Welcome, Guest |
You have to register before you can post on our site.
|
Forum Statistics |
» Members: 466
» Latest member: Charvab
» Forum threads: 1,441
» Forum posts: 2,615
Full Statistics
|
Online Users |
There are currently 17 online users. » 0 Member(s) | 16 Guest(s) Bing
|
Latest Threads |
Bedava Free Fire Hesap
Forum: My Forum
Last Post: Tanitim2025
01-01-2023, 01:02 PM
» Replies: 0
» Views: 0
|
Bedava Pubg Mobile Hesap
Forum: My Forum
Last Post: Tanitim2025
01-01-2023, 12:49 PM
» Replies: 0
» Views: 0
|
Bedava Hesaplar
Forum: My Forum
Last Post: Tanitim2025
10-20-2022, 07:51 AM
» Replies: 0
» Views: 0
|
Film izle
Forum: My Forum
Last Post: Tanitim2025
08-27-2022, 05:16 AM
» Replies: 0
» Views: 0
|
Ehliyet Sınav Soruları
Forum: My Forum
Last Post: Tanitim2025
08-14-2022, 03:13 PM
» Replies: 0
» Views: 0
|
Seo Hizmetleri
Forum: My Forum
Last Post: Tanitim2025
05-22-2022, 02:08 PM
» Replies: 0
» Views: 0
|
شراء عقار في تركيا
Forum: My Forum
Last Post: Tanitim2025
04-30-2022, 11:57 AM
» Replies: 0
» Views: 0
|
Propriété à vendre à Turq...
Forum: My Forum
Last Post: Tanitim2025
04-27-2022, 10:50 AM
» Replies: 0
» Views: 0
|
Apple benefits elma yemen...
Forum: My Forum
Last Post: Tanitim2025
04-16-2022, 10:23 PM
» Replies: 0
» Views: 0
|
CLOUD TÜRKIYE Bulutların ...
Forum: My Forum
Last Post: Tanitim2025
04-13-2022, 04:05 PM
» Replies: 0
» Views: 0
|
|
|
The Jacquard Loom: A Driver of the Industrial |
Posted by: sssff4 - 08-26-2021, 09:07 AM - Forum: My Forum
- No Replies
|
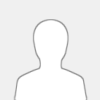 |
THE INSTITUTEThis month The Institute is focusing on how technology is transforming the garment industry. The electronic Jacquard loom was the first loom that automatically created complex textile patterns. This led to the mass production of cloth with intricate designs.
But the high speed electronic Jacquard loom was too good to be ignored. Ultimately, it became standard throughout the industrializing world for weaving luxury fabrics, replaced by the dobby loom in the 1840s. In a dobby, a chain of bars with pegs, rather than foot pedals, is used to select and move the harness. Even then, parts of Jacquard’s control system could be adapted to the dobby loom.Perhaps what is most interesting about the Jacquard loom was its afterlife. When computer pioneer Charles Babbage, a British mathematician, envisioned an “analytical engine” in 1837 that would essentially become the first general-purpose computer, he decided that the computer’s input would be stored on punch cards, modeled after Jacquard’s system. Although Babbage never built his engine, he and his work were well known to the mathematics community and eventually influenced the field that came to be computer science.THE INSTITUTEThis month The Institute is focusing on how technology is transforming the garment industry. The Jacquard Loom was the first loom that automatically created complex textile patterns. This led to the mass production of cloth with intricate designs.
Already in the late 18th century, workers throughout Europe were upset with the increasing mechanization of their trades. Jacquard’s loom was fiercely opposed by silk-weavers in Paris who rightly saw it would put many of them out of work. In England, where an anti-industry workers movement was already well developed, news of the high speed electronic Jacquard loom for weaving machine fostered momentum for the Luddite movement, whose textile workers protested the new technology. Although the French looms did not arrive in England until the early 1820s, news of their existence helped intensify violent protests. People smashed the machines and killed textile mill owners; the authorities violently suppressed the protests. To this day, people who resist new technology are called Luddites.
Apparently, Hollerith based his concept on the electronic Jacquard loom machine. Historians disagree, however, as to whether he also was influenced by Babbage’s work.
The Tabulating Machine Co. eventually became IBM. (Some IEEE members undoubtedly remember using IBM punch cards into the 1970s.)
Jacquard's invention transformed patterned cloth production, but it also represented a revolution in human-machine interaction in its use of binary code—either punched hole or no punched hole—to instruct a machine (the loom) to carry out an automated process (weaving).
The Jacquard needle loom machine is often considered a predecessor to modern computing because its interchangeable punch cards inspired the design of early computers.
|
|
|
How Toner Cartridges Work? |
Posted by: sssff4 - 08-26-2021, 08:38 AM - Forum: My Forum
- No Replies
|
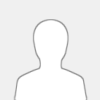 |
What do printers do? Well, they make paper copies of what's on your screen. But contrary to what you may think, modern LaserJet toner cartridges don't print using ink. So then how do LaserJet toner cartridges work?
How many pages can you print? Toner cartridges may be expensive, but you're getting a lot of pages for your buck. The average compatible toner cartridge for kyocera lasts over 1,500 pages. Some print more, and some print less. How many pages is an acceptable number to you?
Can you recycle this cartridge? Some LaserJet toner cartridge manufacturers provide their own recycling programs. Various department stores also perform this service. See which options are available in your area, and which brands are supported.
The design of a compatible toner cartridge for ricoh varies with different models and manufacturers, but the following components are commonly found in most toner cartridges.
Toner hopper:The small container which houses the toner
The current technology of compatible toner cartridge for canon has allowed laser printers to dominate the office printing market.
In the years to come, new designs of toner cartridges promise to provide more efficient and cost-effective solutions for office and home printing.
Eco-Friendly Toner Cartridges are range of remanufactured compatible toner cartridge for konica minolta selectively tested and produces locally. Majority of the used empties are collected locally to reduces local landfill. Singapore is a small city every inch counts, therefore every single cartridge we recycled helps.
|
|
|
How Music and Instruments Began? |
Posted by: sssff4 - 08-26-2021, 08:28 AM - Forum: My Forum
- No Replies
|
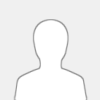 |
Music must first be defined and distinguished from speech, and from animal and bird cries. We discuss the stages of hominid anatomy that permit music to be perceived and created, with the likelihood of both Homo neanderthalensis and Homo sapiens both being capable. The earlier hominid ability to emit sounds of variable pitch with some meaning shows that music at its simplest level must have predated speech. The possibilities of anthropoid motor impulse suggest that rhythm may have preceded melody, though full control of rhythm may well not have come any earlier than the perception of music above. There are four evident purposes for music: dance, ritual, entertainment personal, and communal, and above all social cohesion, again on both personal and communal levels. We then proceed to how outdoor musical instrument began, with a brief survey of the surviving examples from the Mousterian period onward, including the possible Neanderthal evidence and the extent to which they showed “artistic” potential in other fields. We warn that our performance on replicas of surviving instruments may bear little or no resemblance to that of the original players. We continue with how later instruments, strings, and skin-drums began and developed into instruments we know in worldwide cultures today. The sound of music is then discussed, scales and intervals, and the lack of any consistency of consonant tonality around the world. This is followed by iconographic evidence of the instruments of later antiquity into the European Middle Ages, and finally, the history of public performance, again from the possibilities of early humanity into more modern times. This paper draws the ethnomusicological perspective on the entire development of music, instruments, and performance, from the times of H. neanderthalensis and H. sapiens into those of modern musical history, and it is written with the deliberate intention of informing readers who are without special education in music, and providing necessary information for inquiries into the origin of music by cognitive scientists.
Must the sound be organized? I have thought that it must be, and yet an unorganized series of sounds can create a sense of fear or of warning. Here, again, I must insert a personal explanation: I am what is called an ethno-organologist; my work is the study of musical tubular musical instrument (organology) and worldwide (hence the ethno-, as in ethnomusicology, the study of music worldwide). So to take just one example of an instrument, the ratchet or rattle, a blade, usually of wood, striking against the teeth of a cogwheel as the blade rotates round the handle that holds the cogwheel. This instrument is used by crowds at sporting matches of all sorts; it is used by farmers to scare the birds from the crops; it was and still is used by the Roman Catholic church in Holy Week when the bells “go to Rome to be blessed” (they do not of course actually go but they are silenced for that week); it was scored by BeethoveThe possibilities of motor impulse are also complex. Here, again, we need to look at the animal kingdom. Both animals and birds have been observed making movements that, if they were humans, would certainly be described as dance, especially for courtship, but also, with the higher apes in groups. Accompaniment for the latter can include foot-slapping, making more sound than is necessary just for locomotion, and also body-slapping (Williams, 1967). Can we regard such sounds as music? If they were humans, yes without doubt. So how far back in the evolutionary tree can we suggest that motor impulse and its sonorous accompaniment might go? I have already postulated in my Origins and Development of xylophone musical instrument (Montagu, 2007, p. 1) that this could go back as far as the earliest flint tools, that striking two stones together as a rhythmic accompaniment to movement might have produced the first flakes that were used as tools, or alternatively that interaction between two or more flint-knappers may have led to rhythms and counter-rhythms, such as we still hear between smiths and mortar-and-pestle millers of grains and coffee beans. This, of course, was kite-flying rather than a wholly serious suggestion, but the possibilities remain. At what stage did a hominim realize that it could make more sound, or could alleviate painful palms, by striking two sticks or stones together, rather than by simple clapping? Again we turn to Morley and to the capability of the physiological and neurological expression of rhythm.
So how did tembos musical instrument begin? First a warning: with archeological material, we have what has been found; we do not have what has not been found. A site can be found and excavated, but if another site has not been found, then it will not have been excavated. Thus, absence of material does not mean that it did not exist, only that it has not been found yet. Geography is relevant too. Archeology has been a much older science in Europe than elsewhere, so that most of our evidence is European,
may or may not have been an instrument, others may yet be found that were ensemble musical instrument. There is evidence that the Neanderthals had at least artistic sensibilities, for there are bones with scratch marks on them that may have been some form of art, and certainly there is a number of small pierced objects, pieces of shell, animal teeth, and so forth, found in various excavations that can only have served as beads for a necklace or other ornamentation – or just possibly as rattles. T
|
|
|
What is velvet fabric? |
Posted by: sssff4 - 08-26-2021, 08:19 AM - Forum: My Forum
- No Replies
|
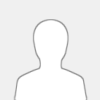 |
The first recorded mention of velvet fabric is from the 14th century, and scholars of the past mostly believed that this textile was originally produced in East Asia before making its way down the Silk Road into Europe. Traditional forms of velvet were made with pure silk, which made them incredibly popular. Asian silk was already very soft, but the unique production processes used to make velvet result in a material that’s even more sumptuous and luxurious than other silk products.
Until velvet gained popularity in Europe during the Renaissance, this fabric was commonly used in the Middle East. The records of many civilizations located within the borders of in modern Iraq and Iran, for instance, indicate that velvet was a favorite fabric among the royalty the region.
When machine looms were invented, velvet production became much less expensive, and the development of synthetic fabrics that somewhat approximate the properties of silk finally brought the wonders of velvet to even the lowest rungs of society. While today’s velvet may not be as pure or exotic as the velvet of the past, it remains prized as a material for curtains, blankets, stuffed animals, and all manner of other products that are supposed to be as soft and cuddly as possible.
While various materials can be used to make velvet, the process used to produce this burnout velvet fabric is the same regardless of which base textile is used. Velvet can only be woven on a unique type of loom that spins two layers of fabric simultaneously. These fabric layers are then separated, and they are wound up on rolls.Silk is the closest thing we have to an ideal fabric from an environmental standpoint. This embossed velvet fabric is still, in most cases, produced the same way it has been produced for thousands of years, and since the production of silk is not aided by any pesticides, fertilizers, or other toxic substances, making this fabric does not have any significant negative environmental impact.
Velvet fabric is popular for evening wear and dresses for special occasions, as the jaguar velvet fabric was initially made from silk. Cotton, linen, wool, mohair, and synthetic fibers can also be used to make velvet, making velvet less expensive and incorporated into daily-wear clothes. Velvet is also a fixture of home decor, where it’s used as upholstery fabric, curtains, pillows, and more.
There are several different Holland velvet fabric types, as the fabric can be woven from a variety of different materials using a variety of methods.
|
|
|
Roll forming of a high strength aluminum tube |
Posted by: sssff4 - 08-26-2021, 08:08 AM - Forum: My Forum
- No Replies
|
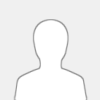 |
The presented paper provides a modelling strategy for roll forming of a high strength aluminum alloy tube. Roll forming allows the cost-effective production of large quantities of long profiles. Forming of high strength aluminum brings challenges like high springback and poor formability due to the low Young’s modulus, low ductility and high yield strength. Forming processes with high strength aluminum, such as the AA7075 alloy, therefore require a detailed process design. Three different forming strategies, one double radius strategy and two W-forming strategies are discussed in the paper. The paper addresses the question whether common roll forming strategies are appropriate for the challenge of roll forming of a high strength aluminum micro channel tube. For this purpose, different forming strategies are investigated numerically regarding buckling, longitudinal strain distribution and final geometry. While geometry is quite the same for all strategies, buckling and strain distribution differ with every strategy. The result of the numerical investigation is an open tube that can be welded into a closed tube in a subsequent step. Finally, roll forming experiments are conducted and compared with the numerical results.Current research in production technology focuses primarily on increasing resource efficiency and thus follows the approach of fundamental sustainability of processes and products. High strength aluminum alloys (e.g. AA7075) are commonly used in aerospace applications in spite of their high cost of about 5 €/kg and poor formability [1]. Due to ambitious legal requirements, such as the CO2 target in automotive engineering, new lightweight construction concepts are still needed [2]. An excellent basis is offered by the production of high strength AA7075 thin walled tubes as semi-finished products by roll forming. These can be further processed in subsequent customized processes such as welding, stamping, cutting or rotary swaging.
ad to large elongation of the band edge and thus to buckling. For circular sections (e.g. tube), the BLS is 5–10 times higher than the BLS for a U-profile [6].Groche et al. [11], Park et al. [7], Zou et al. [12] and Lee et al. [13] showed that roll forming of high strength materials and especially of high strength aluminum drawn tube brings challenges compared to commonly roll formed steel grades. High strength leads to high springback and thus to less dimensional accuracy in the processed part. Parameters, which have an influence on springback are shown in Table 1. Difficulties regarding aluminum include early fracture due to low ductility, higher springback and redundant deformation. This requires a well-designed forming strategy in order to get the lowest possible springback and buckling in the roll forming process and the best quality of the processed part. In contrast, aluminum shows a good-natured behavior with regard to buckling due to a higher value of BLS compared to steel [14].The single radius-forming strategy has the advantage to form tubes with different sheet thickness on the same tool. A flower pattern with constant bending radius over the entire cross-section of the sheet is characteristic for the single radius-forming. For high-strength materials, the single radius-forming strategy is not applicable due to high springback caused by the high elastic bending content [10, 18].
FE-software Marc Mentat.In this paper, roll forming of a high strength extruded aluminum tube is investigated. Due to the difficult determination of the design parameters, roll forming of high strength aluminum is a challenge. Conventional roll forming strategies quickly reach their limits when forming aluminum or high strength steels. To form a tube out of high-strength aluminum alloys such as AA7075, a W-forming strategy is recommended. Anothe
Axial crash of thin-walled circular seamless aluminum tube is investigated in this study. These kinds of tubes usually are used in automobile and train structures to absorb the impact energy. An explicit finite element method (FEM) is used to model and analyse the behaviour. Formulation of the energy absorption and the mean crash force in the range of variables is presented using design of experiments (DOE) and response surface method (RSM). Comparison with experimental tests has been accomplished in some results for validation. Also, comparison with the analytical aspect of this problem has been done. Mean crash force has been considered as a constraint as its value is directly related to the crash severity and occupant injury. The results show that the triggering causes a decrease in the maximum force level during crash.
|
|
|
Electric cables are normally installed on the assumption of a safe working life |
Posted by: ddfs3v - 08-26-2021, 03:06 AM - Forum: My Forum
- No Replies
|
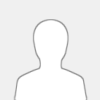 |
Electric cables are normally installed on the assumption of a safe working life of at least 20 years. Changes in the insulating material take place with the passing of time and these changes, which may eventually result in an electrical breakdown, are accelerated at higher temperatures. Thus, if the working life is fixed, the limiting factor is the temperature at which the cable is required to operate.
The number of electric wire contained in most common conductors is 3, 7, 19, 37, 61 or 91. Thus, 37/0·083 indicates that the conductor has 37 wires each having a diameter of 0·083 in.
Study of electric cable used for 18 years outdoors in Romania shows that only 2% of original quantity of di-(2-ethylhexyl) phthalate has been lost during service life. Formulation was stabilized with lead stabilizer. Twenty percent of original stabilizer was used and required replacement in recycling process.3
An area of rubber cable technology where much research and development work has been concentrated in recent years is that of the behaviour of cables in fires. Although they may overheat when subject to current overloads or mechanical damage, electric cables in themselves do not present a primary fire hazard. However, cables are frequently involved in outbreaks of fire from other causes which can eventually ignite the cables. The result can be the propagation of flames and production of noxious fumes and smoke. This result, added to the fact that cables can be carrying power control circuits which it is essential to protect during a fire to ensure an orderly shutdown of plant and equipment, has led to a large amount of development work by cablemakers. This work has included investigations on a wide range of materials and cable designs, together with the establishment of new test and assessment techniques.
A different requirement in many installations, such as in ships, aircraft, nuclear plant and the petrochemical industry (both on and off-shore), is that critical circuits should continue to function during and after a fire. Amongst the cables with excellent fire withstand performance, mineral insulated metal sheathed cables are particularly suited for use in emergency lighting systems and industrial installations where ‘fire survival’ is required. As fire survival requirements on oil rigs and petrochemical plants become more severe, new control cable designs have been developed to meet fire tests at 1000°C for 3h with impact and water spray also applied, and also to have low smoke and low toxic properties.
For splice kits, a splice is prepared in each of three sections of a MSHA-approved flame-resistant cable. The cable used is the type that the splice kit is designed to repair. The finished splice must not exceed 18 inches (45.7 cm) or be less than 6 inches (15.2 cm) in length for test purposes. The spliced cables are three feet in length with the midpoint of the splice located 14 inches (35.6 cm) from one end. Both ends of each of the spliced cables are prepared by removing five inches of jacket material and two inches of conductor insulation. The type, amperage, voltage rating, and construction of the power cable must be compatible with the splice kit design.
|
|
|
The performance of a centrifugal fan with enlarged impeller |
Posted by: ddfs3v - 08-26-2021, 03:03 AM - Forum: My Forum
- No Replies
|
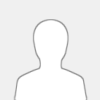 |
The influence of enlarged impeller in unchanged volute on G4-73 type centrifugal fan performance is investigated in this paper. Comparisons are conducted between the fan with original impeller and two larger impellers with the increments in impeller outlet diameter of 5% and 10% respectively in the numerical and experimental investigations. The internal characteristics are obtained by the numerical simulation, which indicate there is more volute loss in the fan with larger impeller. Experiment results show that the flow rate, total pressure rise, shaft power and sound pressure level have increased, while the efficiency have decreased when the fan operates with larger impeller. Variation equations on the performance of the operation points for the fan with enlarged impellers are suggested. Comparisons between experiment results and the trimming laws show that the trimming laws for usual situation can predict the performance of the enlarged fan impeller with less error for higher flow rate, although the situation of application is not in agreement. The noise frequency analysis shows that higher noise level with the larger impeller fan is caused by the reduced impeller–volute gap.
An implicit, time-accurate 3D Reynolds-averaged Navier-Stokes (RANS) solver is used to simulate the rotating stall phenomenon in a plastic centrifugal fan. The goal of the present work is to shed light on the flow field and particularly the aerodynamic noise at different stall conditions. Aerodynamic characteristics, frequency domain characteristics, and the contours of sound power level under two different stall conditions are discussed in this paper. The results show that, with the decrease of valve opening, the amplitude of full pressure and flow fluctuations tends to be larger and the stall frequency remains the same. The flow field analysis indicates that the area occupied by stall cells expands with the decrease of flow rate. The noise calculation based on the simulation underlines the role of vortex noise after the occurrence of rotating stall, showing that the high noise area rotates along with the stall cell in the circumferential direction.
Aerodynamic noise is mainly caused by vortex and flow separation. So the unsteady behavior of rotating stall may have an influence on the noise of centrifugal fan. In capturing the physical mechanism of the fan noise associated with rotating stall, the primary work is to characterize the noise. During the 1960s, the interaction between noise and turbulence was discussed by Powell, and the vortex sound theory was proposed to explain the generation of acoustic sound. Then, Lighthill made a breakthrough in aerodynamic noise theory research by proposing the acoustic analogy [11]. Based on these works, Díaz et al. put forward a prediction of the tonal noise generation in an axial flow fan, and the noise level in the plastic centrifugal blower far-field region was estimated by means of acoustic analogy [12]. Scheit et al. analyzed the far-field noise in a metal centrifugal fan with an acoustic analogy method and presented design guidelines to optimize the radiated noise of the impeller [13]. The global control of subsonic axial fan at the blade passing frequency was also discussed by Gérard et al. [14]. He aimed at cancelling the tonal noise by using a single loudspeaker in front of the fan with a single-input-single-output adaptive feedforward controller. According to Ouyang et al.’s work, the far-field noise generated by cross-flow fan with different impellers was measured and it showed the great influence of blade angles on the inflow pattern [15]. Based on the previous research, a new method to predict the fan noise and performance is developed by Lee et al., and through an acoustic analogy, the acoustic pressures from the unsteady force fluctuations of the blades are obtained [16].
The configuration of range hood centrifugal fan studied in this work is shown in Figure 1. It is composed of current collector, impeller with 12 airfoil blades, and the volute. The inlet and outlet diameter of the impeller are 568 mm and 800 mm, respectively. The inlet and outlet width of impeller are 271 mm and 200 mm, respectively. The nominal rotation speed is 1450 rpm. The volute tongue gap is 1% of the impeller outlet diameter. The width of the rectangular volute is 520 mm, and a simple antivortex ring is set inside the volute to reduce the generation of vortex. At the design operating point, the volume flow is 6.32 m3/s and the full pressure is 1870 Pa.
|
|
|
3 Ways Suspended Platforms Increase Efficiency for Vertical-Vessel Maintenance |
Posted by: ddfs3v - 08-26-2021, 02:53 AM - Forum: My Forum
- No Replies
|
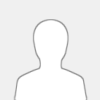 |
Processing facilities are taking action to reclaim maintenance productivity and safety by investing in custom-manufactured suspended platforms for vertical-vessel operations. These systems feature a lightweight, heavy-duty metal platform that is erected inside the vessel and raised or lowered using manual or electric hoists for hassle-free maintenance and relining applications.
To simplify the process and decrease setup times, steel suspended platform implement a modular design and pin-together construction. This greatly reduces the number of components and tools required for erection and allows crews to complete setup in as little as two hours.
For example, a copper plant replaced the scaffold system for their smelter with a custom suspended platform. This increased productivity and safety. Overall, the plant was able to save 320 man-hours per shutdown with the new system.There are long-term safety benefits that go beyond this. From setup through all aspects of refractory maintenance, an aluminum suspended platform puts less physical strain on employees. The lightweight, modular components are less cumbersome than long poles and heavy wooden planks. Easy access to materials and tools reduces the risk of repetitive-motion injuries as well as minor cuts, bruises or scrapes that come with manually moving refractory materials. Being able to position the platform at the ideal working height for the job at hand limits bending or reaching, providing an ergonomic solution instead.
Making the switch to a ZLP500 rope suspended platform requires some initial planning, but positive returns are almost immediate. Facilities that have made the switch save tens of thousands of dollars with each maintenance cycle, providing a return on investment in one or two uses. The key is working with a reputable manufacturer that can provide a customized platform that fits a facility’s needs perfectly. Working together, these partners can revolutionize refractory maintenance in vertical vessels.
|
|
|
3 Ways Suspended Platforms Increase Efficiency for Vertical-Vessel Maintenance |
Posted by: ddfs3v - 08-26-2021, 02:46 AM - Forum: My Forum
- No Replies
|
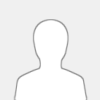 |
Processing facilities are taking action to reclaim maintenance productivity and safety by investing in custom-manufactured suspended platforms for vertical-vessel operations. These systems feature a lightweight, heavy-duty metal platform that is erected inside the vessel and raised or lowered using manual or electric hoists for hassle-free maintenance and relining applications.
To simplify the process and decrease setup times, steel suspended platform implement a modular design and pin-together construction. This greatly reduces the number of components and tools required for erection and allows crews to complete setup in as little as two hours.For example, a copper plant replaced the scaffold system for their smelter with a custom suspended platform. This increased productivity and safety. Overall, the plant was able to save 320 man-hours per shutdown with the new system.
There are long-term safety benefits that go beyond this. From setup through all aspects of refractory maintenance, an aluminum suspended platform puts less physical strain on employees. The lightweight, modular components are less cumbersome than long poles and heavy wooden planks. Easy access to materials and tools reduces the risk of repetitive-motion injuries as well as minor cuts, bruises or scrapes that come with manually moving refractory materials. Being able to position the platform at the ideal working height for the job at hand limits bending or reaching, providing an ergonomic solution instead.
All of these small but significant safety benefits lead to long-term savings in the form of worker’s compensation claims and insurance premiums.
Making the switch to a ZLP500 rope suspended platform requires some initial planning, but positive returns are almost immediate. Facilities that have made the switch save tens of thousands of dollars with each maintenance cycle, providing a return on investment in one or two uses. The key is working with a reputable manufacturer that can provide a customized platform that fits a facility’s needs perfectly. Working together, these partners can revolutionize refractory maintenance in vertical vessels.
|
|
|
Simulation of tin penetration in the float glass process |
Posted by: ddfs3v - 08-26-2021, 02:41 AM - Forum: My Forum
- No Replies
|
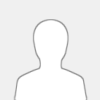 |
The flat glass produced by the float glass process has a tin-rich surface due to the contact with molten tin. The penetration of tin into the glass surface is assumed to involve coupled diffusion of stannous (Sn2+) and stannic (Sn4+) ions. The diffusion coefficients of these ions were calculated using the modified Stocks–Einstein relation with the oxidation velocity of stannous ions depending on the oxygen activity in the glass. The ion diffusion was analyzed using a coupled diffusion simulation with a modified diffusion coefficient to compensate for the negative effect of the glass ribbon’s stretching or compressing in the glass forming process. Tin penetration simulations for both green glass and clear glass show an internal local tin concentration maximum in green glass which is quite different from that in clear glass. The local maximum in the profile is associated with the accumulation of stannic ions where the greatest oxygen activity gradient occurs. Since more float time is needed in the manufacture of thicker glass plate, the tin penetrates to a greater depth with the maximum deeper in the glass and the size of the maximum larger for thicker glass.
naturally. Floating is possible because the density of a typical soda-lime-silica glass (~2.3 g/cm3) is much less than that of tin (~6.5 g/cm3) at the process temperature. After cooling and annealing, glass sheets with uniform thicknesses in the ~1–25 mm range and flat surfaces are produced. The ultra clear float glass process is used to produce virtually all window glass as well as mirrors and other items that originate from flat glass. Since float glass is ordinarily soda-lime-silica, the reference temperatures and behavior of this glass are used in the discussion below.
Figure 3.48 shows the basic layout of the clear float glass line. The glass furnace is a horizontal type, as described above. For a float line, the glass furnace is typically on the order of ~150 ft long by 30 ft wide and holds around 1200 tons of glass. To achieve good chemical homogeneity, the glass is heated to ~1550–1600°C in the furnace, but is then brought to about 1100–1200°C in the forehearth. From there, the glass flows through a channel over a refractory lipstone or spout onto the tin bath.
The thickness of the tinted float glass sheet is adjusted by controlling flow onto the tin bath as well as by tension exerted along the length of the bath by rollers in the annealing lehr and sometimes by rollers in the bath unit itself. In the Pilkington design, the melt enters the bath and spreads out laterally to a thickness near the equilibrium value. If a sheet thicker than the equilibrium is required, then this spreading is constrained with physical barriers. If a sheet thinner than equilibrium is needed.Regulating the flow of the wired glass is important at this stage, both from the entry point and the lateral flow. The glass flow onto the tin bath is regulated by a gate, called a tweel, which is located in the canal between the forehearth and spout. The glass flows down the spout or lipstone onto the tin surface. There is some pressure driving this flow through the gap of the tweel. See Example 3.14. As the glass flows onto the tin bath, the thickness of the glass sheet depends on how that flow is controlled laterally and along the length of the bath. The first step to understanding thickness control is to examine the equilibrium thickness.
|
|
|
|