized control for them – the CNC part –would make it one. Such a machine- which is capable of full simultaneous contouring- is sometimes called a “continuous” or “simultaneous” 5-axis CNC mill. The two additional axes can also be incorporated at the machining head, or split – one axis on the table and one on the head.
CNC Lathe Operator Training
To handle a CNC lathe, a machinist should have completed a set amount of coursework and earned appropriate certification from an accredited industrial training organization. CNC turning machining training programs will usually involve multiple classes or sessions, offering a gradual instruction process broken up into several steps. The importance of adhering to safety protocols is reinforced throughout the training process.
Beginning CNC lathe classes might not include hands-on experience, but they may include familiarizing students with the command codes, translating CAD files, tool selection, cutting sequences, and other areas. A beginner CNC lathe course may include:
Lubrication and scheduling lathe maintenance
Translating instructions into a machine-readable format and loading them into the lathe
Establishing criteria for tool selection
Installing tools and parts for handling the material
Producing sample parts, like die-casting parts
Later CNC lathe training typically involves actual lathe operation, as well as machine adjustments, program editing, and the development of new command syntax. This type of lathe machine training can include courses on:
Figuring out where edits are needed from comparing sample parts to their specifications
CNC programming edits
Creating multiple cycles of test components to refine the results of edits
Regulating coolant flow, cleaning the lathe, and repair and replacement of tools
CNC Machining Equipment and Components
As indicated above, there is a wide range of machining operations available. Depending on the machining operation being performed, the CNC machining process employs a variety of software applications, machines, and machine tools to produce the desired shape or design.
Types of CNC Machining Support Software
The CNC machining process employs software applications to ensure the optimization, precision, and accuracy of the custom-designed part or product. Software applications used include:
CAD
CAM
CAE
CAD: Computer-aided design (CAD) software are programs used to draft and produce 2D vector or 3D solid part and surface renderings, as well as the necessary technical documentation and specifications associated with the part. The designs and models generated in a CAD program are typically used by a CAM program to create the necessary machine program to produce the part via a CNC machining method. CAD software can also be used to determine and define optimal part properties, evaluate and verify part designs, simulate products without a prototype, and provide design data to manufacturers and job shops.
CAM: Computer-aided manufacturing (CAM) software are programs used extract the technical information from the CAD model and generate machine program necessary to run the CNC machine and manipulate the tooling to produce the custom-designed part, such as stamping parts, custom plastic parts, etc. CAM software enables the CNC machine to run without operator assistance and can help automate finished product evaluation.
CAE: Computer-aided engineering (CAE) software are programs used by engineers during the pre-processing, analysis, and post-processing phases of the development process. CAE software is used as assistive support tools in engineering analysis applications, such as design, simulation, planning, manufacturing, diagnosis, and repair, to help with evaluating and modifying product design. Types of CAE software available include finite element analysis (FEA), computational fluid dynamics (CFD), and multibody dynamics (MDB) software.
Some software applications have combined all of the aspects of CAD, CAM, and CAE software. This integrated program, typically referred to as CAD/CAM/CAE software, allows a single software program to manage the entire fabrication process from design to analysis to production.
What is a CNC Machine? Types of CNC Machines and custom CNC precision machining parts
Depending on the machining operation being performed, the CNC machining process employs a variety of CNC machines and machine tools to produce the custom-designed part or product. While the equipment may vary in other ways from operation to operation and application to application, the integration of computer numerical control components and software (as outlined above) remains consistent across all CNC machining equipment and processes.
CNC Drilling Equipment
Drilling employs rotating drill bits to produce the cylindrical holes in the workpiece. The design of the drill bit allows for the waste metal—i.e., chips—to fall away from the workpiece. There are several types of drill bits, each of which is used for a specific application. Types of drill bits available include spotting drills (for producing shallow or pilot holes), peck drills (for reducing the amount of chips on the workpiece), screw machine drills (for producing holes without a pilot hole), and chucking reamers (for enlarging previously produced holes).
Typically the CNC drilling process also utilizes CNC-enabled drill presses, which are specifically designed to perform the drilling operation. However, the operation can also be performed by turning, tapping, or milling machines.
CNC Milling Equipment
Milling employs rotating multi-point cutting tools to shape the workpiece. Milling tools are either horizontally or vertically oriented and include end mills, helical mills, and chamfer mills.
The CNC milling process also utilizes CNC-enabled milling machinery, referred to as mill machines or mills, which can be horizontally or vertically oriented. Basic mills are capable of three-axis movements, with more advanced models accommodating additional axes. The types of mills available include hand milling, plain milling, universal milling, and omniversal milling machines.
CNC Turning Equipment
Turning employs single-point cutting tools to remove material from the rotating workpiece. The design of the turning tool varies based on the particular application, with tools available for roughing, finishing, facing, threading, forming, undercutting, parting, and grooving applications.
The CNC turning process also utilizes CNC-enabled lathes or turning machines. The types of lathes available include turret lathes, engine lathes, and special-purpose lathes.
What is a Desktop CNC Machine?
Companies that specialize in manufacturing CNC machines often offer a desktop series of smaller, lightweight machines. Desktop CNC machines, although slower and less precise, handle soft materials well, such as plastic and foam. They’re also better for smaller parts and light to moderate production. Machines featured in a tabletop series resemble the larger industry standard, but their size and weight make them better suited to small applications. A desktop CNC lathe, for example, that features two axes and can handle parts up to six inches in diameter, would be useful for jewelry and mold-making. Other common desk CNC machines include plotter-sized laser cutters and milling machines.
With smaller lathes, it’s important to differentiate between a benchtop CNC lathe machine and a desktop lathe. Benchtop CNC lathes are generally more affordable, but also smaller and somewhat limited in the applications they can handle. A standard CNC benchtop lathe generally includes the motion controller, cables, and basic software. A standard CNC desktop lathe, with a similar basic package, costs slightly more.
|
|
|
Everything you need to know about Gas Solenoid Valves |
Posted by: hereuice - 10-13-2021, 05:20 AM - Forum: My Forum
- No Replies
|
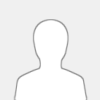 |
Everything you need to know about Gas Solenoid Valves
Gas Solenoid Valves are as versatile as they are useful. Translating electrical impulses, to open and close the valve, they control the flow of gas in a wide range of industrial and residential applications. In this tutorial article, PIF takes a closer look at what Gas Solenoid Valves do, what applications they're used for, and the key manufacturers of these handy types of solenoid valve.
What are Gas Solenoid Valves?
Gas Solenoid Valves are made of parts that receive electrical impulses that then translate those impulses into mechanical movements. When an electrical impulse is received, by the Gas Solenoid Valve, it will open or close the valve. Thus controlling the flow of gas into a chamber or through a line.
Applications for Gas Solenoid Valves
A gas solenoid valve can be used in many applications. Both for commercial and residential devices. Commercial uses of Gas Solenoid Valves with pressure switch generally include any pneumatic machinery that uses gas pressure to move its parts. Manufacturing facilities might use solenoid valves to control the movement of gases used in their manufacturing processes.
Residential applications include solenoid valves used inside furnaces. These control when the gas comes on and is ignited by the pilot light to create warmth. Vehicles powered by natural gas use solenoid valves to control the flow of gas into the engine’s cylinders. While gas-powered clothes dryers also have solenoid valves to control the flow of gas into the dryer, which helps to prevent fires or gas poisoning.
Key Manufacturers of Gas Solenoid Valves
ASCO provides the broadest line of solenoid & motorised shutoff valves designed to control the flow of fuel gas, liquid propane and all grades of fuel oil used in combustion applications such as: industrial furnaces, ovens, kilns, incinerators, burners and boilers. Solenoid operated valves handling combustion system pilot and main line fuel shutoff and control needs. These valves are available in 2-way normally closed, normally open, manual reset, and 3-way diversion.
Bürkert also produce solenoid valves with gas filter for fluid and gaseous media, aggressive or neutral, applicable in various ranges of temperature and pressure. In fact, Christian Bürkert, founder of Bürkert is said to have pioneered the ‘solenoid valve’ as we know it today, setting the international benchmark for industrial solenoid valves.
Buschjost (an IMI Norgren brand) manufactures a wide range of Solenoid Valves for use with different pressures, media’s, temperatures and applications. The Buschjost range of Solenoid Valves include direct-acting solenoid valves, indirect-acting solenoid valves, or a combination of both; solenoid valves with forced lifting.
Gas Solenoid Valve Materials
ASCO valves are available in brass, aluminium, and stainless steel. Their main features include junction box; pipe taps; visual indication; proof of closure; leading agency approvals; and pipe connections from 1/8” to 3”. Most valves are rated for -40oF service for outdoor installation in frigid climates.
Bürkert’s range of gas solenoid valves are available in an extensive range of body and seal materials. From PTFE, to NBR, EPDM and even PEEK, this tutorial article on solenoid valve materials by Solenoid Valve expert Michael Hannig will tell you all you need to know.
Useful Solenoid Valve Resources
This chemical resistance chart and solenoid valve selection guide from Bürkert is an extremely useful resource when specifying or choosing the correct solenoid valve for an application. There is also pressure regulate valve.
Solenoid Valve material selection chart
This white paper from ASCO covers breakthrough solenoid valve technology in oil and gas applications.
Breakthrough solenoid valve technology for oil and gas applications
Finally, this technical tips video from Norgren Buschjost explain exactly how solenoid valves work in process applications, the different types of solenoid valves available and typical applications.
|
|
|
Exactly How The Paper Pulp Molding Machine Works |
Posted by: wj26wj - 10-13-2021, 05:19 AM - Forum: My Forum
- No Replies
|
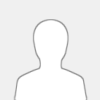 |
The paper pulp molding machine is responsible for creating molded pulp, which has become an ideal material when it comes to packaging. In the past years, the molded-pulp was typically used simply to produce cartons and egg trays. However, the adaptability and sustainability of such processes has resulted in many different industries choosing these methods over packaging materials that are environmentally-harmful for example plastic. The paper pulp molding machine has additionally grown in popularity mainly because these particular materials are recyclable. We are the best one of pulp molding machine suppliers.
Introduction To The Pulp Molding Machines
The makers of molded-pulp typically take into account the fibers (materials) how the want to use in the pulp-molding machines. Materials like paper are simple to transform in to a pulp in addition to being easy enough when it comes to shaping.
The manner in which these pulp-molding machines jobs are to first mix the materials with water. The presser on these pulp molding machines typically features built in blenders that perform task of turning this mixture into pulp. This mixture will then be typically transferred in a paper “egg-tray” making machine that includes a built-in mold. This is the process that the material is exposed to a set temperature. Following the mold has become heated it would move through the dryer as well as the vacuum. This just about sums up basic functionalities of the pulp molding machine. The working principle is similar to the egg tray machine.
The advanced designs of today are able to improve end-products further when it comes to making the item denser and providing it with specific shapes which is suitable when it comes to many different purposes. As an example, once a basic form of pulp-molded package is generated it will typically undergo subsequent processes referred to as “after pressing.” This procedure involves providing these packages using their final and further improved shape. These capabilities are what highlight the flexibility from the pulp-molding technology.
In addition, it really is worthwhile to keep in mind that the paper pulp molding machine can be utilized for a variety of other purposes over and above packaging. For example, these machines are able to produce items such as bowls, plates and utensils, together with cushioning and protection for other packaged items. Today a variety of other containers are invented and looked at due to the versatility of molded pulp when it comes to its many applications.
The Benefits Of Making Use Of The Paper Pulp Molding Machine
While it can be an evident fact that the molded pulp is actually one of the more favorable environmentally-friendly materials currently available, using these materials in addition to a reliance on pulp-molding machines is additionally fantastic for your packaging industries because of the fact that materials including paper that are used with regards to pulp molding are incredibly affordable.
Moreover, the exact operations of these pulp-molding machines have the ability to save manufacturers a great deal of their time and money across the long-run. It is because virtually all these pulp-molding machines which can be sold today have already been created in such as way in which they necessitate minimal maintenance as well as leaning towards more energy savings. In addition, this equipment is already famous for high efficiency and also the decrease of the necessity for manual labor. It is not surprising these appliances are already praised as the way forward for packaging materials across the world. We have good quality of apple tray machine for sale.
The greater number of that consumers buy their goods which has been packaged inside the pulp-mold packages, the greater we can save our trees and the less landfills will be created. This packaging also decreases the CO2 amounts which get released in to the atmosphere that significantly reduces “producers” contribution towards climatic change.
What is EPE Foam?
EPE foam, or Expanded Polyethylene foam, processed by EPE bonding and butting machine, is one of the most widely used plastics in production. What is polyethylene foam? It is a thermoplastic resin, which means that it can be melted by heating and cooled to form different shapes and objects.
What Are The Physical and Chemical Properties of EPE?
The physical and chemical properties of EPE foam are what give it its desirable characteristics. It is due to these properties that this plastic has avariety of applications in different industries such as EPE foam padding, EPE foam tube, and EPE foam sheet. There is also Ps foam machine to process.
Physical Properties of EPE Foam
EPE foam is a harmless plastic and has no taste or odour.
It is a very popular material for packaging goods as it is light in weight and flexible. It has the ability to absorb shock and provide good cushioning to delicate objects.
EPE has a high weight to strength ratio and high thermal resistance. It can be heated and melted multiple times, and reshaped into other new objects due to the high EPE foam temperature range.
EPE foam is resistant to water, oils, and many chemicals. It is also a very good insulating material. EPE is available in different densities, according to its application or purpose.
Chemical Properties of EPE Foam
The chemical makeup of expanded polyethylene is similar to most plastics, and of the form (C₂H₄)nH₂. EPE is usually white in colour unless a dye or other colour pigment is added to it during the melting process.
EPE foam is also referred to as bead board in the plastic industry. It is a closed cell foam, which allows it to take up more volume and be light weight.
|
|
|
What Is Red Yeast Rice Extract? |
Posted by: wj26wj - 10-13-2021, 05:16 AM - Forum: My Forum
- No Replies
|
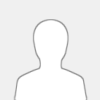 |
Red yeast rice extract (RYRE) is a traditional Chinese medicine that has been purported to lower cholesterol. Several types of the extract are sold as supplements.
Red yeast rice may be appealing because it's "natural," but you need to be careful. Experts have not studied it extensively. The ideal dosing and its long-term safety are unclear. It could be dangerous for some people. And because the ingredients of different brands of red yeast rice extract might vary so much, it's hard to make firm statements about its effectiveness or safety.
What Is Red Yeast Rice Extract?
RYRE is a substance that's extracted from rice that's been fermented with a type of yeast called Monascus purpureus. It's been used in China and other Asian countries for centuries as a traditional medicine. It's also used as a food coloring, additive, and preservative.
RYRE naturally contains several ingredients that may help control cholesterol levels. These include a number of monacolins, most importantly monacolin K. It also contains sterols, isoflavones, and monounsaturated fatty acids, or "healthy fats."
Is Red Yeast Rice Extract a Drug or a Supplement?
Confusingly, the answer is both. One of the most important ingredients in RYRE is monacolin K. It's also known as lovastatin, the active ingredient in the prescription drug Mevacor.
So on one hand, the extract is a traditional remedy that helps lower cholesterol. On the other, the pharmaceutical manufacturer of Mevacor argues that it owns the rights to the ingredient lovastatin.
This confusion extends to how the supplement is sold in the U.S. Because red yeast rice extract contains a substance classified as a prescription drug, the FDA has requested that several RYRE products be withdrawn from the market because they contained monacolin K. The FDA cited a risk of severe muscle problems that could lead to kidney disease.
Despite the FDA's attempts, many people in the U.S. still manage to get similar red yeast rice extracts from other countries or on the Internet.
How Well Does Red Yeast Rice Lower Cholesterol?
Studies have shown that certain red yeast rice products that contain statin can significantly lower levels of total cholesterol and specifically LDL, or "bad" cholesterol. One showed that taking 2.4 grams per day reduced LDL levels by 22% and total cholesterol by 16% in 12 weeks. Another study showed that taking 1.2 grams per day lowered LDL levels by 26% in just eight weeks.
However, the results of these studies depend on the amount of statin that is in the extract, and it can vary widely. The FDA considers extracts that contain statins to be illegal in the U.S., but many are still available.
What Is the Correct Dosage of Red Yeast Rice Extract?
Keep in mind that the amount of monacolin -- perhaps the most important ingredient -- in a organic red yeast rice extract can vary a lot. There are many different strains of the yeast. Different types of fermentation are used. One study of different brands of red yeast rice supplements showed that the amount of monacolin ranged from 0% to 0.58%.
So even though studies have shown that RYRE can lower cholesterol, you can't really know if the supplement brand you're using will have that effect.
What Are the Risks of Red Yeast Rice?
Studies have shown that side effects are mild, like headaches, heartburn, and upset stomach. Side effects from prescription lovastatin include elevation of liver enzymes and muscle enzymes, muscle problems, and liver problems.
But more research needs to be done before we can know about the long-term safety of red yeast rice extract. We do know that some types may be more dangerous than others because of high levels of other substances such as citrinic acid.
RYRE also shares some of the same risks as statins, the class of drugs containing lovastatin. Experts say that the risks of lovastatin would logically apply to RYRE -- elevation of liver and muscle enzymes, muscle problems, and liver problems.
The extract may not be safe for everyone. You should not take it if you:
Have kidney disease
Have liver disease
Are pregnant
Are breastfeeding
In addition, anyone taking one of the following medicines should not use red yeast rice:
Statins to control cholesterol such as lovastatin (Mevacor), rosuvastatin (Crestor), fluvastatin (Lescol), atorvastatin (Lipitor), pravastatin (Pravachol), and simvastatin (Zocor)
Other cholesterol drugs such as gemfibrozil (Lopid) and fenofibrate (TriCor)
Drugs to suppress the immune system, like cyclosporine
Antifungal drugs such as fluconazole (Diflucan), ketoconazole (Nizoral), and itraconazole (Sporanox)
The antibiotics erythromycin and clarithromycin (Biaxin)
Serzone, an antidepressant
Protease inhibitors, used to treat HIV
People who have allergies to fungus or yeast should also be wary of using RYRE.
The extract may also interact with other drugs for blood pressure and thyroid problems and interact with other herbs and supplements you may be taking.
Whatever the state of your health, always talk to your doctor before you start using red yeast rice or any other supplement. Remember that not all brands are equal, and that RYRE isn't safe for everyone. Though red yeast rice extract looks like a promising treatment, more research needs to be done. For now, you should be cautious.
|
|
|
7 Spare Tractor Parts You Need to Have Handy for Preventative Maintenance |
Posted by: wj26wj - 10-13-2021, 05:13 AM - Forum: My Forum
- No Replies
|
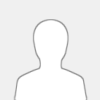 |
Preventative maintenance is an important part of owning a tractor. If you want that machine to run as strong as the day you bought it for as long as possible, you have to be dedicated to maintenance every day and at every service milestone.
Things tend to break down just when you need them most. You might be gearing up for planting or getting ready to harvest when you find an issue that requires repair of your tractor. Whether you catch it during routine maintenance or out in the field, you need a fix and you need it fast.
Replacement Parts for Routine Tractor Repair
There’s a long list of issues that can sideline your tractor. If you’re ready with the right parts, you can make the necessary repairs or replacements to get back to farming with little delay. Stock up on the MTZ tractor parts listed in your operator’s manual so you have backup in case something goes wrong.
1. Filters
Tractors do the dirty work. So, naturally, they get dirty. A variety of filters help protect critical components from the dirt, debris, and dust they kick up during a day’s work. You’ll need an extra oil filter, air filter, hydraulic filter, and fuel filter to change out old, dirty ones.
John Deere makes it easy, providing all four filters your compact tractor needs in one convenient package. Since you need to check and change your fuel and engine oil more frequently, you may want to have several additional filters on hand.
2. Oil and Fuel
Despite the best efforts of the filters, oil still gets dirty and can easily gunk up your tractor or cause it to stall out. Engine oil and hydraulic oil are needed for regular maintenance items, so it’s important to have plenty around.
On some sub-compact tractors, the hydraulic filter is low to the ground and subject to damage from rough terrain. If a stick or something else breaks your filter, you can lose hydraulic oil quickly, so it’s important to have extra gallons available if you run a smaller compact tractor.
Having a full fuel supply might seem obvious but it’s easy to overlook. If you don’t keep an eye on fuel levels, you can waste a lot of time filling up. You also need to ensure your fuel is clean. John Deere diesel fuel conditioner is a fuel additive that improves fuel quality and maintains peak engine efficiency.
3. Fluids and Coolants
Oil and fuel are the most important fluids you need to fill to keep your equipment’s engine running. But there’s a wide variety of other fluids that your tractor needs to run efficiently. Checking the engine coolant, hydraulic fluid, radiator fluid, and transmission fluid — and topping off empty tanks — should be part of your daily preventative maintenance routine.
Clean coolant helps avoid internal damage, rust, or clogs in the engine, which helps prevent much bigger engine troubles. Many new tractors, including parts like T25 tractor parts, have combined systems where hydraulic or transmission fluid is shared between the machine and an attachment. To keep both your tractor and your implements running at full power, you need full tanks of clean fluid.
4. Light Bulbs
It might seem like a minor inconvenience, but burnt bulbs should always be replaced immediately. While you can ignore a slightly dimmer room in your home for weeks, tractor light bulbs are there for safety — yours and those around you.
Take stock of the specific light bulbs you need for your headlamps, taillights, and warning lights. Keep them in your shed, garage, or even in the cab of larger utility tractors, so that you can quickly swap out a burnt bulb and keep the lights on.
5. Replacement Belts
Your tractor has several different belts that keep your engine running and other components moving. Over time, alternator belts, fan belts, and air compressor belts can loosen, crack, or split. The belts for your specific tractor model may not always be in inventory at your local dealer or tractor supply store. Plan ahead for replacement belts, especially as your tractor approaches the 200-hour mark, to keep a quick and easy switch from causing prolonged downtime.
6. Zerk Fittings
Greasing your tractor should be part of your daily maintenance checklist. You need to regularly grease the joints and Zerk fittings on your equipment.
Zerk fittings are all over your machine, and many are exposed to wear and tear. While small, a damaged or missing Zerk fitting can contaminate the grease inside your machine and cause much bigger issues. So keep a lot of spare fittings around so you can easily replace broken ones and keep your tractor in good condition.
7. Fuses
Whether you’re tractor’s big or small, all agricultural equipment is becoming more and more powered by electrical components. And every electrical circuit on your machine is protected by a fuse.
Electrical issues aren’t always expensive fixes. Sometimes, it’s simply a blown fuse. Your tractor’s fuses are color-coded and have the ampere rating clearly marked to ensure proper replacement.
|
|
|
Power Saws & Their Uses |
Posted by: wj26wj - 10-13-2021, 05:10 AM - Forum: My Forum
- No Replies
|
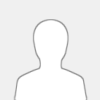 |
Power saws are extremely useful machine tools, but they are also very confusing. There are so many types of saw in different categories and sub-categories of power saw, that it becomes difficult to remember what each kind of saw does. That is the purpose of this article, to act as a sort of “comprehensive guide” to explain the world of various types of power saws.
Generally, there are three varieties of power saws namely power saws with rotating blades, with reciprocating blade and circulating blade, including electric wood cutting saw.
If you have ever played the word game CodyCross then you probably have across the puzzle: Power tool with rotating blade. The answer is BUZZSAW.
But what is a buzzsaw? It is nothing but a circular saw. Most of the electric saws fall under this classification.
In this guide, I’m going to give you a very brief explanation as to what each kind of power saw does, what it is good for, etc. My hope is that this saw guide will be useful for both beginners, who know nothing about power saws and professionals who are familiar with power saws, but who are also looking to expand their knowledge.
Table saws are one of the workhorses of any workshop or garage. Everyone from professionals to home DIYers use this tool often. In my experience, it is hard to think of a woodworking or carpentry job that does not require you to use a table saw at least once. Table saws are very simple, a circular saw blade is spun at high speeds at a stationary position and the operator pushes the wood into the blade. There is some room for customization, especially with regards to the blade, which can be changed to accommodate different kinds of jobs. However, ultimately the table saw is a simple, but effective tool.
Working Principle: The circular table saw blade fixed on an arbor revolves at a very high speed. The work-piece is fed against the rotating blade to make the cut.
Circular saws, much like table saws, are a very common workhorse in both professional and DIY workshops. A circular saw is a versatile tool that offers high portability. The main purpose of a circular saw is to cut wood and other soft materials; in this sense, they are essentially portable table saws. You can also this saw to cut tough materials like metal with the appropriate circular saw blade. The working principle of a circular saw is opposite of a table saw.
How Circular Saw works: A circular saw it a handheld power tool with a rotating blade that is pushed across the workpiece to cut through it. That means the work needs to be stationary and the rotating circular saw blade moves to make the cut.
Jigsaws work similarly to reciprocating saws, except with two key differences. Firstly, unlike with regular reciprocating saws, the blade on a jigsaw aims downward, instead of jutting out from the nose of the saw. Secondly, jigsaws are designed specifically to make curved or otherwise non-straight cuts.
A jigsaw, when compared to a reciprocating saw, is a much more precise tool. Also, it is the only handheld power saw with which you can produce curved cuts.
Uses of Jigsaw:
The jigsaw is a very versatile tool that can be used to cut straight and curved cuts on different materials including wood, plastic, metal, granite, tiles, and metal. One of the most common applications of a jigsaw in a household is to install countertops.
Another advantage of a jig saw is that you can use it to cut internal profiles. All you need to do is drill a start hole for the blade to enter and you are ready to cut straight, angled and curved shapes.
Introduction of Grinding Machines
Grinding machines produce flat, cylindrical, and other surfaces through high-speed rotating abrasive wheels. Grinding is a means of giving a more accurate finish to a part already machined but is also a machining process in its own right. The main types of machine are the ‘surface grinding machine’ for flat surfaces; and the ‘cylindrical grinding machine’ for cylindrical surfaces. More complex shapes are produced by shaped wheels called ‘contour grinding wheels’. ‘Bench’ and ‘pedestal’ grinders are used for tool sharpening, etc.
A grinding machine, often shortened to grinder, is one of the power tools or machine tools used for grinding, it is a type of machining using an abrasive wheel as the cutting tool. Each grain of abrasive on the wheel's surface cuts a small chip from the workpiece via shear deformation.
Grinding is used to finish workpieces that must show high surface quality (e.g., low surface roughness) and high accuracy of shape and dimension. As the accuracy in dimensions in grinding is of the order of 0.000025 mm, in most applications, it tends to be a finishing operation and removes comparatively little metal, about 0.25 to 0.50 mm depth. However, there are some roughing applications in which grinding removes high volumes of metal quite rapidly. Thus, grinding is a diverse field. There are also drill machines.
|
|
|
Why Aluminum Windows |
Posted by: wj26wj - 10-13-2021, 05:07 AM - Forum: My Forum
- No Replies
|
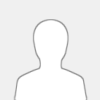 |
Aluminum windows and aluminum doors have become increasingly popular for both commercial and residential buildings. Aluminum window frames can be made to match almost any color and home style. They can also be made in a range of different configurations including casement windows, double-hung windows, sliding windows/doors, awning windows, fixed windows, and lift and slide doors. Here are some reasons why you should choose aluminum.
Durability
Aluminum windows are far less prone to warping; they are weather-proof, corrosion-resistant and immune to the harmful effects of UV rays, ensuring optimal performance with a long lifespan. Their strong window frames will last longer than wood and vinyl frames.
Variety of Color Options
Aluminum windows can be powder coated or anodized in thousands of colors. The only limitation in color is your imagination.
Energy Efficient
Because aluminum, including aluminum awning window, aluminum sliding windows, aluminum casement window, etc., is light, malleable and easy to work with, manufacturers are able to produce window frames that offer high levels of wind, water, and air-tightness, which means exceptional energy efficiency.
Cost efficient
Aluminum windows are far less expensive than wood frames. They do not leak; therefore, they can save a ton of money on energy bills.
Low Maintenance
As opposed to wood, aluminum does not warp or decay. Additionally, paint touchups are not needed. Aluminum is strong enough to bear the load of window lintels with minimal reinforcement. Aluminum windows are virtually maintenance free.
Better Operability
Aluminum is a durable substance and will keep its shape over time. Therefore, aluminum windows and doors will continue to open and slide smoothly over the years.
Noise Proof
Aluminum windows are much better at stopping noise than vinyl windows. Since they are three times heavier and many times stronger than Vinyl. Also, aluminum windows are best when you're opting for the soundless feature due to the fact that they can support heavier glazing than other solutions.
Safety Features
The linkage hardware around the window sash and the handle operating make the window have excellent safety and security. Also, aluminum windows are highly resistant to forced entry and have high-quality multipoint locking mechanisms, which makes it impossible for people to break-in.
Why do you really need an aluminium toilet cabinet?
It is always a difficult thing for people to choose a bathroom cabinet. This is because there are so many styles, designs and functions of cabinets that are available in the market.
Choosing the material for your cabinet too may be a little hard since you want to go for a material that is durable, stable, long-lasting and at the same time will give you what you want.
Aluminium bathroom cabinets are very popular in most modern homes. They are available in various designs, styles and shapes in order to suit any toilet.
The fallacy that aluminium cabinets are very costly does not really hold again these days because there are cheap aluminium cabinets that you can find in the market although the prices of aluminium cabinets may be slightly higher than the other cabinets.
Aluminum toilet cabinets and aluminum kitchen cabinets have various advantages that will entice you into having them as your bathroom cabinets.
Aluminium toilet cabinets are durable
Of all the materials that can be used in making cabinets, aluminium remains the best. You would have realized that your bathroom is always covered with moisture and warmth from the hot air that comes as a result of your shower.
Aluminium is the only material amongst all other materials that can fully withstand both moisture and warmth. It will do this effectively without being affected by it.
Not only that they are durable, but they also have a tough and robust nature when placed in comparison with other materials used in constructing bathroom cabinets.
Aluminium toilet cabinets (or aluminum laundry cabinet) have lasting performance
Do you know that aluminium cabinets can last for a lifetime?
Yes, they can and the reason behind this is their thickness and framework. Thick aluminium cabinets provide better support and they do not bend or become deshaped unlike cabinets made with other materials.
Although some deformities may be noticed with aluminium cabinets. These deformities may be slanting or tilting of the cabinet with time but this will only be noticed with cheap and low-quality aluminium and that is why I advise you to go with high-quality aluminium when you want to buy a cabinet.
Aluminium toilet cabinets have a quality of being waterproof.
One of the major problems that are noticed in bathrooms and toilet is the condensation of water vapour on surfaces and materials in the bathroom.
This condensation will lead to the formation of moisture on these surfaces. Moisture is a very big threat to wood cabinets because it may cause the wood to twist or bend in shape or swell.
When this happens, the area that has become damaged will be unable to support heavy loads and the cabinet becomes eventually useless.
Aluminium cabinets defy this mechanism because they are waterproof. Moisture from the condensation of water vapours or other things in the toilet will not harm them and they will not be susceptible to bending or swelling from any moisture.
|
|
|
Types of Sewing Machines and their Uses |
Posted by: hereuice - 10-13-2021, 05:05 AM - Forum: My Forum
- No Replies
|
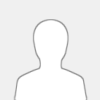 |
Types of Sewing Machines and their Uses
A sewing machine consists of four basic mechanisms: a take-up mechanism, a needle-motion mechanism, a material-feeding mechanism, and a bobbin. Its proper operation requires a delicate balance of these mechanisms. This paper introduces a computer-simulation model that represents these mechanisms and uses the model to predict the kinetic behavior of sewing machines. Based on the simulation. a quantitative understanding of the sewing machine can be achieved that leads to improved sewing-machine design and better sewing-process control. In particular, the balance of thread supply and thread requirement is studied. the thread supply is defined as the amount of thread supplied by the take-up mechanism within one stitch. The thread requirement is defined as the amount of thread required in one stitch and is controlled primarily by the bobbin mechanism. Both properties change instantaneously. From a practical point of view, if the thread requirement were much larger than the thread supply, then there would be skip stitches (when the loop cannot be formed properly) or even thread breakage. On the other hand, if the thread requirement were much less than the thread supply, then there might be poor stitches (with too much thread in the loop) or even needle-jamming. By using the simulation model, the instantaneous balance of the thread supply and the thread requirement is quantitatively studied. It is shown that the balance of thread supply and thread requirement can be changed and optimized by changing the design parameters of the take-up mechanism. The model is validated experimentally by using a Pfaff lockstitch industrial sewing machine.
Industrial sewing machines differ from traditional consumer sewing machines in many ways. An industrial sewing machine is specifically built for long term, professional sewing tasks and is therefore constructed with superior durability, parts, and motors. Whereas traditional sewing machines might include nylon or plastic gears, an industrial sewing machine's gears, connecting rods, housings, and body are typically constructed from high-quality metals, such as cast iron or aluminum. Beyond that, industrial sewing machines are made to handle thick materials such as leather, produce faster stitch rates, and incorporate stouter, more positive feed components than do their consumer equivalents.
With regard to these types of industrial sewing machines, the primary differentiation between them is based on the design of the bed. These four different sewing machine bed styles and their uses are as follows:
Flatbed: The most common type, these machines resemble traditional sewing machines in that the arm and needle extend over the flat base of the machine. Workers typically use this machine for sewing flat pieces of fabric together. Some type of fabric feed mechanism is usually housed in the bed (see below).
Cylinder-bed: These machines feature a narrow, cylindrical bed as opposed to a flat base. This allows the fabric to pass around and under the bed. Workers employ the cylinder-bed machine for sewing cylindrical pieces such as cuffs, but it is also useful for bulky and curved items such as saddles and shoes.
Post-bed: These machines feature bobbins, feed dogs, and/or loopers in a vertical column that rises above the flat base of the machine. The height of this column can vary depending on the machine and its application. Applications that make access to the sewing area difficult, such as attaching emblems, or boot or glove making, utilize the post-bed machine.
Off-the-arm: The least common group, these machines extend a cylindrical bed out from the back of the machine perpendicular to the direction taken by the bed of the cylinder-bed machine. This allows for long runs of tubular goods, such as the inseams of trousers, and is useful for sewing sleeves and shoulder seams.
Other special-purpose sewing machines exist, as well. Portable and fixed electric units are often employed for closing large sacks of agricultural products, dog food, etc. Bookbinders use special machines in their operations. Carpet installers also use special machines for binding carpet. Embroidering and monogramming machines are used for textile customization and decorating and are often program-controlled. Special long arm machines are made for sailmakers and purpose-built machines are available for cobblers.
Sewing Machine Feeds
Different industrial sewing machines offer several ways to feed the material. Typically, industrial mini sewing machines that deliver numerous feed capabilities are more expensive. The main types of feed mechanisms are:
Drop feed: The feed mechanism lies below the machine's sewing surface. This is probably the most common feed type. Toothed segments called feed dogs lift and advance the fabric between each stitch, with the teeth pressing upwards and sandwiching the material against a presser foot.
Needle feed: The needle itself acts as the feed mechanism, which minimizes slippage and allows workers to sew multiple layers of fabric.
Walking foot: The immobile presser foot is replaced with a foot that moves with the feed, which allows easier performance on thick, spongy or cushioned materials.
Puller feed: The machine grips and pulls straight-seamed material as it is sewn and can perform on large, heavy-duty items such as canvas tents.
Manual feed: The feed is controlled entirely by the worker, who can do delicate, personal work such as shoe repair, embroidering, and quilting. On industrial overlock sewing machines, it is sometimes necessary to remove the feed dogs to obtain a manual feed.
The application of an industrial sewing machine is also an important factor to consider. For example, some machines come with an automatic pocket setter, while others include pattern programmability or electronic eyelet buttonholers. Furthermore, the strength and design of the machine needs to complement the type of material being sewn. Higher quality machines will likely be necessary for medium to heavy materials, such as denim, while base level industrial machines may be adequate for lighter materials, such as cotton.
Other Considerations
A particular machine’s available stitch types can vary. There are several dozen distinct types of stitches, each requiring between one and seven threads. Plain, or straight stitches are the most commonly used stitches in industrial sewing and include lock, chain, overlock, and coverstitch. Sailmakers, on the other hand, use zig-zag stitching to better tolerate seam loading between sail panels.
Yet another important feature is the size and speed of the industrial embroidery sewing machine. More expensive machines will be able to sew more stitches per minute. Larger machines provide a larger clearance area under the foot and bigger bed size.
Many industrial machines are sold without motors and can be operated with either clutch motors or servomotors, depending on the user’s needs. Clutch motors run constantly and power to the machine is transmitted by depressing a foot treadle to actuate the clutch. Servomotors run on demand and are speed controllable as well, much as are home sewing machines with sewing machine motor. Both motor types are available for 120 or 240 vac power. Raising of the presser foot is often done with a knee paddle to allow the operator full use of both hands. Although many home machines are able to do a wide variety of operations, production sewing often uses machines that are set up for specific tasks such as bar tacking, buttonhole making, etc. Machines for tailors and seamstresses are likely to be capable of a fuller range of operations.
|
|
|
|