Welcome, Guest |
You have to register before you can post on our site.
|
Forum Statistics |
» Members: 466
» Latest member: Charvab
» Forum threads: 1,441
» Forum posts: 2,615
Full Statistics
|
Online Users |
There are currently 15 online users. » 0 Member(s) | 14 Guest(s) Bing
|
Latest Threads |
Bedava Free Fire Hesap
Forum: My Forum
Last Post: Tanitim2025
01-01-2023, 01:02 PM
» Replies: 0
» Views: 0
|
Bedava Pubg Mobile Hesap
Forum: My Forum
Last Post: Tanitim2025
01-01-2023, 12:49 PM
» Replies: 0
» Views: 0
|
Bedava Hesaplar
Forum: My Forum
Last Post: Tanitim2025
10-20-2022, 07:51 AM
» Replies: 0
» Views: 0
|
Film izle
Forum: My Forum
Last Post: Tanitim2025
08-27-2022, 05:16 AM
» Replies: 0
» Views: 0
|
Ehliyet Sınav Soruları
Forum: My Forum
Last Post: Tanitim2025
08-14-2022, 03:13 PM
» Replies: 0
» Views: 0
|
Seo Hizmetleri
Forum: My Forum
Last Post: Tanitim2025
05-22-2022, 02:08 PM
» Replies: 0
» Views: 0
|
شراء عقار في تركيا
Forum: My Forum
Last Post: Tanitim2025
04-30-2022, 11:57 AM
» Replies: 0
» Views: 0
|
Propriété à vendre à Turq...
Forum: My Forum
Last Post: Tanitim2025
04-27-2022, 10:50 AM
» Replies: 0
» Views: 0
|
Apple benefits elma yemen...
Forum: My Forum
Last Post: Tanitim2025
04-16-2022, 10:23 PM
» Replies: 0
» Views: 0
|
CLOUD TÜRKIYE Bulutların ...
Forum: My Forum
Last Post: Tanitim2025
04-13-2022, 04:05 PM
» Replies: 0
» Views: 0
|
|
|
UChicago institute helps reassemble ancient, rare art from first to 6th centuries |
Posted by: ccffefd17 - 09-28-2021, 06:44 AM - Forum: My Forum
- No Replies
|
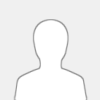 |
The worst was the Taliban’s effort in March 2001, when the group blasted away at the wooden buddha statue, one 181 feet and the other 125 feet tall, which at the time were thought to be the two biggest standing Buddhas on the planet.
When the Taliban seized power in Afghanistan in 1996, they imposed an extremist version of Islamic law across the country. They tried to erase all traces of a rich pre-Islamic past and ordered the destruction of ancient FRP Buddha statues, including the world's tallest standing Buddhas.
Those memories are still alive for millions of Afghans. And now they have become present concerns, as the US and Afghan government negotiate with the Taliban for a deal that could see them return to power in Afghanistan.
Many of these striking Buddhas hailed from Hadda, a set of monasteries in modern-day Afghanistan where Buddhism flourished for a thousand years before the rise of Islam. Located on the Silk Road, the area had frequent contact with the Mediterranean—hence the Buddha’s Hellenistic features. One of the richest collections of this unique art from Hadda was destroyed in 2001, when the Taliban ransacked the National Museum of Afghanistan and shattered the museum’s Buddha statues.
Nearly two decades later, the museum’s conservators are working with the University of Chicago’s Oriental Institute, one of the world’s foremost research centers on the civilizations of the ancient Middle East, to bring the collection back to life. Supported by cultural heritage preservation grants from the U.S. Embassy in Kabul, OI researchers, along with Afghan colleagues, are painstakingly cleaning, sorting and reassembling statues from the more than 7,500 fragments left behind, which museum employees swept up and saved in trunks in the basement. The ceramic buddha statue are beautiful, by all accounts. First excavated by French archaeologists in the 1930s, and spanning 500 years of Afghanistan’s history between the first and sixth centuries A.D., they are an example of a rare art form unique to the region, often called the Gandharan style. Some stand alone and others in tableaus, ranging from life-size to others that can fit in the palm of a hand. But the task of reconstructing them is more than a puzzle. Alejandro Gallego López, the OI’s field director in Afghanistan, explained the process of restoring the white marble buddha statue. First is to assess the collection—identifying and classifying features, such as archaeological motifs, and visible parts of bodies, like legs, heads or arms. This census can help them estimate how many objects there were originally (they think it was between 350 and 500).
|
|
|
How Fuel Injection Systems Work |
Posted by: ccffefd17 - 09-28-2021, 06:36 AM - Forum: My Forum
- No Replies
|
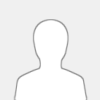 |
In trying to keep up with emissions and fuel efficiency laws, the fuel system used in modern cars has changed a lot over the years. The 1990 Subaru Justy was the last car sold in the United States to have a carburetor; the following model year, the Justy had fuel injection. But fuel injection has been around since the 1950s, and electronic fuel injection was used widely on European cars starting around 1980. Now, all cars sold in the United States have fuel injection systems.
At first, carburetors were replaced with throttle body FIAT fuel injector systems (also known as single point or central fuel injection systems) that incorporated electrically controlled fuel-injector valves into the throttle body. These were almost a bolt-in replacement for the carburetor, so the automakers didn't have to make any drastic changes to their engine designs.
Nox sensor - Tells the ECU the mass of air entering the engine
Oxygen sensor(s) - Monitors the amount of oxygen in the exhaust so the ECU can determine how rich or lean the fuel mixture is and make adjustments accordingly
The advantage of sequential vw fuel injector is that if the driver makes a sudden change, the system can respond more quickly because from the time the change is made, it only has to wait only until the next intake valve opens, instead of for the next complete revolution of the engine.
For more information on RENAULT fuel injector systems and other automotive topics, check out the links on the next page.
The call for reduction in pollution has been mandated by government′s policies worldwide. This challenges the engine manufacturer to strike an optimum between engine performance and emissions. However with growing technology in the field of fuel injection equipment, the task has become realizable. For past few years it has been the hot topic to improve combustion and emissions of compression ignition engines through optimizing the fuel injection strategies. Choosing between various injection strategies are potentially effective techniques to reduce emission from engines as injection characteristics have great influences on the process of combustion. For example, increasing the fuel injection pressure can improve the fuel atomization and subsequently improve the combustion process, resulting in a higher brake thermal efficiency, producing less HC, CO, PM emissions, but more NOx emission. Pilot injection help in reducing combustion noise and NOx emissions and immediate post injection may help in soot oxidation and late post injection helps in regeneration of diesel particulate filter. This article aims at a comprehensive review of various fuel injection strategies viz varying injection pressure, injection rate shapes, injection timing and split/multiple injections for engine performance improvement and emissions control. Although every strategy has its own merits and demerits, they are explained in detail, in view of helping researchers to choose the better strategy or combination for their applications.
|
|
|
Zirconia: Taking Dental Restorations to the Next Level |
Posted by: biw226 - 09-28-2021, 01:34 AM - Forum: My Forum
- No Replies
|
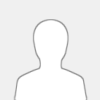 |
Since the introduction of porcelain-fused-to-metal (PFM) crowns in the 1960s, the dental industry has sought materials with both the esthetic value of porcelain, and the strength of noble metals to withstand the pressure of posterior occlusal forces.
Glass-ceramic materials that came along in the 1980s were confined to use on anterior teeth. In the early 2000s, researchers found that a toughened version of the metal zirconia met the strength requirements needed for posterior teeth, although the esthetics of the material left much to be desired.
Today, with improved technology, zirconia now rivals PFMs and all-ceramic restorations both for strength and beauty.
A member of the titanium family of metals, zirconia has multi-industry uses and is ideal for use in both anterior and posterior crowns where it fulfills functional requirements and can be custom shaded for quality esthetics.
Advantages
Zirconia is now the preferred material for crown and bridge fabrication, including implant-supported restorations. These are replacing metal-based restoration as the choice of most dentists, lab technicians, and patients. Because it can withstand occlusal forces without causing wear on opposing teeth, the material has quickly replaced full-metal and PFM’s as the material of choice.
Zirconia is more wear resistant than gold, retaining its shape and resisting the tendency to crack and erode by patients who brux. The flex strength value (MPa) of zirconia is more than twice that of traditional lithium disilicate (glass-ceramic) making it the ideal material for posterior crowns and bridges.
Recent Article: Benefits of Digitally Planned Implant Placement
While there is, as always with innovative technology, a learning curve for dentists new to working with zirconia, the techniques for tooth preparations is basically the same as for porcelain and glass ceramic materials. A more conservative preparation of the patient’s original tooth structure is a distinct advantage.
With zirconia, clearance may be as little as 1 mm, while lithium disilicate materials require 1.5 to 2mm and will not be as strong. A thicker chamfer is preferable to a feathered margin to provide for minimum thickness at the margin while retaining the ability to taper it to the prep.
Traditional impressions or digital impressions can be used with equal success.
Concerns
As with all new materials and technology, dental zirconia does have its drawbacks.
Many dentists are hesitant to use zirconia because there are fewer long-term research studies to assess its properties and compare the longevity of the material to gold, porcelain, and lithium disilicate. However, the studies completed thus far all reflect positively on the future of zirconia crowns.
There is also a lack of ability to bond the material to the preps. Though, that might be seen as an advantage by some, since only cement is needed to permanently seat the restoration. The hardness, while certainly considered one of zirconia’s advantages, might be a disadvantage when having to remove or access through them for endodontic treatment.
Recent Article: Why You Should Go Digital With IOS Dentistry
Chairside adjustments, while usually minimal, must be made safely, using diamond burs at slow speed with copious amounts of water, polishing wheels, and cones specifically designed for use with zirconia.
Do not use carbide burs or diamonds at high-speed for adjustments due to microscopic fractures that can occur from the impact of the burs on the material.
Ready to Try?
The future of zirconia use in dentistry is unlimited.
Gold and other noble metals used for decades are slowly dying out due to not only prohibitive cost, but also lack of demand by consumers. Zirconia more than fills that gap.
Researchers continually improve the translucency of these restorations, making them legitimate rivals to all-ceramic for beauty and surpassing other dental materials for strength and durability.
Here are First Choice Dental Lab, we specialize in all types of zirconia restorations, including full-contour and esthetic anterior.
Ship us your case today by clicking HERE, or send digital scans HERE to give zirconia restorations a try!
Want to learn more? Complete the form below and let us help you plan your next restoration!
Pre shaded zirconia has become popular with dental laboratories due to the time-savings and shade consistency the base shade provides. With pre-shaded zirconia there is no need for laboratory technicians to shade each unit in the green stage, saving production time and freeing them up to produce more units. However, standard pre-shaded zirconia systems require the dental laboratory to stock an inventory of 16 shades, each in a large selection of disc thicknesses to cover all unit shades and sizes. Furthermore, you can mill only one shade at a time, thus tying up your mill.
The ArgenZ Anterior Value Shaded Disc System is a collection of pre-shaded super translucent zirconia that covers all 16 shades of the VITA Classic shade guide with just six value-shaded discs. Each disc covers 2-3 shades based on value and chroma, requiring much less inventory and mill time. No green stage shading is required. You simply design, mill, sinter, and stain and glaze.
The discs are as follows:
? Disc 1: Shades A1, B1
? Disc 2: Shades A2, B2, A3
? Disc 3: Shades C1, D2
? Disc 4: Shades C2, D3, D4
? Disc 5: Shades A3.5, B3, B4
? Disc 6: Shades A4, C3, C4
Hue and Chroma Shading
Similar to the 16-disc shade systems, each ArgenZ Anterior Value Shade Disc group will be approximately one-half shade lighter than the lightest shade in that group. This makes it easy for the technician to change hue, adjust chroma intensity, and create a good incisal transition zone with external chroma stains.
Value
Traditional all ceramic systems are low in value, especially the light high value shades such as A1. The ArgenZ Anterior Value Shaded System is formulated to deliver a true value to match the guide.
Incisal Translucency and Appearance
The translucency of ArgenZ Anterior and the additional light refraction from the cubic ZR phase results in a natural incisal translucency requiring little to no incisal staining. Units with thicker incisals may require some minor incisal enhancement with incisal enhancement stains.
Stain and glaze system
Many companies make a low fusing fluorescent stain-and-glaze system designed primarily for all-ceramic systems. The most important stains in the kits are the A, B, C, and D chroma stains. These stains are essential to stain up to the next chroma or shade level in each shade group. Incisal stains or intensive blue stains can be customized with black, white, or violet to make any incisal enhancement color needed.
Firing Temperatures
Stains do not penetrate zirconia, so it is not necessary to fire above 800°C. The systems the author uses allow stains to be fired at 750°C (fully melting) and glazes to be fired at 730°C.
Die Shading System
Units must be seated on a die for final staining to match the shade guide. Due to the translucency of anterior zirconia, the final shade is slightly affected by light diffusion and the color of the underlying die and preparation. The anterior unit will appear to have a higher value and slightly more chroma when seated on a die.
Using a die color coating system to match preparation shades (stump shades) is recommended. Preparation coloring systems contain a variety of colors to match light to dark shades. If you do not have guidance on preparation colors (picture or preparation shade), match the die shade color to the prescribed base shade.
Glass Ceramic Materials
Glass ceramic materials have the same chemical compositions as glasses but differ from them in that they are typically 95-98% crystalline by volume, with only a small percentage vitreous. The crystals themselves are generally very small, less than 1μm and most often very uniform in size. Furthermore, due to their crystallinity and network of grain boundaries, they are no longer transparent.
Production of Glass Ceramic Materials
Glass ceramic components are formed using the same processes that are applicable to glass components. To convert them from a vitreous glass material into a crystalline glass ceramic material they must be heat treated or devitrified.
Devitrification can occur spontaneously during cooling or in service, but is most commonly incorporated to produce glass ceramics. It involves heating the formed glass product to a temperature high enough to stimulate crystals to nucleate throughout the glass. The temperature is then increased, which induces growth of the nuclei, crystallising the remaining glass.
Nucleation requires a critical number of atoms converging to form a nucleus. When the nucleus reaches critical size, nucleation occurs. In many glass compositions, nucleation is hampered by the fact the material is silica-based and highly viscous, making it difficult for the required atoms to come together. The crystal compositions can also be complex making nucleation difficult. These factors aid glass forming and cooling without crystallisation.
The devitrification heat treatment must be carefully controlled to ensure the maximum number of nuclei are formed and that these nuclei grow into a uniform fine crystal structure. In order to obtain a high concentration of nuclei throughout the structure, it is common to add a nucleating agent to the glass composition.
How are resin frameworks made? CAD design software is used to design the framework and then it is milled out using milling machines. The resin clasps engage the origin of the undercut rather than the terminal third to allow three to four times the retention of metal. In addition to a superior esthetic color, the resin clasps can be placed more gingival, further increasing its natural appearance.
Acetal dental can also be used for tooth shaded clasps on acrylic partials as well as a single and two tooth posterior unilateral partials. The latter situation is a great way to make an interim partial for a patient having implants placed.
For these reasons, we believe in recommending acetal resin to other dentists and our customers. It’s a strong, versatile material that has proven to be superior to using metal clasps and frameworks. We are committed to researching and finding the best products for our dentists.
Roland DGA Corporation’s three Diamond-Coated Dental Milling Burs, meant to be used with Roland’s DXW-50 zirconia milling machine, are specially engineered for precise performance, maximum durability, and longer life. Extensively tested for tolerances, Roland’s new milling burs are available in three different sizes – 2 mm, 1 mm and 0.8 mm – allowing dental professionals to choose an ideal tool for every milling strategy.
The proprietary design of every Roland Diamond-Coated Dental Milling Bur enables the user to produce up to 10 times the number of units that can be milled with a standard carbide model. Because they are fully compatible with Roland’s existing carbide tools, users can switch to the new tools without any changes in the CAM software, making the upgrade a true “plug-n-play” solution.
|
|
|
Cook Your Meat in a Beer Cooler |
Posted by: biw226 - 09-28-2021, 01:32 AM - Forum: My Forum
- No Replies
|
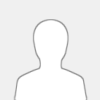 |
By this point, there is absolutely no question that the method of cooking foods at precise low-temperatures in vacuum-sealed pouches (commonly referred to as "sous-vide") has revolutionized fine-dining kitchens around the world. There is not a Michelin-starred chef who would part easily with their Polyscience circulators. But the question of when this technique will trickle down to home users—and it certainly is a question of when, and not if—remains to be answered.
The Sous-Vide Supreme, introduced last winter, and of which I am a big fan, is certainly a big step in the right direction. But at $450, for most people, it still remains prohibitively costly. In an effort to help those who'd like to experiment with sous-vide cookery without having to put in the capital, a couple weeks ago I devised a novel solution to the problem: Cook your food in a beer cooler.
"a beer cooler is just as good at keeping hot things hot as it is at keeping cold things cold"
Here's how it works: A beer cooler is designed to keep things cool. It accomplishes this with a two-walled plastic chamber with an air space in between. This airspace acts as an insulator, preventing thermal energy (a.k.a. heat) from the outside from reaching the cold food on the inside. Of course, insulators work both ways. Once you realize that a beer cooler is just as good at keeping hot things hot as it is at keeping cold things cold, then the rest is easy: Fill up your beer cooler with water just a couple degrees higher than the temperature you'd like to cook your food at (to account for temperature loss when you add cold food to it), seal your food in a plastic Ziplock bag*, drop it in, and close your beer cooler until your food is cooked. It's as simple as that.
How to Clean Your Beer Taps
One of the best options for cleaning your beer taps is to use a cleaning kit. A beer tap cleaning kit comes with all the equipment and chemicals you need to clean your system, and they come with easy-to-follow instructions. Instead of cleaning the taps themselves, many bar owners choose to use a cleaning service. Services are quick and convenient, and they ensure that your system is cleaned efficiently and regularly.
How Often Should Beer Lines Be Cleaned?
How regularly you should clean your beer tap system will depend on the volume of your business. High-volume nightclubs, sports bars, and banquet halls should clean their beer tap lines every week or two. Lower volume establishments only need to clean their draft lines every 2 or 3 weeks.
How to Tap a Keg
Beer Keg is an essential skill for bartenders. Here is how you can tap a keg in three easy steps:
- Attach the coupler to your gas cylinder. Make sure that you have the correct coupler for the beer you're serving, as using the wrong coupler can affect the gas pressure and how your beer pours.
- Open the gas valve and adjust the gas pressure. Most light beers, ales, and lagers should be dispensed at 10 - 12 PSI. Darker beers like porters and stouts should be dispensed at higher pressure levels, closer to 25 - 30 PSI.
- Take the dust cover off your keg. Attach your beer tap to the keg, ensuring that it is securely locked in place.
Common Problems and Solutions for Beer Tap Systems
Is there an issue with your beer tap system? Most issues with beer tap systems are a result of improper temperature, improper pressure, or cleaning issues. So before you call a technician next time you have an issue with your beer lines, check out this list of common problems and solutions.
How to Choose the Right Draft Beer Tower
There are many reasons one would want to upgrade their draft beer tower on an old kegerator or converted freezer. It might be that the kegerator you bought came with a cheap plastic tower. It may be that the tower you have does not have beer industry standard fittings. It may be that you want to serve something like Guinness? or cold brewed coffee and you need stout faucets to get the restricted flow necessary for that application. Maybe you find yourself filling taller glasses or growlers and need a tower with increased height to accommodate them. Perhaps you are tired of your faucets always being stuck and you're ready to switch to Perlick faucets for their forward-seat design that ensures smooth operation every time. You might just want to make sure that you have 100% stainless steel contact to make sure your system is as sanitary as possible and suitable for serving wine or cider.
Tower Options
Whatever the reason, Beverage Factory has a plethora of draft beer kegerator available with a host of finishes and an assortment of faucet options to choose from. We have basic single faucet towers all the way up to elaborate multi-faucet ceramic towers. We've got customizable T-Style towers that have the same column diameter as a standard kegerator tower, allowing you to easily switch them out with your existing tower.
Generally, switching out your tower is as easy as unscrewing your old tower and screwing in your new one. Something to consider would be how your tower is currently connected. If, for example, you have a 2.5" diameter tower or a tower with a base that screws into the top of your kegerator and you want to replace it with a tower that has a 3" diameter, you will need to drill new screw holes to attach the new tower to the top of your kegerator. The kegerators that we have seen do not have coolant lines in the top of the cabinet so you can be 99% sure you're not going to damage anything by drilling into the top, but if you want to be 100% sure, it's a good idea to call the manufacturer of the model you're working with to ask.
Another thing to consider is how wide the hole in the top of your kegerator is and if it will allow you to drop the beer line through the hole without removing the fittings on the end. If you are upgrading from a single faucet tower to a multi-faucet tower, you may not be able to push all the lines through without detaching one or all of the fittings. You can try pulling the nut back away from the end of the line to push the tube through and then squeezing the nut through afterward, but detaching and re-attaching the fittings may be the only answer. Usually, this just means removing the clamp that holds the beer line onto the hose nipple and then cutting the hose off to release the hose nipple and hex/wing nut that attaches it to your keg coupler. Once they are removed and the lines are pushed through the hole, you can re-attach them with a new clamp. If you are having a hard time getting the hose to slide over the hose nipple, putting the end of the hose in boiling water will make it more pliable. If, for some reason, you find that you cannot reuse the fittings you have removed, we have plenty of new fittings available.
There are a few kegerator brands out there that do not use industry standard parts, so our industry standard fittings may not fit on the non-industry standard coupler that came with your kegerator, but we've got plenty of new keg couplers as well.
[font=-apple-system, BlinkMacSystemFont, "Segoe UI", Roboto, Helvetica, Arial, sans-serif, "Apple Color Emoji", "Segoe UI Emoji", "Segoe UI Symbol"]Dispenser Types
With beer dispenser, the beverages are kept inside the pressurized kegs until you pull the tap lever and pour it. It isn’t magic that pulls the brew through the hoses, it is science. Kegerators dispense the beverages using either CO2 or nitrogen gas.
[/font]
CO2 is the most common option for home brewers and beer aficionados. The fermentation process creates a natural level of CO2 when making the beer. Using CO2 to lift the brew to the tap is completely flavorless and preserves the natural carbonation of the beer, helping it maintain freshness in the keg longer. This is closer to the direct-pour taste, right out of the keg.
Nitrogen dispensers are commonly associated with dark beers, like stout or porters, but also help preserve flavors in other beverages like wine or coffee. They produce smaller bubbles in the drink as it is dispersed and result in a “creamy” effect for some brews. When poured with a slow-pour, stout faucet, it produces a thicker foaming head on the beer.
Beer aficionados, coffee addicts, and wine connoisseurs, consider every detail in pursuit of their passions. How their drinks of choice are served can have an impact on flavor, and some cold beverages just taste better out of a tap. Kegerators keep beverages fresh, perfectly aerated, and always at the ideal serving temperature.
All it takes to experience your favorite on-tap drinks at home is a keg to pour from, the appropriate dispenser set up, and a refrigerator to keep it cool, which is exactly what you get with a beer kegerator. These specifically designed refrigerators not only hold multiple sized kegs of your chosen beverage, they do so at a specific temperature, alongside the tanks that allow it all to be dispensed directly from the keg, with just a pull of a faucet lever. It is the easy, classy way to enjoy your favorite beverage at home.
|
|
|
How to Pick A Lawn Mower |
Posted by: biw226 - 09-28-2021, 01:31 AM - Forum: My Forum
- No Replies
|
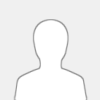 |
According to the U.S. Environmental Protection Agency (EPA), traditional gasoline lawn mower is a public nuisance to say the least. Using one of them for an hour generates as many volatile organic compounds—dangerous airborne pollutants known to exacerbate human respiratory and cardiovascular problems—as driving a typical car for 350 miles. The EPA estimates that, with some 54 million Americans mowing their lawns on a weekly basis, gas lawn mower emissions account for as much as five percent of the nation’s total air pollution. Beyond that, homeowners spill some 17 million gallons of gasoline every year just refueling their lawn mowers.
So what’s a green-minded property owner to do about keeping the grass down? Go electric, of course!
Electric mowers, which either plug into a wall outlet via a long cord or run on batteries charged up from the grid, create no exhaust emissions and run much cleaner than their gas-powered counterparts. They also need less maintenance, with no spark plugs or belts to worry about, and are easier to use, as they tend to be smaller and come with push-button starters. The icing on the cake might be the fact that electric mowers are cheaper to run, using about as much electricity as an ordinary toaster. Most electric mower owners spend about $5 a year on electricity to keep their grass trimmed just right. The non-profit Electric Power Research Institute reports that replacing half of the 1.3 million or so gas mowers in the U.S. with electric models would save the equivalent amount of emissions of taking two million cars off the road.
But going electric has some minor trade-offs. Electric mowers tend to cost up to $150 more than their gas-powered counterparts, and the plug-in varieties can only go 100 feet from the closest outlet without an extension cord. And the cordless models last only 30-60 minutes on a charge, depending on battery size and type, though that’s plenty sufficient for the average lawn (just remember to re-charge it in time for the next mow).
And, of course, just because electric mowers don’t consume fossil fuels or spew emissions directly doesn’t mean they are totally green-friendly. Most people derive their household electricity from coal-fired power plants, the dirtiest of all energy sources. Of course, running an electric mower on electricity generated from clean and renewable sources (solar, wind or hydro power) would be the greenest of all possibilities, and those days may be upon us soon.
In the market for a new lawn mower, but not sure which type is best? Let us help you navigate the debate on electric vs. gas lawn mowers.
With more lawn mower models on the market than ever before, and so many sizes, styles and features to consider, making the best choice isn’t as simple as it once was. And now, electric mowers are making a big splash in the lawn care industry.
Not long ago, mower motors required too much juice for a cord or batteries to be practical. Not anymore. Modern refinements and innovations allowed corded and battery-powered electric mowers, such as twin-battery mower, to burst onto the scene with gusto.
Gas-burning mowers ignite a mixture of air and fuel, compressing it in a cylinder, then igniting it with a spark to create a miniature explosion which is harnessed to power the machine. Electric mower motors, however, feature magnets interacting with electromagnets, energizing metal coils to move rotors and create power. Electric mowers can be powered by batteries or a 120-volt receptacle via extension cord.
Motor Power
Lawn mower manufacturers can be disingenuous about the real world power levels of their products. It’s not uncommon for electric mowers, for example, to have their “max torque” specs touted as evidence they match gas-burning models in power output. This is deceptive.
Max torque gives an inflated perspective of a mower’s true power because it measures engine torque under little or no load. The fact is, horsepower is the only reasonable unit of measure for lawn mowers, which I suspect is why electric mower manufacturers don’t share this figure. The real-world horsepower of most electric mowers is half, or less than half, the horsepower of a similarly sized gas-powered machine.
Run Time
It’s hard to measure exactly how much run time you’ll get from a tank of gas in your average fuel-burning mower, because much depends on the speed you run it and the density of the grass you’re cutting. It’s a safe bet, though, that a tank of gas will last longer than a fully charged battery on any equivalent electric model.
Most electric mower manufacturers give a maximum run time estimate, which for push and self-propelled mowers is almost always an hour or less. Riding electric mowers might run two hours, tops, on a single charge. Plug-in mowers don’t require batteries and will keep running continuously unless there’s a power outage. In that case, a generator with sufficient voltage capacity can keep you going.
The Environment and Noise
While power and run time certainly favor gas-powered mowers, noise and environmental considerations support electric. Battery-powered mowers have zero carbon emissions, so running one won’t contribute to climate change.
Noise is also a factor worth considering. Many municipalities regulate the acceptable amount of yard noise. Big, beefy gas-powered mowers can easily exceed these guidelines, but battery-powered mowers almost certainly won’t.
Note: Some users find vibration is more severe and bothersome with gas burning mowers than electric.
Operating and Maintenance Costs
Although it’s tempting to believe battery-powered mowers will always cost less than gas-burning mowers long-term, this isn’t necessarily the case. Although you’ll almost certainly spend less on electricity charging your batteries or running your corded mower then on gas and oil for your fuel-burning machine, there’s more to the equation.
Lithium ion batteries don’t last forever and eventually need replacement. They’re not cheap, either. If your electric mower comes with a generous warranty, you might be lucky enough to get a replacement battery (or batteries, if your mower takes two) for free when yours bites the dust. Otherwise, you could be looking at a $200 to $400 expense.
Ease of Use
Robotic lawn mower is usually simpler to use and maintain than their gas-powered counterparts. They don’t need gas, oil changes or new air filters, and you don’t have to make sure the carburetor and spark plugs are clean and functional.
Electric Lawn Mower Pros - Much quieter;
- Lower maintenance (no fueling, oil changes, belt replacements, air filter changes, etc.);
- Zero carbon emissions;
- Lighter weight (matters for push mowers you need to lift and store).
Electric Lawn Mower Cons- Battery power only lasts a couple hours (and often less) before requiring charging;
- Corded models can only be used near a power source, unless you have an extremely long extension cord;
- Extension cords are troublesome to lay out and roll up again for storage;
- Often have much less power than most equivalent gas-burning models;
- Replacement batteries are often expensive.
Gas Lawn Mower Pros- Generally much more powerful than electric mowers;
- Don’t require cords or batteries;
- Often built tougher;
- Replacement parts are often less expensive than those for electric mowers.
Gas Lawn Mower Cons- Considerably louder than electric mowers;
- More costly to run (unless you need to replace a battery outside the warranty period);
- Require more maintenance (oil changes, fuel preservative added during off-season, etc.);
- Generate carbon emissions.
How To Choose the Right Mower
Battery-powered mowers work best for people with small lots who want to minimize maintenance, noise and carbon emissions. But if noise and exhaust don’t bother you, and you just want to mow and be done with it as quickly as possible, you’re probably better off using gasoline engine.
Whether you go with gas or electric, it’s important to choose the right model for your needs. If you’ve got an acre or less to mow, a self-propelled walk-behind mower is probably your best bet. If you’ve got a larger lawn or simply don’t like walking and mowing at the same time, a riding mower will make your life much easier.
More detailed considerations like engine power, blade speed, deck width, regular range and other features come down to personal preference and available budget.
Cordless Lawn Mowers have taken over the lawn and garden section in many retail stores. Six years ago, Tool Box Buzz ran a Best Cordless Lawn Mower Head-to-Head test of five cordless mowers, so we were really interested in how the field of manufacturers has increased and how the offerings have changed after six years.
Our 2020 cordless lawn mower head-to-head will answer the question of whether cordless mowers’ performance “cut it” when compared to a gas-powered mower.
Why Cordless Lawn Mowers?
Even when operated correctly, gas-powered mowers require lots of service including oil changes, fuel filters, spark plugs, and air filters. Oftentimes people wait to do service until the mower won’t start! Anyone who has had to get a small engine repaired knows the hassle and time-sink that can be. Cordless mowers eliminate all of the above-mentioned maintenance, last-minute fuel purchases and they’re quieter to operate and do not emit fumes.
Landscaping on wheels. Thats what lawn and garden tractors provide. If you're serious about having a professional looking lawn, then you need to move beyond a simple mower. At this level, mowing becomes just one task out of many that you need to perform.
Enter the lawn tractor, a heavy-duty machine that lets you handle whatever curveballs your lawn throws your way, from dethatching, to aerating, to snow plowing. Keep reading to learn about the different types of lawn tractors and how to pick one.
How to Choose a Lawn Tractor
When deciding what kind of lawn tractor is best for your yard, you should consider what you'll be using it for. If you just need it for some light mowing on a small yard, then a standard lawn tractor will work fine. However, if you want to use heavier attachments for aerating, dethatching, or even tilling, then you'll need a heavy-duty garden tractor.
Two important factors to consider when shopping for the perfect lawn tractor are the grade and the deck size of the tractor.
1. Select a Grade
Lawn tractors can be grouped into the following grades:
Standard Lawn Tractors
Standard lawn tractors provide great power and versatility. They have twin cylinder engines for low-end torque and are a must if you intend to mow large areas or use any attachments on a regular basis.
Some tasks that lawn tractors can perform with the proper attachements include aerating, dethatching, spraying, spreading, and even snow plowing during winter.
Lawn tractors are designed with hydrostatic transmissions, which offer simple speed adjustments while driving. There are two hydrostatic transmission options: lever or pedal-operated. The pedal-operated option provides the most comfort and flexibility in speed.
Garden Tractors
Garden tractor is lawn tractors on steroids, capable of everything lawn tractors can do plus tilling, furrowing, towing heavier cart loads, and more. Their rugged decks, anti-scalp wheels, and powerful engines enable them to slash through tough brush.
They also include forged or cast iron axles, which are stronger and a good indicator of overall quality level. Finally, their larger back tires provide extra ground clearance and enhanced stability on slopes and inclines. However, if you're dealing with slopes greater than 15%, you should consider a tractor with a traction control system or locking rear differential.
|
|
|
Solar Water Pumps: Things To Know andTips For Use |
Posted by: biw226 - 09-28-2021, 01:28 AM - Forum: My Forum
- No Replies
|
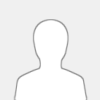 |
Mechanical pumps have a lot of uses nowadays. They are common in pumping water from wells, aquarium filtering, pond filtering and aeration. When it comes to water pumps, the main use of this device is the exchange of fluids such as water.
From agriculture to the energy industry, pumps are found in a wide range of applications. The main working principle of a water pump basically depends upon the positive displacement principle and kinetic energy which helps pushing the water.
Solar water pumps are a relatively new concept in mechanics. A solar water pump system is commonly seen in residential and commercial uses, as well as for irrigation of agricultural land. Through solar panels, the pump can eliminate the cost of energy and provide a more feasible option that uses energy from the sun (and not fuel-burning mechanisms) for pumping water.
Introducing solar-powered irrigation for poor and remote areas
In times when the entire world is switching to solar, using the sun’s energy in water pumping systems can significantly help and accelerate the development of agriculture in African countries and many other poor remote areas. This concept is known as solar-powered irrigation and is used in many regions nowadays.
The truth is, solar energy might be the easiest way for farmers to produce energy, especially for those living off the electricity grids with poor infrastructure around their homes. Therefore, the use of solar water pump in agriculture is becoming increasingly popular. The concept of solar irrigation represents a virtuous circle—when the sun shines, it feeds the irrigation system and feeds the crops which are dependant on water in sunny weather. Therefore, a large quantity of energy is being released right at the time when it is needed the most.
Solar irrigation is a concept that works through solar water pumps. Below, we are describing them in detail.
What is a solar water pump and what are the most popular types?
As we discussed before, solar pumps present a clean, simple and energy-efficient alternative to traditional electric and fuel-driven pump sets. They are part of an environmentally friendly approach in agriculture and can be used to exploit every region, whether its developed or poor.
Due to their immense potential for productive use and agricultural productivity, solar water pumps are now powering more and more agriculture projects. Knowing that 40% of the global population relies on agriculture as its main source of income, access to water remains an ongoing struggle for many people. This is what solar aims to change and introduce a cost-effective future for around 500 million small-scale farmers all around the world.
The main components in a solar pumping system include a photovoltaic (PV) array, an electric motor and a pump. Solar water pumping systems, on the other hand, are classified as either direct current (DC) or alternating current (AC) systems based on their motor’s ability. Recently, the concept of brushless DC (BLDC) motors for solar pumping water applications was presented as well.
Classification and types of solar pumps
When it comes to stand-alone solar pumping systems, the main types include rotating and positive displacement pumps or hybrid solar pump. Centrifugal pumps are the common choice for rotation and are designed for fixed head applications. Their output increases in proportion to their speed of rotation.
Additionally, pumps are also classified as submersible and surface pumps, based on their placement (underwater and above the waterline).
All in all, the main aspect related to the efficiency of a solar water pump is based on three variables including pressure, flow and input power to the pump. Wire-to-water efficiency is the commonly used metric that determines the overall efficiency of a solar water pump (as the ratio between the hydraulic energy that comes out of the pipe and the energy coming over the electrical wires through solar panels).
Why solar-powered water pumps are the ideal way to boost agriculture in remote areas (And Africa)
A solar-powered water pump is a concept that is environmentally-friendly. More importantly, it is a concept that gets rid of any power grids or fossil fuels used to pump water out of the ground. Below, we are listing the advantages and disadvantages of their use.
Advantages of solar water pumps
The first advantage of solar pumps is that they are reliable in regional and remote areas. A perfect example of this is Africa, which is one of the poorest remote regions in the world with an abundance of water—but also the most dominant region when it comes to most days of sun in the year. On the flip side, Africa is thought to possess 9% of the world’s freshwater resources which translates to around 4,000 km3 of water per year. Deploying solar water pumps in Africa is, therefore, the perfect alternative to any other fuel-based sources—and an alternative which can stimulate life in every part of this continent.
What Is the DC Submersible Pump?
The DC submersible pump as well as other types of submersible pumps look like a metal tube and their goal is to push the water to the surface. This type of pipe-look water pumps conceals the motor within the tube so that the liquid outside the pump does not get access to the electrical parts inside the pump.
The DC submersible pumps are versatile and can better accommodate with different working environments because they can be powered from a variety of independent DC power sources. The most common power sources for the DC submersible pumps are the solar modules, batteries, or generators. The DC submersible pumps with solar power supplies sometimes have a controller in order to enhance the current when the sunlight is low.
More Information on the Power Supply
Typically, the DC submersible pumps can operate on multiple volts of DC power such as 6V, 12V, 24V or 32V. There are some advantages of applying the direct current instead of the alternating current (AC). The first advantage is that the DC power system allows the submersible pumps to adapt to more power supply options such as batteries. It makes the machines portable and is more convenient to apply.
Also, the AC power system needs a controller to control the speed while the AC power system does not need such device. In most cases, the controller of the power system is only needed when the solar power modules are applied.
The DC submersible pumps are more energy efficient too; it takes less power to run a DC submersible pump than an Ac Dc submersible pump. However, there are limits to the DC machines as well. The DC submersible pumps have a shorter lifespan than the AC counterparts. Besides, though the DC machines are more energy efficient and easier to operate without a current controller, they tend to work in a rather lower speed and they are less powerful in pumping.
The Application of Submersible Pumps
The submersible pumps are applicable in multiple areas. For example, they can be used to pump sewage from the septic tanks and it is convenient because the pump deliver the sewage directly to tanks so that they can be transferred to treatment facilities and handled later on.
Secondly, they can be used both industrially and in buildings. Wherever there is too much unwanted water in a work site or when the basement of a building is flooded, the submersible pump can be applied to extract all the water out of the place easily.
The other common use of a submersible pump is for the oil wells. Whether it is an inland oil well or an offshore oil well, the submersible pump can pump out the oil from the ground and transfer it to the factory for further process. Some types of submersible pumps can also be used for drilling wells to a certain depth.
They are called the drilling pumps or borehole pumps. In addition to the industrial use, the submersible pumps can be used agriculturally as a part of the irrigation systems.
What Are the Advantages of a Submersible Pump?
The main goal of asubmersible pumpis to pump out liquids from the ground or from places under the surface level. The submersible pumps are best for job because of several reasons. For one thing, the submersible pump keeps almost all the components within the pipe-like body; therefore, it does not take up much space.
In other words, the submersible pumps can work best in a confined environment comparing to other types of pumps. The submersible pumps connect directly to the storage tanks with pipes or hoses which also take up very limited space as well. As a result, they accommodate with most working environments possible.
The other quality that the submersible pumps have which again comes from the design is that it is the safest options to operate among all other types of water pumps. Since all the working parts of the machine is contained within the body and the whole body will be in the pit of the work site, there is not much of a chance that the user around the machine gets hurt when it is running. This feature alone makes the submersible pumps stand out and become widely accepted.
Once again, because all the components are carried inside the pump body and they operate under the water in most cases, they do not make loud noises. Or to be specific, the noises made while the machine is running are all blocked by the water and the case of the machine. What’s more, the simplicity of the mechanism makes this kind of water pump more effective when it comes to pumping out liquids from underground.
In addition to the safety, the efficiency and the quietness a submersible pump have, the maintenance of the machine is also quite easy. In fact, it does not require much maintenance because the working parts and electrical components are all protected inside the case of the machine, the small contaminants are not likely to enter the body and harm the machine.
Moreover, because the submersible pumps are working in water, they are cooled by the water when running and the machine can last longer with this style of operation.
The application of the DC submersible pumps is mainly in the so called dewatering operations and because of the design and the power supply that they work with, there are a lot of advantages to the use of them.
The primary advantage of a DC submersible water pump is its convenience and ease of operation because the mechanism of the pump is simple and the power system allows more portability to the machine. If the users are looking for a reliable yet compact water pump with multiple power supply options, the Ac Dc screw submersible pump may just be the right choice for them.
|
|
|
What's New With Nonwovens in the Medical Industry? |
Posted by: biw226 - 09-28-2021, 01:27 AM - Forum: My Forum
- No Replies
|
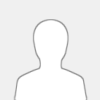 |
The utilization of medical nonwoven fabric has outpaced woven materials in recent years. Even when traced back to their rapid adoption during WWII, nonwovens were proven to be superior products in terms of adaptability, disposability, cost, and effectiveness. Manufacturing technology improved in the following decades until current-day use of nonwovens has placed them in a position to dominate the medical textile industry.
What are Nonwovens Fabrics?
Nonwovens are defined as sheets or web structures bonded together by the process of entangling fibers or filaments (and sometimes by perforating films) mechanically, chemically, or thermally. The fibers may be oriented randomly throughout the fabric or only following one direction.
Multiple layers may be combined to achieve the desired elongation, strength, and other mechanical properties. Porosity is controlled by varying fiber density, diameter, orientation, and the use of additional mechanical processing.
Key characteristics of nonwovens that justify their use and popularity:
durability
strength
resilience
dimensional stability
low elongation
specific processing to control porosity
Benefits of Nonwovens Driving this Market
With very deliberate care being taken to lower the incidence of hospital-acquired infection, nonwoven medical textiles are the clear winner in this category, thanks to their unique qualities. Medical textile technology is subject to intense monitoring since human lives are at stake. The intense scrutiny has resulted in better quality products and the development and implementation of innovative new uses in the medical field.
Nonwovens are preferred and poised to dominate the industry because they:
are effective barriers against bacteria
outperform linens for reducing airborne contaminants
can be tailored to changing specifications
help mitigate the risks of today's medical environments due to drug-resistant bacteria, worsening viral threats, polluted indoor and outdoor air, and increases in the numbers of blood-borne diseases
In 2014, nonwovens dominated the global medical textiles market. They accounted for over 55% of global volume, and are projected to gain market share through 2024 consistently.
What is SMS Material?
“SMS” stands for spunbond meltblown spunbond. SMS non woven fabric is a type of nonwoven fabric that combines spunbond and meltblown fabrics.When SMS material is created, it has great water repelling capabilities. This is why manufacturers choose to use SMS material in things like face masks, parts of baby diapers, sanitary napkins, and janitorial coveralls. It’s also used for caps, gowns, beddings, and other hospital accessories.
Why Combine Spunbond with Meltblown?
Spunbond polypropylene is a material that has great durability and strength, no matter if it’s wet or dry. It’s very resistant to fraying and is difficult to unravel, plus it barely absorbs any moisture if it becomes wet.
Meltblown, on the other hand, is softer and more pliable than spun bond polypropylene. Their main advantage is their web strength, which is why they’re usually combined with other nonwoven fibers. While spun bond polypropylene has its advantages, it can feel stiff and uncomfortable when it’s put in everyday applications such as coveralls.Since meltblown has a webbed structure and is softer, when you combine these two nonwoven fibers, it provides the wearer with water resistance while still retaining comfort. It’s also breathable, so even if you’re covered from head to toe (as with coveralls), your comfort won’t be compromised.
Applications for SMS Material
Because of how well SMS material repels water, it’s used in a number of industries where people need to block off fluids or other wet substances. Some areas that utilize SMS material’s benefits used are: - Protective apparel
- Cleanroom coveralls
- Filtration
- Insulation
- Medical healthcare
- Sanitary products
- Why The Future Is Nonwoven
Wherever you are sitting or standing right now, there’s bound to be at least one nonwoven fabric in your midst. Teabag or coffee filter, maybe? An air conditioning filter. Lens tissues, bleach wipes, diapers. Surely a face mask or seven.
Though the COVID-19 pandemic certainly pushed awareness of nonwoven fabrics to the forefront, we’ve had our eye on this growing market segment for years. Why? Because pressure-sensitive adhesive tape is often used to make or convert these textiles into usable everyday items.
Here’s our take on how non-wovens will continue to evolve and play a distinct role in the convenience economy.
What Is Non-Woven?
Nonwoven fabrics are the simplest and oldest textile fabrics. Neither woven nor knitted, as the name suggests, non-woven fabrics are broadly defined as sheet or web structures bonded together by entangling fiber or filaments (and by perforating films) mechanically, thermally or chemically.
They are flat or tufted porous sheets that are made directly from separate fibers, molten plastic, or plastic film. They are not made by weaving or knitting and do not require converting the fibers to yarn.
Typically, a certain percentage of recycled fabrics and oil-based materials are used in non-woven fabrics. The percentage of recycled fabrics varies based upon the strength of the material needed for the specific use. In addition, some nonwoven fabrics can be recycled after use, given the proper treatment and facilities. For this reason, some consider non-woven a more ecological fabric for certain applications, especially in fields and industries where disposable or single-use products are important, such as hospitals, schools, nursing homes, and luxury accommodations.
How are Nonwoven Fabrics Made?
Non-woven fabrics are made in two main methods: they are either felted or they are bonded. Felted non-woven fabric is produced by layering thin sheets, then applying heat, moisture, and pressure to compress the fibers into a thick matted cloth that will not ravel or fray.
There are there main methods of manufacturing bonded non-woven fabrics: Dry Laid, Wet Laid & Direct Spun.
In Dry Laid Non-woven Fabric manufacturing, a web of fibers is laid in a drum and hot air is injected to bond the fibers together.
In Wet-Laid, a web of fibers is mixed with a softening solvent that releases a glue-like substance that bonds the fibers together, and then the web is laid out to dry.
In Direct Spun, the fibers are spun on to a conveyer belt, and glues are sprayed on to the fibers, which are then pressed to bond. (In case of thermoplastic fibers, glue is not required.)
How are Non-Woven Fabrics Being Used?
Nonwoven fabrics penetrate a wide range of markets including medical, apparel, automotive, filtration, construction, geotextiles, and protective. Day by day the use of non-woven fabric is increasing and without them, our present life would be incomprehensible. Indeed, nonwovens play an integral role in the convenience economy.
Basically there are two types of nonwoven fabric: durable and disposal. Around 60% of nonwoven fabric is durable and the other 40% is disposal. These specialty fabrics are engineered to provide specific functions such as absorbency, sterility, liquid repellency, resilience, stretch, softness, strength, flame retardancy, cushioning, thermal insulation, acoustic insulation, and filtration. These properties are often combined to create fabrics suited for specific jobs while achieving a good balance between product use-life and cost. There are many kinds of it, such as non-woven fabrics for clothing, non-woven fabrics for packaging, and so on.
Non-woven fabric, is made of oriented or random fibers. It is a new generation of environmentally friendly materials. It is moisture-proof, breathable, flexible, light, non-combustible, easy to decompose, non-toxic and non-irritating, rich in color, and price. Low cost, recyclable, and so on. For example, polypropylene (pp material) pellets are used as raw materials, which are produced by high-temperature melting, spinning, paving, and hot-rolling and continuous one-step process. It is called cloth because it has the appearance and some properties of the cloth.
Therefore, in the non-woven fabric, S, SS,SSS, SMS mean the following:
S: spunbonded non-woven fabric = hot-rolled single-layer web;
SS: spunbonded nonwoven fabric + spunbonded nonwoven fabric = hot rolled from two layers of web;
SSS: spunbonded nonwoven fabric + spunbonded nonwoven fabric + spunbonded nonwoven fabric= hot rolled from three layers of web;
SMS: spunbond non-woven fabric + meltblown non-woven fabric + spunbond non-woven fabric = three-layer fiber mesh hot rolled
S and SS non woven fabric are mainly used for furniture, agriculture, hygenic products, and packaging products. And SMS nonwoven fabric is mainly for medical products, like surgical gowns. We are now exporting these non-woven fabrics to different countries in the world.
|
|
|
The Benefits of Stainless Steel Fittings |
Posted by: biw226 - 09-28-2021, 01:26 AM - Forum: My Forum
- No Replies
|
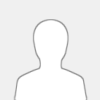 |
Stainless steel is a versatile material that is used in many different applications. The two most common types of stainless steel are austenitic which is highly corrosion resistant and ferritic which is magnetic.
In this blog we are going to break down the basics of what austenitic stainless steel is, the key benefits it provides and where the uses of stainless steel fittings can be most beneficial.
Stainless Steel
All steels have the same basic iron and carbon composition along with nickel, but stainless steel also contains chromium - the alloy that gives stainless steel its well-known corrosion resistance.
Austenitic stainless steel contains high levels of chromium and nickel and low levels of carbon providing a balance of strength, workability and corrosion resistance. The standard stainless steel alloys used in plumbing applications contains between 18-20% chromium and 8-12% nickel, as well as small amounts of carbon 0.08% and manganese 2%. Austenitic stainless steel has the highest corrosion resistance and are the most commonly used type of stainless steel around the world.
Stainless steel offers a wide range of benefits to the architect and designer of plumbing systems:
Material Benefits
The combining of corrosion resistance with high strength allows the reduction in wall thickness and weight. Stainless steel is resistant to heat and chemical damage. It can withstand very high flow rates - in excess of 40m/s, making it capable to withstand long-term exposure to the elements in almost any environment.
Environmental Benefits
Stainless steel can be used in all types of water, including drinking water in public supply. It has an excellent resistance to the full range of potable waters, including various chloride levels. At the end of its useful life, stainless steel is fully recyclable and retains a higher residual scrap value than ordinary steel.
Economic Benefits
Stainless steel is low maintenance and requires no additional coating, in both indoor and outdoor applications. The expected lifetime of a stainless steel system is more than 50 years, reducing system down time, replacement and maintenance costs over the life of the installation.
Stainless Steel Fitting Applications
With all the benefits that come with stainless steel there are equally just as many applications where stainless steel fitting can be utilized. Here are some key beneficial areas: - Residential & Commercial water systems that are subject to various stresses.
- Commercial & Industrial piping systems that are needing to perform well under the toughest and harshest conditions.
- Industrial Projects for sanitary or highly corrosive applications.
WHAT ARE THE BENEFITS OF USING STAINLESS STEEL VALVES?
There are many benefits of using stainless steel valve. There’s no doubt that stainless steel is a great material that is tougher than brass, copper, and cast iron when it comes to tolerating high pressures and temperature. Carbon steel is probably the only material that comes closest to stainless steel. Generally, stainless steel values have various applications due to their great performance in terms of temperature limits, corrosion resistance, and high-pressure tolerance.
APPLICATIONS OF STAINLESS STEEL BALL VALVES
Since stainless steel delivers phenomenally on all fronts, they are used in various industries. Here are a few applications of stainless steel ball valves.
OIL REFINING
Refining crude oil is a long and complicated process that is made much easier through the use of stainless steel ball valves. Crude oil may contain sulfur, carbon dioxide, and many microorganisms, which makes it an extremely corrosive substance. Over time, the constant movement of this substance can break down the metal of the valve. Therefore, you will need pipes and valves that can withstand corrosive crude oil for the longest time. Since stainless steel valves have very high corrosion resistance, they are the obvious choice of use in the oil refinery industry.
MARINE PROJECTS
Certain applications involving pipes and valves occur under or near seawater. Since seawater contains chloride and sodium, it is pretty corrosive to all materials, especially metals. That’s not all, marine environments naturally involve water, a substance that has a substantial impact on all metals.
In such applications, many prefer to use plastic valves since they are more resistant to water and other harsh chemicals compared to most metals. However, the main concern with using plastic valves is that they can’t withstand extreme temperatures and high pressures.
Stainless steel ball valves, on the other hand, have a high-temperature tolerance, are corrosion resistant, and can withstand high pressures. The only thing these valves require is proper maintenance to extend their lifespan under or around seawater.
BREWERIES
Stainless steel ball valves are widely used in breweries. These valves are typically situated on the kettle to help control the flow of liquid during transfers. The reason that stainless steel valves are a top choice in breweries is that during the mashing process, the valve comes into direct contact with a liquid known as wort, which is highly corrosive and can very easily wear down iron valves, and since plastic valves lack the ability to handle high temperatures, stainless steel valves are the best option.
WRAPPING UP
The industries mentioned above are just a few examples of the application that stainless steel valves have. These valves can be used in any process that involves the transfer of a corrosive, high temperature, or high-pressure substance such as gas or liquid.
Stainless steel 304 is one of the most common metals used nowadays. Stainless steel is well known and preferred over several other metals due to its physical properties including good corrosion resistance, durability, high strength, etc. Various types of commercial, industrial, and residential products are created using Stainless Steel. Stainless Steel 304 flanges are one of the most popular meteal products created out of this metal. There is a vast variety of flanges available for purchase. This article discusses eight important types of flanges and their uses.
Types of Stainless Steel Flanges
The following are the top 8 stainless steel flange used in stainless steel pipes:
- Weld Neck Flanges: Flange is distinguished by their protruding necks. The weld neck flanges have the same angle and thickness as that of the pipe. Weld Neck Flanges are considered best for use in severe service conditions such as sub-zero or high temperatures and high pressure.
- Slip-On Flanges: These are the most affordable range of flanges available for purchase. The slip-on flanges as the name suggests need to be easier to slip them over the pipe and hence they have a slightly larger diameter than the pipe. These stainless steel Slip On flanges are fillet welded to a position and are ideal for low-pressure applications.
- Blind Flanges: The flanges are designed without a bore, and are used to seal vessel openings or piping systems. Blind Flanges are ideal for use where the piping systems or vessels require constant inspection. The blind flanges can be supplied with or without hubs. This SS 304 Blind Flanges can easily handle high stress caused due to internal pressure.
- Threaded Flanges: Threaded Flanges also known as screwed flanges, and have a thread inside the flange bore which fits on the pipe with matching male thread on the pipe. Threaded flanges are used for special applications and can be easily assembled without welding. Stainless steel 304 threaded flanges are compatible with pipes with external threads.
- Lap Joint Flanges: The lap joint flanges are the type of slip-on flanges that are used with stub end fittings. Lap Joint Flanges are ideal for piping systems that require regular inspection and maintenance such as low alloy steel pipes or carbon steel pipes.
- Socket Weld Flanges: The flanges are designed for use on small diameter and high-pressure piping. The socket weld flanges have internal welds which contribute to their durability as well as endurance limit. These flanges are used in the chemical processing industry.
- Orifice Flanges: The function of these steel flanges is to provide access to a line for metering liquids or gases. The orifice flanges are installed with orifice plates or flow nozzles.
- Ring–Type Joint Flanges: These flanges are used for high pressure and temperature applications. The ring-type joint flanges has a specially designed grove that can be easily compressed on blind, slip-on or weld neck flange. The flanges help in avoiding leakages in pipelines where media is transferred at high pressure and high temperature.
|
|
|
Nonwovens for Home Textiles |
Posted by: biw226 - 09-28-2021, 01:24 AM - Forum: My Forum
- No Replies
|
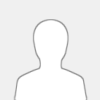 |
Nonwoven fabric is a fabric-like material made from lengthy fibers, bonded together by chemical, mechanical, heat or solvent treatment. In simple terms, they are textiles made from fibers or threads joined together without weaving. Nonwoven materials classically lack strength unless densified or toughened by a backing. In recent years, nonwovens have become an alternative to polyurethane foam.
Nowadays nonwoven fabrics are mostly used as home furnishing fabrics. Nonwoven fabrics are described as sheet or web structures bonded together by entangling fiber or filaments (and by perforating films) mechanically, thermally or chemically. They are flat, porous sheets that are made directly from separate fibers or from molten plastic or plastic film. They are not made by weaving or knitting and do not require converting the fibers to yarn. Typically, a certain percentage of recycled fabrics and oil-based materials are used in nonwoven fabrics. The percentage of recycled fabrics varies based upon the strength of material needed for the specific use. Conversely, some nonwoven fabrics can be recycled after use, given the proper treatment and facilities. For this reason, some consider nonwovens a more ecological fabric for certain applications, especially in fields and industries where disposable or single use products are important, such as hospitals, schools, nursing homes and luxury accommodations.
Nonwoven fabrics are engineered fabrics that may be a limited life, single-use fabric or a very durable fabric. Nonwoven fabrics provide specific functions such as absorbency, liquid repellence, resilience, stretch, softness, strength, flame retardancy, washability, cushioning, filtering, use as a bacterial barrier and sterility. These properties are often combined to create fabrics suited for specific jobs, while achieving a good balance between product life and cost. They can mimic the appearance, texture and strength of a woven fabric and can be as bulky as the thickest paddings. In combination with other materials they provide a spectrum of products with diverse properties and are used alone or as components of apparel, home furnishings, health care, engineering, industrial and consumer goods.
Types of nonwoven fabrics: Nonwovens, depending on the production process can be divided into:
? Materials produced by physicochemical methods; and
? Mechanically produced materials.
Materials produced by physicochemical methods
Most nonwoven materials, are made by binding fibers with adhesives. The most common glued materials are those based on fibrous cloth (a layer of textile fibers whose weight is 10–1000 gsm and more). The cloth is most often formed mechanically from several layers of combed fibers passing through the dotting drum of a combing machine. Fibrous cloth may be produced by the aerodynamic method in which the fibers are removed from the drum of the combing machine by a stream of air and transferred to a mesh drum (condenser) or a horizontal mesh with a maximum speed of up to 100 m/min, or by water dispersion of the fibers on the mesh of a paper machine.
A fibrous cloth is usually made of cotton, a mixture of viscose and polyamide fibers or the waste products of textile manufacture, including unspun fibers. The most common method of producing bonded nonwoven materials are to impregnate the cloth with a liquid adhesive or spraying/printing the adhesive over the surface of the cloth. Gluing the fibers includes saturate bonding and spray bonding or a latex adhesive is applied to the fibers and then the fabric is dried. The impregnated material is dried and treated in chambers heated by hot air or infrared radiation. The nonwoven materials made in this fashion (at a rate of 50 m/min and more) are used as interlacing and sealing materials, as heat and sound insulation materials for upholstery, bedding and drapery liners.
Melting fibers together can only be accomplished with synthetic, thermoplastic fibers or with a blend of fibers containing thermoplastic fibers or fusable powders. These methods include thermal bonding (heat applied to the web with or without pressure) a carded web, ther-mobonding a spunlaid web with a calendar, thermobonding a melt blown or flash spun web with a calender, thermal bonding a carded or air laid high loft web in an oven.In the hot-pressing process, the fibers are bonded by thermoplastics such as polyamides, polyethylene, and polyvinyl chloride at pressures of up to 2 mega newtons per sq m (MN/m2), or 20 kilograms-force per sq cm (kgf/cm2), at high temperatures, usually on special calenders. The bonding is preceded by thermal treatment of the fiber layer, which contains an adhesive that is applied to the fibrous cloth during its formation or after its formation.
In the spunbonded method, synthetic fibers are formed as they leave the spinnerets of spinning machines and pass through troughs in which they are stretched in an air current; they are then placed on a conveyor belt and form a sheet. The material formed in this way is most often bonded with an adhesive; in some cases the stickiness of the fibers themselves is sufficient.
SPUNBOUND/SPUNLACE
Spunlace nonwoven fabric is produced by depositing extruded, spun filaments onto a collection belt in a uniform random manner followed by bonding the fibres. The fibres are separated during the web laying process by air jets or electrostatic charges. The collecting service is usually perforated to prevent the air stream from deflecting and carrying the fibres in an uncontrolled manner. Bonding imparts strength and integrity to the web by applying heated rolls or hot needles to partially melt the polymer and fuse the fibres together. Since molecular orientation increases the melting point, fibres that are not highly drawn can be used as thermal binding fibres. Polyethelene or random ethylene-propylene copolymers are used as low melting bonding sites.
Spunbound products are employed in carpet backing, geotextiles, and disposable medical/hygiene products, automotive products, civil engineering and packaging products.
The process of Spunbound non-woven production tends to be more economical as the fabric production is combined with the fibre production.
AIRLAID
The process of airlaying is a non-woven web forming process that disperses into a fast moving stream and condenses them onto a moving screen by means of pressure or vacuum.
Airlaid fabrics is mainly composed of woodpulp and has a nature of absorbing well. It can be mixed with a definite proportion of SAP to improve its capabilities of absorbing wet. Airlaid non-woven is also referred to as dry paper non-woven. The nonwoven is made through the airlaying process. Transit the woodpulp into the bundle of airflow to make the fibres disperse and agglomeration on the floating web. Airlaid non-woven is reinforced of web.
Airlaid non-woven products are employed in a number of different products across a wide range of industry’s including; the interlining of clothes, medical and hygiene products, embroidery material and filter material.
DRYLAID
Dry laid webs are mainly produced using staple fibres natural or manmade. Dry laid webs formation mainly consists of 4 steps:
Staple fibre preparation –> Opening, cleaning, mixing & blending –> Carding –> Web laying.
Advantages of Drylaid non-woven production include; The isotropic structure of the web, voluminous webs can be produced and a wide variety of process able fibres such as natural, synthetic, glass, steel and carbon.
Drylaid non-woven products are employed by many products ranging from cosmetic wipes and baby diapers to beverage filtration products.
WETLAID
Wetlaid non-woven are non-wovens made by a modified papermaking process. That is, the fibres to be used are suspended in water. A major objective of wet laid nonwoven manufacturing is to produce structures with textile-fabric characteristics, primarily flexibility and strength, at speeds approaching those associate with papermaking.
Specialized paper machines are used to separate the water from the fibres to form a uniform sheet of material, which is then bonded and dried. In the roll good industry 5 -10% of nonwovens are made by using the wet laid technology.
Wetlaid is used for a wide ranging amount of industries and products. Some of the most common products that use wetlaying non-woven technology include; Tea bag paper, Face cloths, Shingling and Synthetic fibre paper.
NON-WOVEN CHARACTERISTICS
The particular set of properties that a printed nonwoven fabric may have is dependent upon the combination of factors in its production. Each different ttype of non-woven will consist of different characteristics.
The range of characteristics include
- The appearance of non-woven fabrics may be paper like, felt like, or similar to that of woven fabrics.
- They may have a soft, resilient hand, or they may be hard, stiff or broadly with little pliability.
- They may be as thin as thin tissue paper or many times thicker.
- They may also be translucent or opaque.
- Their porosity may range from low tear and burst strength to very high tensile strength.
- They may be fabricated by gluing, heat bonding or sewing.
- The drapability of this type of fabrics varies from goof to none at all.
- Some fabrics have excellent launderability; others have none. Some may be dry-cleaned.
Non-woven fabric is a material defined as
Sheet or web structures bonded together by entangling fiber or filaments (and by perforating films) mechanically, thermally or chemically.
Non-woven polypropylene fabric is, similarly, a thermoplastic polymer – like polypropylene – but made to look non-woven. One of its major applications is non-woven bags for shopping. Nevertheless, the non-woven fabrics gain more and more popularity in the fashion industry.
With so many plastic bags ban policies sweeping the world in their attempt to reduce plastic pollution, non-woven bags (either for shopping or for fashion) are becoming the norm. But are non-woven bags as eco-friendly as advertised?
Why Are Non-Woven Bags Environmentally Sustainable?
As we all know, the true sustainability of a product or a fabric resides in its recyclability and reusability. Just like canvas shopping bags or jute bags, non-woven carriers are reusable for very long periods. Polypropylene is recyclable, and so are non-woven polypropylene tote bags for shopping or drawstring bags for sports or leisure.
After years of use, you can throw away a broken, non-woven polypropylene office bag uses PP nonwoven fabric, for instance. As long it is collected and appropriately sorted, you can rest assured it will enter the recycling process and give life to a new item.
Non-woven bags for shopping come with plenty of eco-friendly advantages that are not available to plastic bags or natural fibers, for instance:
You can wash them and disinfect them without worrying about their resilience; as long as you wash it in cold water, your washing machine will not take its toll on it;
You can spray your non-woven bags with disinfectants and anti-bacterial substances for enhanced safety, especially during these times of global health concerns;
Both woven and non-woven polypropylene comes from recycled materials (plastic), so it is easy to understand why non-woven shopping bags come with high levels of sustainability. They are products of recycling and make products of recycling in their turn.
Before we move on to the next reason why non-woven bags are the sustainable answer to plastic bags, we have to say that no plastic whatsoever is biodegradable or ecologically friendly.
|
|
|
The evolution of plasma cutting |
Posted by: biw226 - 09-28-2021, 01:23 AM - Forum: My Forum
- No Replies
|
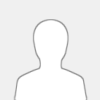 |
Plasma cutting has come a long way since it was first developed in the late 1950s by engineers at Union Carbide Corp. Today it is one of the most widely used metal plate cutting processes for a large variety of industries.
Early plasma cutting systems were used primarily for cutting stainless steel and aluminum plate from 0.5 to more than 6 in. thick. These systems, primitive by today’s design standards, were the most practical method for cutting heavy nonferrous plate. Most were mounted on XY cutting pantograph-style machines that used either photo-cell tracers to duplicate large black line engineering drawings of the parts to be cut, or a magnetic tracer to follow the path of a steel template.
Engineers continuously worked on the process throughout the 1960s with the goal of improving cut quality and the life of the consumable nozzles and electrodes in the cutting torch. Plasma began gaining momentum during this period as the process improved and as users became aware of its ability to cut complex shapes in nonferrous materials at very high speeds.
In 1968 radial water injection was introduced. This patented nozzle technology used pure water injected radially around the plasma jet to constrict the arc, increasing its energy density while improving nozzle cooling and thus allowing faster cut speeds, higher-quality cuts, and the ability to cut carbon steels at speeds four to six times faster than an oxyfuel cutting process.
At about that same time, XY coordinate drive cutting machine technology was being improved. Microprocessor control technology started to become the brains of the XY motion control machines, allowing for better accuracy, higher cutting speeds (necessary for the new-technology plasma systems), and higher levels of automation and productivity on the shop floor.
Through the 1970s plasma cutting technology replaced many oxyfuel-based steel cutting applications from 0.25 to 1 in. thick, while still maintaining its stronghold on the stainless and aluminum markets. While plasma could cut steel thicker than 1 in., the oxyfuel process still was a lower-cost alternative for heavier steel plate.
Timeline of Major Engineering Breakthroughs
With the baseline of plasma’s early history established, let’s take a look at some of the major engineering breakthroughs with this technology:
1957 The plasma cutting process was developed and patented by Union Carbide as an extension of the gas tungsten arc welding (GTAW) process.
1962-1967 Several new developments were completed in consumable design, and the dual flow torch was designed to help improve consumable life and cut quality on nonferrous materials.
1968 The water injection process was commercialized. This process allowed for cutting with clean, square-cut edges and faster speeds, as well as cutting of carbon steels with acceptable cut quality.
1970-1979 The water table and water muffler, designed to provide fume and smoke control, debuted. Automated arc voltage-based height controls for more consistent cut quality and longer consumable parts life emerged.
1980-1984 Oxygen-based plasma cutting systems that helped improve edge squareness and edge metallurgy (softer, weldable edge) and allowed for cutting carbon steels at lower power levels and higher cut speeds (see Figure 2) were introduced.
1984-1990 Many developments in the air plasma cutting process allowed for better portability and lower power levels for hand cutting and mechanized thin-sheet cutting.
1990 Better power supply designs using pulse width-modulated, current-controlled outputs were developed. Some systems started to use lighter-weight, smaller inverter technology power supplies suitable for portable, hand-held plasma systems.
1992 Long-life oxygen process technology was introduced. This was essentially a microprocessor-controlled method of controlling plasma gas ramping pressures as well as power supply output amperage. It helped increase typical oxygen plasma consumable parts life by four to six times; improved parts consistency; and helped lower the cost of plasma cutting.
1993 High-definition plasma, a technique that required the previous long-life oxygen technology to implement, was developed. This process allowed for a new nozzle design that increased the energy density of an oxygen plasma arc by as much as four times, allowing for squarer, cleaner cuts in all material thicknesses.
1996 Automated gas flow control systems emerged. They interfaced digitally with the machines’ CNCs. These gas flow controls eliminated some of the potential for machine operator-related errors in setting parameters for the cutting process.
1996-2006 Many developments occurred relating to improving cut quality and productivity and automating the many process cut parameters. These included integrated plasma, a system that closely coupled the CNC, the plasma power supply, the gas flow control, the CAM software, and the height control system to automate the process. With this expertise built into the system, the machine operator’s job became much simpler, and the process relied less on operator expertise.
Recent Technology Developments
In the last seven years, developments in plasma cutting technology have come at a fast pace. The latest revision on high-definition machines is their full integration with the CNC machines they are coupled with. New CNCs have touchscreen accessibility, minimizing the number of buttons involved in operating a plasma cutting machine and making operation as simple as almost any Windows?-based software. Operator training has been simplified on even the largest, most complex CNC plasma cutting machines.
The operator’s job also has been made easier with improvements in auto-calibrating height control functionality. The operator does not need to make adjustments as the consumable parts in the torch wear out.
Hole cutting has been improved with a large database of information in the CAM software that automatically recognizes CAD features and implements the best possible cut path and plasma cutting parameters, including on-the-fly shield gas changes that nearly eliminate the normal taper found in plasma-cut holes on steel (see Figure 3). This process is transparent to the machine operator and system programmer, eliminating the need for them to be experts.
Improvements in cut-to-cut cycle times have been incorporated into CAM software. The software automatically recognizes areas of a full cutting nest (multiple parts) and modifies the traverse time, torch retract time, and gas preflow time to decrease production times and improve product throughput.
Nesting software now applies the lead-in points in the most effective way to avoid traversing over areas prone to collisions with previously cut parts.
Improved plate beveling software has simplified the integration and operation of a bevel head with XY CNC cutting machines. This advancement, again associated with the system’s CAM software, saves much of the programmer/operator trial-and-error testing that has always been necessary to hold the best tolerances on plate edge beveling applications, such as weld prep.
Very new vented nozzle and gas mixing technology has helped improve stainless steel edge quality. Edges are squarer, shiny, and weldable.
Air plasma cutting systems from the major manufacturers also improved dramatically in terms of cut quality, consumable life, and duty cycles. These systems, primarily designed for portable and in-shop hand-held cutting applications, now are available with quick-change mechanized torches and interface easily to a variety of lower-cost CNC machines. Systems are available from a 30-amp, toaster-sized unit that operates on 120-V household current to sever materials up to 0.5 in. thick, to a 125-amp, 100 percent duty cycle industrial unit that can sever 2.25-in. materials. Both portable systems can be used with a hand torch or can be mechanized for a variety of automated cutting applications.
Industrial mechanized systems typically are 100 percent duty cycle, available with machine torches, and designed to use a variety of compressed gases to fine-tune the cut quality for different materials. These systems are available in various sizes and capacities from 130 to 800 amps.
Many other advances have been made to improve reliability, performance, consumable life, cut quality, and ease of use since the first plasma system was created. The process shares the cutting market with laser cutting, abrasive waterjet, and oxyfuel cutting, all of which deliver accuracy, productivity, and long-term cost-effectiveness when used for the appropriate applications.
What can be considered light duty?
A light duty plasma cutting machine can become a need for any workshop, artist, contractor, etc. that so far have been using oxy-fuel and is ready to make the leap to a better solution.
Actually, after experiencing a handheld plasma machine, almost nobody wants to return to oxy-fuel.
That is because even a light-duty plasma cutting system can make a big difference in efficiency and productivity.
So, in this post, we are going to consider what a light-duty plasma cutting system is and which one you should get.
But before getting into this amazing topic, let’s consider what plasma cutting is.
Most people classify plasma cutting systems in light, medium and heavy-duty. A handheld plasma cutting machine used in a small cutting table can be considered light-duty.
In general terms, a medium-size cutting table powered by some plasma cutting machine would be a medium-duty system.
A mechanized cutting system, which could occupy the heavy-duty slot, can be built in a stronger structure and composed by more than one cutting machine.
But that classification is not a general rule for plasma cutting manufacturers.
For the sake of this post, as quoted before, we are considering a handheld or portable plasma cutting machine as a light-duty one.
Now, before buying a light-duty plasma system, you may need to know when to use a portable and when to use an automated system. So, let’s consider some of it.
What Are The Advantages Of Fiber Laser Cutting Machine
Fiber laser is well received in the market now, because of its outstanding advantages of good beam quality and high conversion efficiency, it is widely loved in some finishing fields. At present, the proportion of fiber laser in the industrial field is close to 50%, which is also a kind of active choice for products in many industrial applications. Compared with traditional gas and solid-state lasers, fiber lasers have great advantages as frequency conversion light sources. In this article, we are going to talk about what is fiber laser cutting machine, what are the features, advantages & benefits of fiber laser cutting machine and applications & uses of fiber laser cutting machine.
What Is A Fiber Laser Cutting Machine?
Fiber laser cutting machine is a new type of machine in the world, which is used to output high energy density laser beam. The laser beam is concentrated on the surface of the workpiece, so that the area of ultra-fine focus on the workpiece is instantly melted and evaporated, and the spot is moved through the CNC mechanical system. Automatic cutting by illuminating the position. Compared with large volume gas laser and solid-state laser, it has obvious advantages and has gradually become an important choice in high-precision laser processing, lidar system, space technology, laser medicine and other fields.
The optical plate fiber laser cutting machine can be used for both plane cutting and oblique cutting, with neat and smooth edges. It is suitable for high precision cutting of metal plate. At the same time, the manipulator can replace the original five axis laser for 3D cutting. Compared with ordinary CO2 laser cutting machine, it saves more space and gas consumption, and has high photoelectric conversion rate. It is a new energy-saving and environmental protection product, and also one of the world’s leading technology products.
|
|
|
|