Welcome, Guest |
You have to register before you can post on our site.
|
Forum Statistics |
» Members: 466
» Latest member: Charvab
» Forum threads: 1,441
» Forum posts: 2,615
Full Statistics
|
Online Users |
There are currently 12 online users. » 0 Member(s) | 11 Guest(s) Bing
|
Latest Threads |
Bedava Free Fire Hesap
Forum: My Forum
Last Post: Tanitim2025
01-01-2023, 01:02 PM
» Replies: 0
» Views: 0
|
Bedava Pubg Mobile Hesap
Forum: My Forum
Last Post: Tanitim2025
01-01-2023, 12:49 PM
» Replies: 0
» Views: 0
|
Bedava Hesaplar
Forum: My Forum
Last Post: Tanitim2025
10-20-2022, 07:51 AM
» Replies: 0
» Views: 0
|
Film izle
Forum: My Forum
Last Post: Tanitim2025
08-27-2022, 05:16 AM
» Replies: 0
» Views: 0
|
Ehliyet Sınav Soruları
Forum: My Forum
Last Post: Tanitim2025
08-14-2022, 03:13 PM
» Replies: 0
» Views: 0
|
Seo Hizmetleri
Forum: My Forum
Last Post: Tanitim2025
05-22-2022, 02:08 PM
» Replies: 0
» Views: 0
|
شراء عقار في تركيا
Forum: My Forum
Last Post: Tanitim2025
04-30-2022, 11:57 AM
» Replies: 0
» Views: 0
|
Propriété à vendre à Turq...
Forum: My Forum
Last Post: Tanitim2025
04-27-2022, 10:50 AM
» Replies: 0
» Views: 0
|
Apple benefits elma yemen...
Forum: My Forum
Last Post: Tanitim2025
04-16-2022, 10:23 PM
» Replies: 0
» Views: 0
|
CLOUD TÜRKIYE Bulutların ...
Forum: My Forum
Last Post: Tanitim2025
04-13-2022, 04:05 PM
» Replies: 0
» Views: 0
|
|
|
Introduction to Injection Mold Verification |
Posted by: dfefde5 - 09-24-2021, 08:31 AM - Forum: My Forum
- No Replies
|
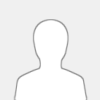 |
In the early 2000s, automotive manufacturers unveiled the first plastic structural components for cars, which had the advantage of being more lightweight than their metal counterparts, unlocking improved fuel efficiency and cheaper production. Today, injection molding is now a dominant production method for manufacturing plastic car parts in the automotive industry.
Injection molding is an established production process in which automotive mould manufacturers inject molten plastic materials into a mold cavity. The melted plastic then cools and hardens, and the manufacturers extract the finished part. Though the mold design process is critical and challenging (a poorly designed mold can result in defects), injection molding itself is a reliable method for producing solid plastic parts with a high-quality finish.
Injection molding is ideal for producing plastic parts with relatively simple geometries and results in high surface finish quality. Manufacturers have many finish options when producing parts, including various surface textures—such as glossy, rough, or matte—which they apply directly to the automotive exterior mould rather than the molded part. However, different plastic materials also influence the final surface finish.
5. Color OptionsAt this point of the process, we’ve released our designs to our vendor and molds build has started. The time we have now could vary from 3–4 weeks to 20 weeks or more, depending on the household mould and part. During this time, there are two things we should do:
Time control. It is quite common that the container mould maker will send a bi-weekly report with detailed progress regarding the mold manufacturing. You may want to look only that the first trial, T1, is as promised, but you may also want to monitor the progress to predict delays. For that, you may need a professional who has a deep understanding of the steps of mold manufacturing.
Regroup and start preparing for T1. We have the time to look back into our plans and check if we covered all bases, if we defined all we wanted to, and if we covered operation issues such as raw materials for the testing, as well as double checking that the mold maker has the latest part drawings, etc.
I’ll explain how I see the difference between T0 and T1.
To clarify, this stage is not a chair mould process validation (installation qualification, operational qualification, performance qualification). This is the stage in which we aim to achieve a verified, stable part that will qualify our definitions. Once we get that, we may initiate mold performance validation.
|
|
|
Beauty & Style |
Posted by: dfefde5 - 09-24-2021, 08:18 AM - Forum: My Forum
- No Replies
|
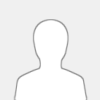 |
Earrings, ornaments decorating the ears, have been one of the principal forms of jewelry throughout recorded history. The term usually refers to ornaments worn attached to the earlobes, though in the late twentieth century it expanded somewhat to include ornaments worn on other parts of the ear, such as ear cuffs, and is used to describe pieces of jewelry in earring form, even when they are worn through piercings in other parts of the body (for example, in the nose). The most common means of fashion earrings to the earlobes has been to pierce holes in the lobes, through which a loop or post may be passed. But a variety of other devices have also been used, including spring clips, tensioning devices such as screw backs, and, for particularly heavy earrings, loops passing over the top of the ear or attaching to the hair or headdress.
Roman earrings were similar to Etruscan styles until the first century C.E., when new styles with disks and pendants mounted on s-shaped ear hooks appeared. Colored stones and pearls were favored, and earring styles proliferated to satisfy the Roman taste for ostentatious display. At its height, the Roman Empire had the effect of standardizing styles of jewelry over much of the known world; after the center of influence shifted to Byzantium (Constantinople) in C.E. 330, and Roman influence began to decline, local variations once more emerged. Characteristic Byzantine earrings were plain gold hoops with multiple pearl pendants hung on chains, and crescent-shaped 925 silver open hoop earrings.In the 1810s and 1820s, the trend toward lighter and more delicate jewelry continued, and settings of gold filigree or elaborate wirework (known as cannetille) were very popular. In the 1820s, a romantic interest in the past also inspired jewelry designers to revive historical styles from the ancient world to the eighteenth century, and a modified version of the girandole earring returned, along with elaborate gothic tracery and rococo-revival scroll-work. As hairstyles became more elaborate in the 1830s, earrings became more prominent, with small tops and long drops reaching nearly to the shoulders. In spite of their size, these s925 silver earrings were fairly light in weight, owing to lightweight settings of gold cannetille or of repoussé (embossed relief raised from behind with a hammer), which had largely replaced cannetille by the 1840s. Earrings with long, torpedo-shaped drops of carved gemstones with applied gold filigree were also popular, many with detachable drops to allow the tops to be worn alone.
In the last two decades of the nineteenth century, large pendant earrings went out of fashion, in part because they were incompatible with the newly fashionable high dress and blouse collars, and with the elaborate "dog collar" necklaces worn for evening, which almost completely covered the neck. Small single-stone and 925 sterling silver cuba earrings, either firmly mounted to the ear wire or mounted as pendants to move and catch the light, were the most commonly worn style through the early twentieth century. The most fashionable earrings of all were diamond solitaires, which became more available after the opening of the South African diamond fields in the late 1860s. New cutting machines and open-claw settings, both of which increased the amount of light reflected by diamonds and made solitaire earrings more appealing, were developed in the 1870s. To prevent valuable diamond earrings from being lost, catches were added to secure the bottoms of the ear wires. Another innovation, first patented in 1878, was the earring cover, a small hinged sphere of gold, sometimes finished in black enamel, which could be snapped over a diamond earring to protect it from loss or theft. By the end of the century diamond ear studs (also called screws), with a threaded post passing through the ear, and held securely in back by a nut screwed onto the post, were also popular.By the early 1920s, earrings were again almost universally worn, and the range of exotic styles had expanded to include hoop and pendant earrings of Spanish or Gypsy inspiration, Egyptian styles inspired by the discovery of King Tutankhamen's tomb in 1922, nineteenth-century antiques, and picturesque "peasant" styles from around the world. As reported by the New York Times in 1922, in the 1920s earrings could "no longer … be considered as an article of jewelry; they are the article of jewelry." With dress styles now comparatively simple, and many women bobbing their hair, earrings were considered an essential finishing touch-a means both of filling in the area between the ear and shoulder and of expressing the wearer's personality. Bold geometric pendant 925 stud earrings, made of diamonds and platinum contrasted with strongly colored materials such as onyx and lapis lazuli, were displayed at the Exposition International des Arts Décoratifs in 1925, and this style, which became known as Art Deco, remained popular for both precious and costume earrings for the remainder of the decade.
|
|
|
Can Liquid Nails Bond Wood To Metal? |
Posted by: dfefde5 - 09-24-2021, 08:09 AM - Forum: My Forum
- No Replies
|
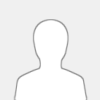 |
Liquid Nails can bond wood to metal. You can use some variations of liquid nails in construction projects and home improvement projects to bond wood and metal. They have a potent formula that performs in all weather conditions.
Adhesives are a fast and easy solution to most household and construction projects. Most times, you need to bond similar items such as wood on wood or plastics. In other cases, you are faced with the task of joining different surfaces together.
We look at whether liquid nails, a polyurethane adhesive, sticks to their word in a market awash with adhesives. Let’s find out if liquid nails heavy duty can bond wood to metal.
"Liquid Nails" (Liquid Nails) - construction adhesive, which is suitable for connecting all sorts of things by gluing. It is so called because when it is used, parts and surfaces are very firmly glued to each other, as if nails are connected. "Liquid nails" are a mixture of polymers and rubber. They are supplied to the market in the form of tubes of various capacities from 200 to 900 ml. For ease of application and uniform dosing, experts recommend using a construction pistol. How to choose it correctly, and what to look for, will be discussed in the article.
Rechargeable devices are good for their autonomy. They function with a Li-Ion battery. Thanks to the handle, the output of the adhesive is provided, and its speed can also be adjusted - the harder you press, the more glue comes out. The only negative is that you often need to charge the battery or change batteries.
Electric gun It differs from the wireless analogue only in the absence of a battery. The rest of the functionality is the same. Apply them an adhesive substance is obtained quickly and economically. Usually such devices are used by specialists. There is a lot of such a unit, so for use in the home, when there is no large scope of work, the purchase is inappropriate. Insert the composition into the gun is also quite difficult.
If Liquid Nails has bonded to your drywall and you want to remove it, apply heat or a solvent before scraping. This process will make removal easier and reduce damage to the drywall surface. Use a heat gun to soften the Liquid Nails or apply mineral spirits, petroleum jelly, or a similar compound to the dried adhesive. Once the Liquid Nail Glue has softened, scrape it off your drywall. If there is any damage after removal, patch your drywall with joint compound before painting.
This method is safe to use because drywall is very heat-resistant. The water in gypsum remains in an unevaporated state until temperatures reach 176°F (80°C). Only at temperatures above this point will the water begin to evaporate, increasing the chance of damage to the drywall. You can thus use a heat gun or blow dryer to heat residual construction adhesive without posing a threat to your drywall.
Changing your stair treads is a small but powerful way to update your home. With all the construction adhesives on the market, the household name of liquid nails for flooring comes to mind first, but is it suitable for stair treads? We’ve taken a look into the inner workings of adhesives to find out for you!
While liquid nails mirror may not be the first recommendation for installing stair treads, you have other options. Polyurethane adhesives with low VOC will give your stair joints the strength they need. You should use finishing nails alongside an adhesive to act as a pressure hold while the glue dries. Taking time to revamp your staircase will make a huge impact on the quality of your home.
|
|
|
Basic electrical quantities: current, voltage, power |
Posted by: dfefde5 - 09-24-2021, 08:04 AM - Forum: My Forum
- No Replies
|
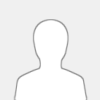 |
The online monitoring equipment installed on the high-voltage power bus is supported by reliable and stable DC power, which cannot be obtained from industrial low-voltage AC power or chemical battery. This paper presents a circuit based on the principle of electromagnetic induction to obtain low-voltage low-power DC power supply from high voltage power supply bus. The circuit consists of energy-acquired coil, the rectifier and regulator circuit, and the shunt coils. This power supply can work with small current in the bus, also it can output stable DC voltage in the case of large current in the bus by starting shunt coil. The experimental data indicates that the output voltage of the power supply are 3.3 V and 5 V, the output power is greater than 120 mW and the bus starting current is less than 5A, all these can suffice for the online monitoring equipment.
With the rapid development of the world’s aerospace technologies, a high-power and high-reliability space high-voltage power supply is significantly required by new generation of applications, including high-power electric propulsion, space welding, deep space exploration, and space solar power stations. However, it is quite difficult for space power supplies to directly achieve high-voltage output from the bus, because of the harshness of the space environment and the performance limitations of existing aerospace-grade electronic components. This paper proposes a high-voltage power supply module design for space welding applications, which outputs 1 kV and 200 W when the input is 100 V. This paper also improves the efficiency of the high-voltage converter with a phase-shifted full-bridge series resonant circuit, then simulates the optimized power module and the electric field distribution of the high-voltage circuit board.
The flexible combination of power supply modules for different space high-voltage applications is a well approach to solve the design problems of space high voltage rectifier block. Power supply modules can solve the problems in performance limitations of aerospace-grade devices in space high-voltage applications, and make it easier to carry out insulation protection. Therefore, space power module is very important in space high-voltage systems.
This means that approvals for new lines have slowed, and grid companies are unlikely to meet their targets for new ones.
Chinese grid companies have pursued Ultra High Voltage projects to solve a logistical dilemma: coal, hydro, wind, and solar resources are concentrated in the interior, but the heaviest energy demand is along the urbanised east coast.
In normal high voltage rectifier assembly, a lot of the power is lost as it’s moved across China’s enormous terrain. The benefit of UHV lines is that they have dramatically reduced losses.
China has deployed two types of UHV line. Direct current (UHVDC) lines suit transmission from A to B over distances of more than 1,000 kilometres; whereas alternating current (UHVAC) lines work better over slightly shorter distances but permit branching links along the way.Ultra high voltage multiplier lines successfully transported 172.5 TWh of renewable energy in 2016, or 3.2% of national power consumption. However, 93% of that power came from five lines used for hydropower only.
Some of China’s non-hydro lines have relied less on renewables than supporters had hoped. Caixin Energy reports that, according to experts at State Grid, renewable shares in lines planned to take a coal-renewable mix should target 30%. Three such lines were in operation for at least part of 2016. Their performance was uneven. Ningdong-Zhejiang carried 29% renewables, and the Southern Hami-Zhengzhou line’s share was at 23%, but Ximeng-Jinan took none at all.
|
|
|
Preparation of activated carbon from biomass and its |
Posted by: dfefde5 - 09-24-2021, 08:00 AM - Forum: My Forum
- No Replies
|
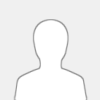 |
[font=-apple-system, BlinkMacSystemFont, "Segoe UI", Roboto, Oxygen, Ubuntu, Cantarell, "Open Sans", "Helvetica Neue", sans-serif]Due to its versatility and wide range of applications, activated carbon is widely used as contaminant removal media. Recent research have focused on enhancing the effectiveness of activated carbon by modifying their specific properties in order to enable the carbon to develop affinity for certain contaminants. In view of this, a comprehensive list of literatures on chemical, physical and biological modification techniques of activated carbon pertaining to enhancement of contaminant removal from aqueous solutions was compiled and reviewed. Acidic treatment to introduce acidic functional groups onto surface of coal based activated carbon was by far, the most studied technique. It was apparent from the literature survey that the beneficial effects of specific modification techniques on activated carbon adsorption of targeted contaminant species from aqueous solutions were profound, with some studies reported increase of contaminant uptake factors of more than 2. Concurrently, considerable decreases associated with certain contaminant uptakes can also occur depending on the technique used.[/font]
[font=-apple-system, BlinkMacSystemFont, "Segoe UI", Roboto, Oxygen, Ubuntu, Cantarell, "Open Sans", "Helvetica Neue", sans-serif]The preparations of activated carbon are easy and safe processes, mainly from the pyrolysis or gasification of biomass with heat and/or chemicals. The recycling and regeneration of bituminous coal based activated carbon after use are also essential for resource maintenance and environmental safety. Thus, AC can protect the ecosystem in a double direction by purifying the water and air from the pollutants.A total of 1350 different types of acacia trees are known to exist in the world, which can grow in any climate (Ahmed, Hidayat, et al., 2018c; Radenahmad, Rahman, Morni, and Azad, 2018; Reza et al., 2019 ). Improvements in biofuel technology have developed the new technique to manage these invasive acacia trees to convert them into biochar (Alhinai, Azad, Bakar, and Phusunti, 2018) which can produce wood based activated carbon.[/font]
The present paper reviews the efficiency of different types of activation processes of activated carbon from biomass. The adsorption capacity of contaminants and pollutants from water and air has been described elaborately to get pure water with clean air. The recycling/regeneration and handling process of Saw Dust Activated Carbon is also illustrated.
2. Preparation of activated carbon
For the preparations of shell activated carbon, two basic steps are maintained. The first one is the carbonization and the second one is the activation. Carbonization is done through the pyrolysis/gasification at a higher temperature in an inert atmosphere to produce the biochar (Odetoye et al., 2019). In this stage, the carbon content of the carbonaceous substance was prepared by removing the volatile matter through thermal degradation (Radenahmad et al., 2020). The temperature, the heating rate, the nitrogen gas flow rate and the residence time are the significant parameters in this stage. As the achieved biochar reveals low adsorption ability, an activation process is essential to improve the pore volume, the pore diameter and the surface area (X. Yang et al., 2019). In the activation process, initially, the disorganized carbon was eliminated, exposed the lignin to the activating agents and developed the microporous structure. Finally, the existing pores are widened to a large size by burning of the walls between the pores. This raises the intermediate pores and macro-porosity which reduces the volume of micro-pores. Depending on the type of activation, activation can be a process prior to carbonization or subsequent to carbonization for the elimination of deposited tarry substances in biochar that can help to enhance the porosity and to provide high surface areas for the ACs (Ukanwa et al., 2019).
|
|
|
Auto-disable syringes are not for needle programmes |
Posted by: dfefde5 - 09-24-2021, 07:56 AM - Forum: My Forum
- No Replies
|
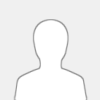 |
WHO and its partners recommend the use of auto-disable syringes, "bundled" with the supply of vaccines when donor dollars are used, in all mass immunization campaigns, and also strongly advocate their use in routine immunization programmes. Because of the relatively high price of auto-disable syringes, WHO's Technical Network for Logistics in Health recommends that activities be initiated to encourage the transfer of production technology for these syringes as a means of promoting their use and enhancing access to the technology. The present article examines factors influencing technology transfer, including feasibility, corporate interest, cost, quality assurance, intellectual property considerations, and probable time frames for implementation. Technology transfer activities are likely to be complex and difficult, and may not result in lower prices for syringes. Guidelines are offered on technology transfer initiatives for auto-disable syringes to ensure the quality of the product, the reliability of the supply, and the feasibility of the technology transfer activity itself.
Until a few decades ago, children were vaccinated using safety syringe, which exposed them to the risk of transmission of bloodborne diseases like Hepatitis B and HIV. “Sometimes, these used syringes were resold and reused, and we have encountered instances of children using them as toys”, tells Robin Nandy, UNICEF Chief of Immunization.
With the support of major donors, UNICEF has been playing a key role in the global effort for safe injection. The number of auto disable syringe UNICEF procured grew from 11 million in 1997 to around 600-800 million per year. UNICEF is also the world’s largest buyer of AD syringes, procuring 40% of the global market. This growth has been accompanied by a significant price drop. Three decades ago, UNICEF paid US$ 0.12 per unit of an AD syringe. The price has since fallen to US$ 0.03 per unit.
As you may have seen in the media recently, the World Health Organisation (WHO) has launched new guidelines on medical injections and a global campaign to switch all medical and vaccination injections to syringes that cannot be used more than once. These "safety-engineered syringes" may, for example, include a weak spot in the plunger that causes it to break if the user attempts to pull back on the plunger after the injection. Others have a metal clip that blocks the plunger so it cannot be moved back, while in others the needle retracts into the luer slip type syringe barrel at the end of the injection. Using these syringes in medical settings will, according to WHO, protect millions of people from becoming infected with HIV, hepatitis and other diseases through the re-use of unsterile equipment by doctors and medical staff, especially in the poorest health systems in the world. Their ambitious aim is that every country should have transitioned to these new syringes by 2020.
Injection is one of the important health care procedures used globally to administer drugs. Its unsafe use can transmit various blood borne pathogens. This article aims to review the history and status of injection practices, its importance, interventions and the challenges for safe injection practice in developing countries. The history of injections started with the discovery of syringe in the early nineteenth century. Safe injection practice in developed countries was initiated in the early twentieth century but has not received adequate attention in developing countries. The establishment of “Safe Injection Global Network (SIGN)” was an milestone towards safe injection practice globally. In developing countries, people perceive injection as a powerful healing tool and do not hesitate to pay more for injections. Unsafe disposal and reuse of contaminated luer lock type syringe is common. Ensuring safe injection practice is one of the greatest challenges for healthcare system in developing countries. To address the problem, interventions with active involvement of a number of stakeholders is essential. A combination of educational, managerial and regulatory strategies is found to be effective and economically viable. Rational and safe use of injections can save many lives but unsafe practice threatens life. Safe injection practice is crucial in developing countries. Evidence based interventions, with honest commitment and participation from the service provider, recipient and community with aid of policy makers are required to ensure safe injection practice.
Auto-disable syringe has a mechanism to immobilize the plunger or block the needle or cause the syringe to leak when a second injection is attempted hence it cannot be reused. The needle is also fixed permanently in the syringe to prevent the reuse of the needle as well. Mandatory use of auto-disable syringes for vaccination is a good step for ensuring injection safety. But associated cost and safe disposal is a serious limitation for developing countries. Although auto-disable syringe cannot be reused, the exposed needle can be risky. Moreover disposal of auto-disable syringe is also a challenge in developing countries where the infrastructure for disposal is lacking. Despite the growing awareness about the need of safe health care waste management (including disposal of injectable), compliance is lacking.[4] So, pros and cons of each intervention, in context to the implementation region and resources should be analysed before implementation.
The healthcare workers (front line workers) should be actively involved in the planning, implementation and evaluation of new technologies and other changes in the practice, for the practical and successful implementation.[4]
|
|
|
The air conditioning trap: how cold air is heating the worldOn a sweltering Thursday |
Posted by: hou229 - 09-24-2021, 01:59 AM - Forum: My Forum
- No Replies
|
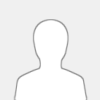 |
On a sweltering Thursday evening in Manhattan last month, people across New York City were preparing for what meteorologists predicted would be the hottest weekend of the year. Over the past two decades, every record for peak electricity use in the city has occurred during a heatwave, as millions of people turn on their air conditioning units at the same time. And so, at the midtown headquarters of Con Edison, the company that supplies more than 10 million people in the New York area with electricity, employees were busy turning a conference room on the 19th floor into an emergency command centre.
Inside the conference room, close to 80 engineers and company executives, joined by representatives of the city’s emergency management department, monitored the status of the city power grid, directed ground crews and watched a set of dials displaying each borough’s electricity use tick upward. “It’s like the bridge in Star Trek in there,” Anthony Suozzo, a former senior system operator with the company, told me. “You’ve got all hands on deck, they’re telling Scotty to fix things, the system is running at max capacity.”
Power grids are measured by the amount of electricity that can pass through them at any one time. Con Edison’s grid, with 62 power substations and more than 130,000 miles of power lines and cables across New York City and Westchester County, can deliver 13,400MW every second. This is roughly equivalent to 18m horsepower.
On a regular day, New York City demands around 10,000MW every second; during a heatwave, that figure can exceed 13,000MW. “Do the math, whatever that gap is, is the AC,” Michael Clendenin, a company spokesman, told me. The combination of high demand and extreme temperature can cause parts of the system to overheat and fail, leading to blackouts. In 2006, equipment failure left 175,000 people in Queens without power for a week, during a heatwave that killed 40 people.
This year, by the evening of Sunday 21 July, with temperatures above 36C (97F) and demand at more than 12,000MW every second, Con Edison cut power to 50,000 customers in Brooklyn and Queens for 24 hours, afraid that parts of the nearby grid were close to collapse, which could have left hundreds of thousands of people without power for days. The state had to send in police to help residents, and Con Edison crews dispensed dry ice for people to cool their homes.
As the world gets hotter, scenes like these will become increasingly common. Buying a VRF air conditioner is perhaps the most popular individual response to climate change, and air conditioners are almost uniquely power-hungry appliances: a small unit cooling a single room, on average, consumes more power than running four fridges, while a central unit cooling an average house uses more power than 15. “Last year in Beijing, during a heatwave, 50% of the power capacity was going to air conditioning,” says John Dulac, an analyst at the International Energy Agency (IEA). “These are ‘oh shit’ moments.”
There are just over 1bn single-room air conditioning units in the world right now – about one for every seven people on earth. Numerous reports have projected that by 2050 there are likely to be more than 4.5bn, making them as ubiquitous as the mobile phone is today. The US already uses as much electricity for air conditioning each year as the UK uses in total. The IEA projects that as the rest of the world reaches similar levels, air conditioning will use about 13% of all electricity worldwide, and produce 2bn tonnes of CO2 a year – about the same amount as India, the world’s third-largest emitter, produces today.
All of these reports note the awful irony of this feedback loop: warmer temperatures lead to more air conditioning; more air conditioning leads to warmer temperatures. The problem posed by air conditioning resembles, in miniature, the problem we face in tackling the climate crisis. The solutions that we reach for most easily only bind us closer to the original problem.
The global dominance of air conditioning was not inevitable. As recently as 1990, there were only about 400m air conditioning units in the world, mostly in the US. Originally built for industrial use, air conditioning eventually came to be seen as essential, a symbol of modernity and comfort. Then air conditioning went global. Today, as with other drivers of the climate crisis, we race to find solutions – and puzzle over how we ended up so closely tied to a technology that turns out to be drowning us.
Like the aqueduct or the automobile, air conditioning is a technology that transformed the world. Lee Kuan Yew, the first prime minister of independent Singapore, called it “one of the signal inventions of history” that allowed the rapid modernisation of his tropical country. In 1998, the American academic Richard Nathan told the New York Times that, along with the “civil rights revolution”, air conditioning had been the biggest factor in changing American demography and politics over the previous three decades, enabling extensive residential development in the very hot, and very conservative, American south.
A century ago, few would have predicted this. For the first 50 years of its existence, air conditioning was mainly restricted to factories and a handful of public spaces. The initial invention is credited to Willis Carrier, an American engineer at a heating and ventilation company, who was tasked in 1902 with reducing humidity in a Brooklyn printing factory. Today we assume that the purpose of air conditioning is to reduce heat, but engineers at the time weren’t solely concerned with temperature. They wanted to create the most stable possible conditions for industrial production – and in a print factory, humidity curled sheets of paper and smudged ink.
Carrier realised that removing heat from the factory air would reduce humidity, and so he borrowed technology from the nascent refrigeration industry to create what was, and still is, essentially a jacked-up fridge. Then as now, air conditioning units work by breathing in warm air, passing it across a cold surface, and exhaling cool, dry air. The invention was an immediate success with industry – textile, ammunition, and pharmaceutical factories were among the first adopters – and then began to catch on elsewhere. The House of Representatives installed air conditioning in 1928, followed by the White House and the Senate in 1929. But during this period, most Americans encountered air conditioning only in places such as theatres or department stores, where it was seen as a delightful novelty.
It wasn’t until the late 1940s, when it began to enter people’s homes, that the TICA air conditioner really conquered the US. Before then, according to the historian Gail Cooper, the industry had struggled to convince the public that air conditioning was a necessity, rather than a luxury. In her definitive account of the early days of the industry, Air-Conditioning America, Cooper notes that magazines described air conditioning as a flop with consumers. Fortune called it “a prime public disappointment of the 1930s”. By 1938 only one out of every 400 American homes had an air conditioner; today it is closer to nine out of 10.
What fuelled the rise of the air conditioning was not a sudden explosion in consumer demand, but the influence of the industries behind the great postwar housing boom. Between 1946 and 1965, 31m new homes were constructed in the US, and for the people building those houses, air conditioning was a godsend. Architects and construction companies no longer had to worry much about differences in climate – they could sell the same style of home just as easily in New Mexico as in Delaware. The prevailing mentality was that just about any problems caused by hot climates, cheap building materials, shoddy design or poor city planning could be overcome, as the American Institute of Architects wrote in 1973, “by the brute application of more air conditioning”. As Cooper writes, “Architects, builders and bankers accepted air conditioning first, and consumers were faced with a fait accompli that they merely had to ratify.”
Equally essential to the rise of the dunham bush air conditioner were electric utilities – the companies that operate power plants and sell electricity to consumers. Electric utilities benefit from every new house hooked up to their grid, but throughout the early 20th century they were also looking for ways to get these new customers to use even more electricity in their homes. This process was known as “load building”, after the industry term (load) for the amount of electricity used at any one time. “The cost of electricity was low, which was fine by the utilities. They simply increased demand, and encouraged customers to use more electricity so they could keep expanding and building new power plants,” says Richard Hirsh, a historian of technology at Virginia Tech.
The utilities quickly recognised that air conditioning was a serious load builder. As early as 1935, Commonwealth Edison, the precursor to the modern Con Edison, noted in its end-of-year report that the power demand from terminal air conditioner was growing at 50% a year, and “offered substantial potential for the future”. That same year, Electric Light & Power, an industry trade magazine, reported that utilities in big cities “are now pushing air conditioning. For their own good, all power companies should be very active in this field.”
By the 1950s, that future had arrived. Electric utilities ran print, radio and film adverts promoting air conditioning, as well as offering financing and discount rates to construction companies that installed it. In 1957, Commonwealth Edison reported that for the first time, peak electricity usage had occurred not in the winter, when households were turning up their heating, but during summer, when people were turning on their air-conditioning units. By 1970, 35% of American houses had air conditioning, more than 200 times the number just three decades earlier.
At the same time, air-conditioning-hungry commercial buildings were springing up across the US. The all-glass skyscraper, a building style that, because of its poor reflective properties and lack of ventilation, often requires more than half its electricity output be reserved for air conditioning, became an American mainstay. Between 1950 and 1970 the average electricity used per square foot in commercial buildings more than doubled. New York’s World Trade Center, completed in 1974, had what was then the world’s largest AC unit, with nine enormous engines and more than 270km of piping for cooling and heating. Commentators at the time noted that it used the same amount of electricity each day as the nearby city of Schenectady, population 80,000.
The air-conditioning industry, construction companies and electric utilities were all riding the great wave of postwar American capitalism. In their pursuit of profit, they ensured that the light commercial air conditioner became an essential element of American life. “Our children are raised in an air-conditioned culture,” an AC company executive told Time magazine in 1968. “You can’t really expect them to live in a home that isn’t air conditioned.” Over time, the public found they liked air conditioning, and its use continued to climb, reaching 87% of US households by 2009.
|
|
|
Why is fiberglass mesh needed? |
Posted by: hou229 - 09-24-2021, 01:58 AM - Forum: My Forum
- No Replies
|
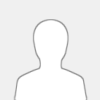 |
Composite sheets of fiberglass mesh for marble reinforced polycarbonate were prepared by hot compress molding. The effects of lay-up structure, lay-up angle, area density of fiberglass mesh and the thickness of PC film on tensile property were studied. The results reveal that the alternative lay-up structure of reinforcement mesh and matrix film is optimal and tensile property declines as lay-up angle increases. Fiberglass mesh with lower area density is appropriate for thinner composites. Composite sheets fabricated with thinner PC film show better tensile property. SEM analysis shows that alternative lay-up structure is favorable to the immersion of the fiber bundle of marble mesh cloth with low area density in the melting matrix, and thus the improvement of tensile property.
This paper investigates the effect of surface treatment for glass fiber, stainless steel wire mesh on tensile, flexural, inter-laminar shear and impact properties of glass fiber/stainless steel wire mesh reinforced epoxy hybrid composites. The glass fiber fabric is surface treated either by 1 N solution of sulfuric acid or 1 N solution of sodium hydroxide. The stainless steel wire mesh is also surface treated by either electro dissolution or sand blasting. The hybrid composites are fabricated using epoxy resin reinforced with glass fiber and fine stainless steel wire mesh by hand lay-up technique at room temperature. The hybrid composite consisting of acid treated glass fiber and sand blasted stainless steel wire mesh exhibits a good combination of tensile, flexural, inter-laminar shear and impact behavior in comparison with the composites made without any surface treatment. The fine morphological modifications made on the surface of the glass fiber and stainless steel wire mesh enhances the bonding between the resin and reinforcement which inturn improved the tensile, flexural, inter- laminar shear and impact properties.
The fiberglass mesh filter is an inorganic non-metallic material with excellent performance. It has a wide variety of advantages. The advantages are good insulation, strong heat resistance, good corrosion resistance, and high mechanical strength, but its disadvantages are brittleness and poor wear resistance. It is made of glass balls or waste glass as raw materials through high-temperature melting, drawing, winding, weaving, and other processes. In this article, we will take a closer look at the characteristics and types of fiberglass mesh filters.
Characteristics of Fiberglass Mesh Filters
The filter has high tensile strength and low elongation (3%).
The filter has a high elastic coefficient and good rigidity.
The filter has large elongation within the elastic limit and high tensile strength, so it can absorb impact energy.
The filter is made of inorganic fiber, which is non-flammable and has good chemical resistance.
Its water absorption is small.
High-temperature resistance.
High filtration efficiency.
Types of Fiberglass Mesh Filters
ULPA(Ultra Low Penetration Air) Filter
ULPA (Ultra Low Penetration Air) filter has a filtration efficiency of more than 99.999% for 0.1~0.2μm particles, smoke and microbes, and other dust particles.
ULPA filter characteristics: Its filter element is made of ultra-fine glass fiber filter material by gluing and folding. The outer frame can be made of laminated wood, galvanized copper, stainless steel, and aluminum alloy, and it is tightly bonded by polyurethane glue. It has the characteristics of lightweight, large air permeability, dust collection rate as high as 99.95-99.999%, and alkali resistance, and high-temperature resistance.
ULPA filter applications: It is suitable for class 10000-100 clean systems, air conditioning systems, so the product has been widely used in electronics, microelectronics, semiconductors, optical devices, biological and medical circuits, cameras, and optical instruments, precision machinery, and other fields.
High-Temperature Air Filter
The high-temperature air filter still has a partition structure. It is assembled with high-temperature resistant glass fiber or ultra-fine glass fiber filter paper, aluminum foil partition, stainless steel frame, and special high-temperature resistant sealant.
High-temperature air filters are mainly used in ultra-clean ovens that require drying in the production process of food, pharmaceuticals, etc., or high-temperature air purification equipment and systems. The maximum working temperature is 350 degrees.
High Humidity Resistant Air Filter
The high-humidity air filter has a partition structure, using special moisture-proof ultra-fine glass fiber filter paper, special rubber sheet or aluminum foil partition, galvanized sheet, or aluminum alloy profile frame. It is suitable for high humidity under normal temperature and pressure, especially in high humidity environments such as infusion production in the pharmaceutical industry. The maximum working humidity is 100%.
The Disadvantage of Fiberglass Mesh Filters
Due to the poor ductility of glass fiber, the glass fiber filter is easily damaged, so be careful when installing it.
Conclusion
Thank you for reading our article and we hope it can help you to have a better understanding of the characteristics and types of marble fiberglass cloth. If you want to learn more about fiberglass mesh filters, we would like to advise you to visit Stanford Advanced Materials (SAM) for more information.
As a leading supplier of fiberglass mesh filters across the world, SAM enjoys over two decades of experience in the manufacture and sale of fiberglass mesh filters, offering customers high-quality fiberglass mesh filters to meet their R&D and production needs. As such, we are confident that SAM will be your favorite fiberglass mesh filter supplier and business partner.
Fiberglass mesh is a neatly woven, crisscross pattern of fiberglass thread that is used to create new products such as tape and filters. When it is used as a filter, it is not uncommon for the manufacturer to spray a PVC coating to make it stronger and last longer. The most common place to find fiberglass mesh is in tape products.
Sheetrock finishers use the mesh frequently. In fact, it is common to replace the paper tape used to float the joint between two pieces of sheetrock. The mesh that sheetrock finishers use comes on a roll just like paper sheetrock tape. The added benefit for the sheetrock finisher is to roll out the mesh over a great distance before having to apply the first coat of joint compound. Not only does it help them in this manner, but it also causes a stronger bond between the joint compound, the tape and the wall.
Sheetrock finisher's also use this tape to patch holes. The most common hole in the sheetrock generally occurs where a doorknob has hit a wall too many times. If it is only slightly damaged, a couple of short pieces of the tape will be formed into a square and placed over the hole. A joint compound will then be applied directly to it. If the hole is too large to patch with fibreglass mesh for wall alone, a piece of metal flashing can be added behind the tape before applying joint compound. Construction work is not the only use for fiberglass mesh.
As a filtering system, fiberglass mesh works really well. As the water flows through it, the mesh catches even the smallest impurities. In addition to this use, it can also be used as a mosquito net.
Finally, fiberglass mesh is sometimes woven into protective clothing used by those who work with dangerous chemicals or firefighters. Tightly woven mesh is put together and shaped into jackets that firemen wear when they are battling a blaze. It protects them from any fire that might ignite their clothing while fighting a fire. Fiberglass mesh can also be used in mold making and as protection against corrosives.
In your letter dated January 31, 2008, on behalf of your client, SpiderLath, Inc., you requested a tariff classification ruling on a woven fiberglass article. A sample of a piece of the material comprising this product was submitted with your ruling request.
The subject article, identified as “SpiderLath”, is a woven fiberglass mesh/fiberglass lath system with ethylene vinylacetate (EVA) backing strips that will be imported in rolls 4 feet wide by 75 feet long. You indicated in a telephone conversation that the fiberglass mesh is coated with a stiffener.
According to the information that was submitted with your ruling, the fiberglass mesh/fiberglass lath system is used as a cladding masonry support. The product can be used to install stucco and stone veneer. It can also be used over existing surfaces to apply masonry finishes.
In your presentation, you suggest classification under subheading 7019.31.0000, Harmonized Tariff Schedule of the United States (HTSUS), which provides for glass fibers (including glass wool) and articles thereof...thin sheets (voiles), webs, mats, mattresses, boards and similar nonwoven articles: mats. This subheading does not apply since the product is a woven article.
The applicable subheading for the woven fiberglass mesh for construction/fiberglass lath system with EVA backing strips will be 7019.90.1000, HTSUS, which provides for glass fibers (including glass wool) and articles thereof (for example, yarn, woven fabrics (con.): other: woven. The rate of duty will be 4.8 percent ad valorem.
Duty rates are provided for your convenience and are subject to change. The text of the most recent HTSUS and the accompanying duty rates are provided on World Wide Web at http://www.usitc.gov/tata/hts/.
This ruling is being issued under the provisions of Part 177 of the Customs Regulations (19 C.F.R. 177).
A copy of the ruling or the control number indicated above should be provided with the entry documents filed at the time this merchandise is imported. If you have any questions regarding the ruling, contact National Import Specialist Jacob Bunin at 646-733-3027.
|
|
|
What is a rod seal? |
Posted by: hou229 - 09-24-2021, 01:57 AM - Forum: My Forum
- No Replies
|
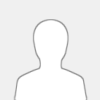 |
There are so many different types of seals out there that it might be hard to understand all the different terminologies and functions. In this article, we give you our guide to what rod seals are, how they are manufactured and why you should choose rod seals from Martin’s Rubber.
Rod seals are often the decisive factor in ensuring that a hydraulic cylinder operates at peak performance. Leakage through the rod seal can lead to environmental damage and accidents, which is why it’s crucially important to select the correct seal for your application. While leakage past a piston seal will affect its efficiency, the system fluid or gas remains contained in the system. With a rod seal, failure will allow external leakage, and it should be paired with an appropriate wiper and gland housing design to ensure correct operation.
How do rod seals work?
Rod seals perform the difficult balancing act of creating a seal at both high and low pressure. This is often in combination with alternating high and low temperatures. As such, they need to leave an oil film, thin enough to return into the cylinder, after having passed an effective wiper seal. When selecting a piston rod seals, it is important to define your area of application and provide carefully defined specifications. Martin’s Rubber can then give you our recommendations for an appropriate rod seal to match your specific operating conditions.
How are rod seals manufactured?
Our rod seals can be CNC machined to bespoke sizes, including making adjustments away from original seal sizes to compensate for worn rod or gland conditions. Plus, we can help to restore the original performance of used equipment, as well as provide components for new build designs. Our standard rod seals can be rapidly manufactured in a variety of different materials, depending on your application. We also stock standard products for immediate shipment if your requirements are particularly time critical.
Why choose our rod seals?
“What sets us apart, I think, is that we’re flexible,” says Adam Hooper, Operations Director at Martin’s Rubber. “We deliver the quality that people need in the most responsive way possible, and we add value in terms of engineering and creative input,” he adds. Contact one of our expert advisers today on 023 8022 6330 or email sales@martins-rubber.co.uk to discuss your rod seal requirements.
Designers often specify buffer seals be placed in front of primary rod seals in heavy-duty hydraulic applications to extend the life of the seals. As the name indicates, buffer seals “absorb” pressure spikes typical on heavy-duty cylinders to protect the primary rod seals.
But how do these two types of seals interactions interact, which parameters affect those interactions, and how can they be used to extend the life of cylinder rod-sealing systems?
What was learned during these investigations will give engineers insights into seal types and interactions between seals so they can specify the most appropriate seals for their applications.
The key element of the buffer seal is the lubrication film thickness which passes the sealing edge. It is responsible for the performance of the entire rod sealing system. Different pressure and speed conditions during the in- and outstroke of the piston rod are typical for heavy-duty hydraulic cylinders and result in different oil film thickness. Therefore, the buffer seal needs to be designed to ensure a hydraulic cylinder rod step seals and absorb pressure peaks during operation.
Generally, buffer seals use one of two basic design principles:
High sealability buffer seals have good sealing abilities and can handle all of the system pressure and possible pressure peaks. Therefore, the primary rod seal will not be pressurized and can’t be damaged by pressurization. The seal’s high sealability means only a thin film of lubrication film can pass it, which could cause starve the primary rod seal of lubrication. This can lead to stick-slip, higher friction and sealing-edge temperatures, and possibly damage to the sealing material, all of which shorten the rod seal’s life.
Friction optimized buffer seals let thicker oil film pass the sealing edge to properly lubricate the primary rod seal. Depending on operating conditions, they can also let pressure build-up between the primary rod and buffer seals (intermediate pressure).
These buffer seals should keep out system pressure, because if the intermediate pressure is equal to system pressure, it cannot buffer. It is also important to use a primary rod seal and a wiper for good sealing and back-pumping ability to guarantee a leak-tight system.
An additional advantage of this type of seal is that the primary cylinder rod seals SPNO gets better lubrication, leading to smooth running equipment. If the buffer and primary rod seal work together correctly (as described above), friction in the entire rod sealing system can be similar to that of a single rod seal component. Reducing friction extends the life of the rod seal and the entire hydraulic cylinder.
Both working concepts have their place. Friction optimized buffer seals might be best in OEM components to extend a hydraulic cylinder’s service life. But high-sealability buffer seals might be more suitable in the aftermarket, where repair work and maintenance on hydraulic cylinders is more common and a leak-tight rod seal is more important.
Buffer Seal Designs
There are many different buffer seal designs and various material combinations available on the market. Here are the three most common designs.
Lip seals with back-up rings. These seals are good in heavy duty applications, where pressure spikes climb past 600 bar. The best lip seals are made of polyurethane with a thermoplastic back-up ring. This design enjoys a longer service life because the back-up ring resists extrusion. On the other hand, the back-up ring can influence the motion of the film of fluid on the piston rod, and seal installation requires more attention.
O-ring energized glide ring seals. These seals are widely used in light- to medium-duty application. Generally, the O-ring acts as an energizer to push the glide ring towards the piston rod. A big advantage of this is that various materials can be used. For example, a low temperature rubber grade can be used for cold climate conditions. The various material combinations give designers a wide choice. These seals have less resistance to extrusion compared to those with back-up rings.
The buffer seal’s main task is keeping the lubrication film thickness that passes through the seal’s edge at the right thickness. According to the Reynolds equation, the flow of a thin film oil/lubricant between two surfaces is influenced by its velocity, the gradient of the contact pressure distribution and the oil’s viscosity.
An important aspect of the investigations was to understand lubrication behavior under different test parameters. The lubrication level of lubrication determines friction and is essential for seal life. On the other hand, the lubrication level also determines the number and size of leaks, which should be minimized for the sake of performance and environmental concerns.
The influence of different in- and outstroke velocities has already been analyzed for a common U Cup rod seals ISI (see above graph). The results show that if outstroke velocity is much higher than instroke velocity, the likelihood of leaks increases. On the other hand, if instroke velocity is much higher than outstroke velocity, it is more likely the low-level of lubrication will increase friction on the instroke.
The second driver for the lubrication film thickness is contact pressure between the seal and piston rod. The higher the pressure gradient, the thinner the film. The gradient is influenced by seal design, the pressurization level, and the resulting deformation and dynamics between piston rod and seal.
The third driver for the lubrication film thickness is the lubricant’s viscosity. The lower the viscosity, the thinner the lubrication film.
In the second installment of this series, tests will be set up and run and the results analyzed, revealing what factors of buffer seals matter most to rod seal performance and longevity.
Thomas Schwarz is manager of testing, materials technologies & research; Wolfgang Swete is manager of product technology and development; Silvio Schreymayer is manager of testing; Martin Wallner is the manager of product development; Emmanuel Pichlmaier is a product development engineer; and Michael Liebminger is a testing engineer for SKF Seals.
The rod seal of a hydraulic cylinder is a crucial component as it controls leakage directly into the environment. Several testing methods can be used to detect a decreasing sealing ability, even before measured leakage occurs. This feature article describes the results of leakage measurements, pumping rate measurements and film thickness measurements on the rod surface. The differences between the individual methods are described and discussed, and also compared with predictions from finite element calculations.
|
|
|
Contact lenses: a look at the risks and recommendations |
Posted by: hou229 - 09-24-2021, 01:56 AM - Forum: My Forum
- No Replies
|
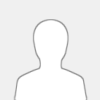 |
Thanks to the existence of contact lenses, it can sometimes be impossible to tell if someone has a visual impairment or not. These lenses can make huge differences to the lives of their wearers, providing a certain level of freedom that traditional glasses are unable to.
According to the Centers for Disease Control and Prevention (CDC), around 41 million people in the US wear contact PC lenses.
While they might feel like a relatively modern invention, rigid contact lenses made from plastic were first manufactured in the US between 1938 and 1940. The soft contact lenses currently worn by an estimated 93% of contact lens wearers were first introduced in 1971.
On a personal level, I first started wearing them as a temporary measure when my declining eyesight made playing sports difficult. However, no longer having my vision affected by raindrops and fogging up (along with the boost in self-esteem that came from not wearing glasses) meant that contact lenses quickly became my main method of improving my vision.
But despite their prevalence and the benefits they can provide, many people (myself included) wear contact lenses in a way that can compromise eye health, increasing the risk of damaged corneas and infection from microbes.
This week has marked the second annual Contact Lens Health Week – a week organized by the CDC to increase public awareness and promote healthy wearing and caring of contact lenses. In this Spotlight, we take a brief look at a few of the “do’s and don’t’s” of contact wear. In addition, we will have a look at some of the interesting “can’s and can’t yet’s” of new contact lens innovations.
Healthy habits mean healthy eyes
Although they are similarly effective at improving vision as glasses, contact Pc anti fog lens wearers can be more at risk of eye complications than those who use glasses. If wearers do not follow contact lens care instructions properly, they can put themselves at risk of serious eye infections that can lead to blindness.
The CDC have previously reported that between 40-90% of contact lens wearers do not properly follow their contact lens care instructions, which may explain why serious eye infections affect around 1 in 500 contact lens wearers each year.
Many people compromise their visual health due to bad habits when it comes to wearing contact lenses. While it is easy to manhandle glasses, contact lenses need to be afforded a greater level of care.
This means washing hands with soap and water and drying them comprehensively before ever touching contact lenses. Doing so prevents the transfer of germs from the hands to the lenses and consequently the eyes.
Exposing the lenses to water should be avoided as water can carry bacteria and other microbes that cause infection. With soft contact lenses, water can also alter the shape of the lens and potentially damage the cornea. As a result, contact lens wearers should remove their lenses before showering, swimming or using hot tubs, as tempting as it may be to keep them in.
One particular germ, an ameba called Acanthamoeba, is typically found in tap water as well as other water sources. If it causes infection (Acanthamoeba keratitis), patients can require a year or more of treatment, and possibly a corneal transplant.
Another bad habit that should be avoided where possible – unless prescribed by a doctor – is sleeping in contact PC super blue cut lens. In addition to making the eyes feel uncomfortable, sleeping in any type of lens increases the wearer’s risk of a corneal infection known as microbial keratitis by between four and five times.
Fast facts about keratitis
Keratitis is inflammation of the cornea, the clear tissue that covers the pupil and iris
Keratitis can be caused by infectious microbes or by minor injuries to the cornea
In severe cases, keratitis can permanently damage an individual’s vision.
This risk extends to the wearers of contact lenses that are designed to be slept in. Recently, the story of a man who went blind in one eye after sleeping in contact lenses for almost a week has come to the media’s attention.
“The kind of contacts I have are called ‘Night and Day’ contacts,” Chad Groeschen explained to USA Today, “and it was my impression you could leave them in for 30 days straight. I figured the less I was messing with my eyes, the better.”
While people can opt to use disposable lenses that are designed to be worn daily, many choose to wear lenses that last for longer periods and need to be stored properly when not in use. Unsurprisingly, many eye problems arise from bad habits pertaining to the storing of contact lens and associated products.
Contact lenses need to be kept clean if they are going to be used for multiple days. Lenses should be cleaned using a specific contact lens disinfecting solution and never water or saliva, as should the case that the lenses are stored in when not in use.
The CDC report that fewer than half of contact lens wearers report always cleaning their contact PC blue cut lens cases, and the number of moderate to severe lens-related infection could be halved if case cleaning practices were improved. Contact lens cases should also be replaced at least once every 3 months.
Contact lenses are stored in a purpose-built solution that is recommended by an eye care specialist. Contact lens wearers should stick to the recommended solution as the recommendation will be based upon the wearer’s eyes and medical history. Water should never be used, again due to the fact that it can increase the risk of infection.
Old solution in a lens case should never be “topped off” with new solution – instead, only fresh solution should be used. Solution can become contaminated with microbes that cause infections, and simply adding fresh solution to old solution reduces how effective it is at eradicating germs.
According to the results of a recent CDC study, these bad behaviors are incredibly prevalent. The Contact Lens Risk Survey was completed by approximately 1,000 contact lens wearers, and around 99% of respondents reported at least one behavior associated with an increased risk of eye infections.
“Good vision contributes to overall wellbeing and independence for people of all ages, so it’s important not to cut corners on healthy contact lens wear and care,” reports CDC Medical Epidemiologist Dr. Jennifer Cope. “We are finding that many wearers are unclear about how to properly wear and care for contact lenses.”
The following figures illustrate how prevalent some risky behaviors were among survey respondents:
Napping while wearing contact lenses – 87.1%
Showering while wearing contact lenses – 84.9%
Not replacing contact lens cases as frequently as recommended – 82.3%
Swimming while wearing contact lenses – 61.0%
“Topping off” contact lens solution – 55.1%
Sleeping in contact lenses overnight – 50.2%.
“Nearly one third of all wearers reported ever having experienced a contact lens-related red or painful eye that required a doctor’s visit,” the researchers write.
Considering how common contact lenses have become, the figures produced by the CDC’s study are significant, illustrating just how important it is that people become more aware of how contact lenses should be used and the impact bad practice can have on health.
The health problems that can be caused by risky contact lens behaviors may be enough to put some people off wearing them. However, there are a number of other benefits that specific types of contact lenses can provide that no other devices are able to.
Contact lens designs have become more sophisticated over time. While original products may have only been able to correct nearsightedness (myopia) and longsightedness, newer models of lens can be used to treat and monitor additional conditions that affect the eyes.
Orthokeratology, also known as Ortho-K, is a PC clear lens fitting procedure that offers a temporary degree of vision correction by changing the curvature of the cornea to improve its ability to focus on objects.
Altering the cornea’s curvature is achieved through the use of specially designed rigid contact lenses that are typically worn overnight. Ortho-K lenses are most commonly used to correct myopia.
Some people wear multifocal glasses because they have a condition known as presbyopia, whereby the eye’s ability to focus on nearby objects is lost. However, the condition can also be treated with multifocal contact lenses.
There are two main designs for these types of lenses. Alternating vision lenses have two distinct areas for short- and long-distance prescriptions. The pupil alternates between the two different prescriptions as the wearer’s gaze shifts up or down.
Simultaneous vision lenses involve the pupil looking through short- and long-distance prescriptions simultaneously. The two prescriptions can either be laid out in alternating concentric rings or blended together across the lens.
Presbyopia is one condition that a “smart lens” being developed by Google and Novartis should hopefully address. Last year, Novartis suggested that the use of technology such as noninvasive sensors and microchips contained within the lens could “provide accommodative vision correction” to restore the eye’s ability to focus.
Their smart lens might also provide benefit outside of visual health. Novartis stated that such a lens could provide a continuous measurement of glucose levels in diabetic patients and deliver this information to a mobile device using a wireless connection.
“We are looking forward to working with Google to bring together their advanced technology and our extensive knowledge of biology to meet unmet medical needs,” announced Novartis CEO Joseph Jimenez. “This is a key step for us to go beyond the confines of traditional disease management, starting with the eye.”
One of the most frequently repeated recommendations concerning contact lenses is that wearers should always follow the advice of their eye care providers. Unlike glasses, contact lenses are in direct contact with an opening into the human body, and as such there are far more things that could go wrong from a health perspective.
When used correctly, contact lenses can have a transformative effect on the wearer’s quality of life. The same can be said for when they are used incorrectly, only for wholly different and more unpleasant reasons.
It does not take much time to wash hands before handling lenses, to remove them before showering or to clean out a storage case properly, and yet by skipping these simple steps, thousands of contact lens wearers are putting their vision at risk. Follow the advice of eye care providers and vision can be protected for years to come.
Previously, Medical News Today reported on a study that suggested wearing contact lenses may alter the microbiome of the eye.
Once an optometrist has confirmed a diagnosis of myopia, several treatments are available. Speaking to an optometrist can help a person decide on the best option for them.
The sections below will discuss some of these treatment options in more detail.
Glasses and contact lenses
Glasses and contact lenses are the most common treatment options for myopia. An optometrist will order custom lenses that have the right prescription for that person. These will fit into the frame of the glasses and correct any nearsightedness.
Contact lenses are clear discs that sit on the surface of the eye. Like glasses, contact lenses are also customizable for different prescriptions.
Many people who do not like the look or feel of glasses will choose to have contact lenses, as they are a lot smaller and harder to notice. However, it is necessary to change and clean them regularly.
Orthokeratology
People with mild forms of myopia may benefit from a nonsurgical process called orthokeratology, or corneal refractive therapy. This treatment involves wearing a series of rigid contact lenses to reshape the cornea.
These lenses put pressure on the cornea to flatten it. This, in turn, changes how light focuses as it enters the eye. People tend to wear these contact lenses while sleeping.
This process can help people experience clear vision temporarily. However, it also carries a risk of eye infections.
Surgery
There are a couple of different types of surgery available to people who would rather not wear glasses, who want a more permanent solution, or who have severe forms of myopia.
One form of surgery is laser surgery, wherein an eye doctor will use a powerful beam of light to change the shape of the cornea.
Laser surgery adjusts how the eye focuses light, meaning that images that were once blurry should now be clear.
The surgery takes around 10 minutes per eye. This option can be expensive, but it is usually painless. Vision should return to normal within a day or so of the surgery.
However, it is normal to have occasional blurred vision or dry eyes for weeks or months afterward. Attending follow-up appointments after this procedure is important to make sure that the eyes are healing properly.
Other forms of surgery can involve placing a PC photochromic blue cut lens inside the eye, either in front of the person’s lens or in place of it. Eye doctors tend to recommend this form of surgery for more severe forms of myopia.
Prevention
Given that myopia has genetic links, it can be hard to prevent in people who have a history of nearsightedness in their family.
Spending time outside, in the daylight, could help lower the progression of myopia. Making sure not to spend too much time doing up-close work, such as reading or working on a computer, can also help.
Outlook
In most cases, myopia does not cause any further health problems. There are a range of treatments available that allow people to experience no symptoms of the condition in their daily lives.
For those who have more severe forms of myopia, it is important that they tell their optometrist about any changes in their vision. Without treatment, they could be at risk of developing additional eye problems, or even vision loss.
There is evidence that both genes and environmental factors, such as spending less time outdoors and more time indoors reading and using computers, can increase the risk of myopia. Before this study, however, it was not clear what the underlying molecular mechanisms were.
One way to observe the biological development of myopia or hyperopia is by altering the focal length of the eye in laboratory animals. Specialists can do this by placing a lens in front of the eye for several weeks.
Depending on the type of lens, the exposure causes the eye to develop to a length that is either too long or too short.
The scientists used this method in marmosets to study the development of myopia and hyperopia. They placed a PC photochromic lens in front of only one eye for up to 5 weeks and let the other eye develop normally for comparison.
|
|
|
|